Guogao Mine Machine
Professional Mineral Processing Equipment supplier
Gold ore, Copper ore,Lithium,Tantalite,Diamond,Gem, Barite, Silver ore,etc.
Aggregate crushing, Grining mill Plant.
Our Services
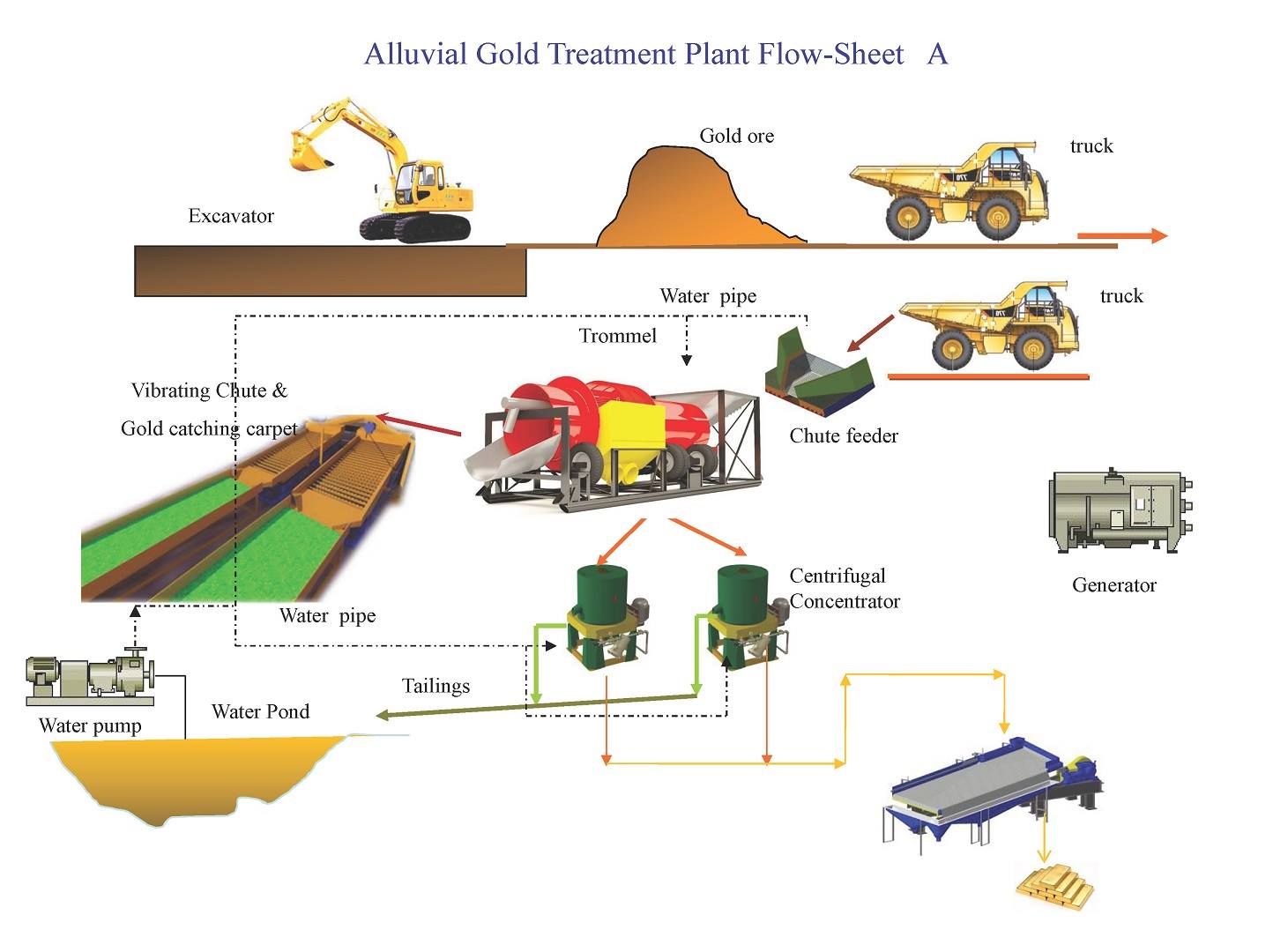
The placer gold mine has a very low gold content, and it is commonly referred to as gold panning. The process involves using various energy-efficient equipment specifically designed for extracting gold from placer deposits.
Placer gold mining
Placer gold deposits are typically extracted through methods such as gold dredging, hydraulic mining, excavation, and underground shaft mining.
Placer gold wash plant
– Washing ore. Separate gravel, sand, and soil to remove the fine mud adhering to the gravel.
– Screening. Remove large pieces of gold-free stones from the cleaned alluvial gold ore to enhance the efficiency of gold beneficiation.
– Gravity separation. The presence of coarse gold concentrates in this process directly impacts the overall results of placer gold beneficiation.
– Concentration. Depending on the type of alluvial gold mines, methods such as gravity separation and amalgamation can be employed to further increase the content of gold concentrate.
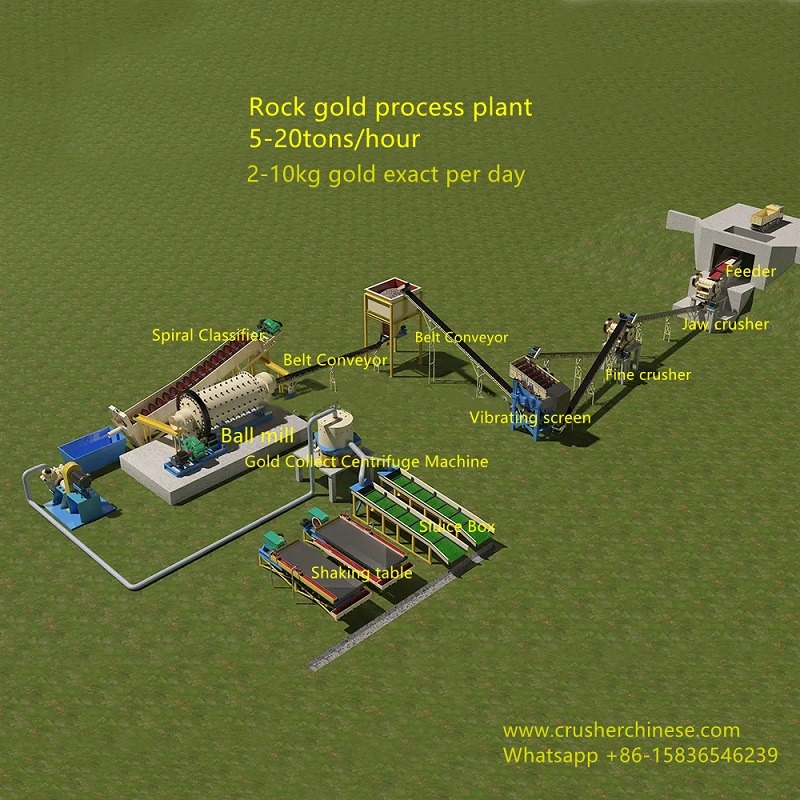
Rock Gold Mining Gravity or Flotation Extraction Process
Gravity beneficiation refers to the process of separating gold ore based on mineral density and plays a crucial role in modern mineral processing techniques. The primary equipment used for gravity separation includes crusher,ball mill,Gold Gravity concentractor, chutes, shaker tables, mineral jigs, hydrocyclones, and more.
Flotation process is commonly employed for the processing of lode gold. It typically yields favorable results when applied to sulfide-containing gold ore with high floatability.
Furthermore, the flotation process is utilized for polymetallic gold-bearing ores, such as those containing gold-copper, gold-lead, or gold-copper-lead-zinc-sulfur.
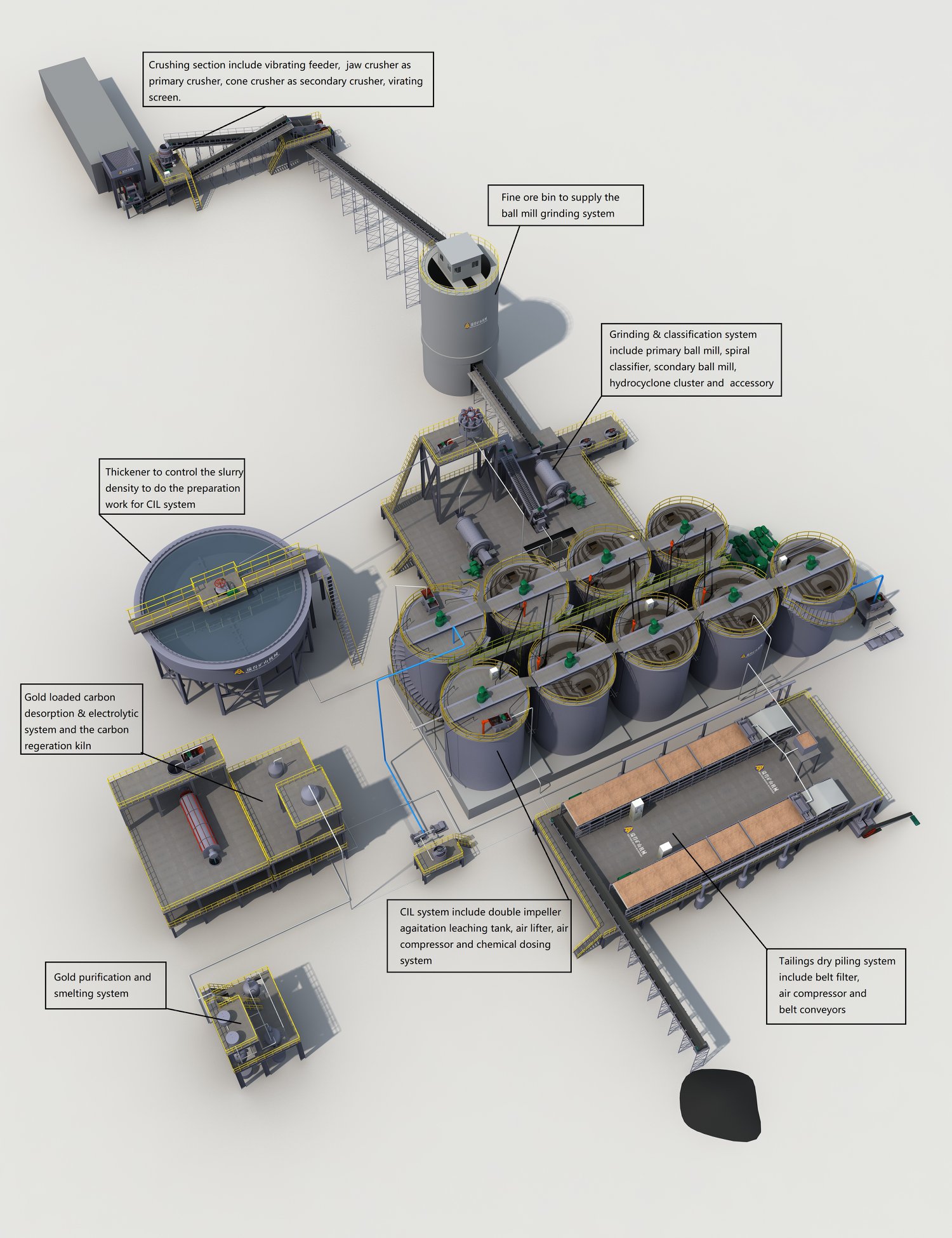
Chemical Method
There are two methods for extracting gold: Amalgamation and sodium cyanide process.
The amalgamation process is an old, simple, and cost-effective method for recovering coarse-grained gold. However, it causes pollution to the environment and has been gradually replaced by gravity separation, flotation, and cyanidation processes.
The cyanidation gold extraction process involves leaching with cyanide, washing and filtering the cyanide pulp, extracting gold from the solution or pulp, and smelting. The Gold CIL (Carbon in Leach) Process is a highly efficient method for extracting and recovering gold from its ore.
CIL Gold Processing
Leaching Pulp Preparation
Cyaniding Leaching and Carbon Adsorption
Carbon Acid Regeneration
Pulp Agitation
Gold Loaded Carbon Desorption
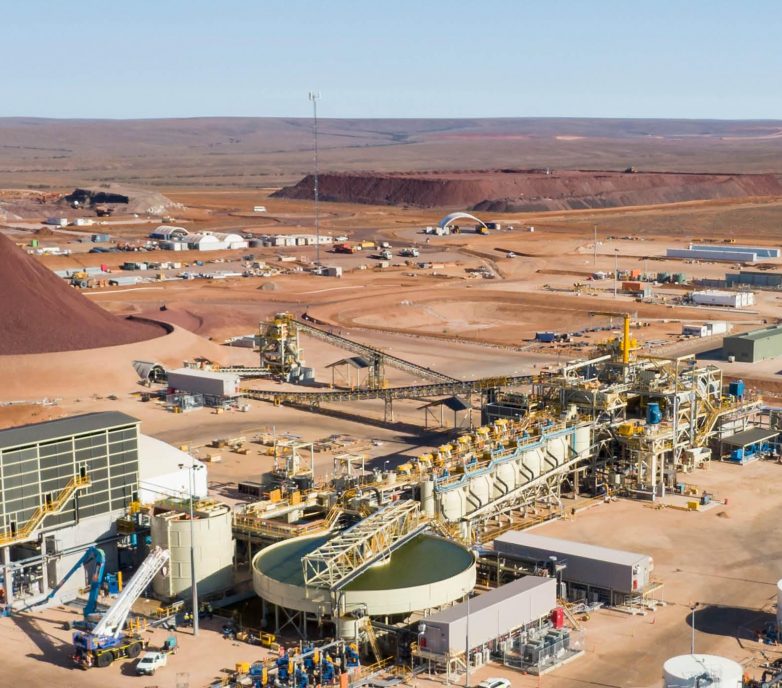
Copper industrial minerals include natural copper, chalcopyrite, chalcocite, tetrahedrite, azurite, malachite, and more. Chalcopyrite is the primary compound mined, followed by chalcocite and bornite.
To fully utilize copper ore, it must undergo flotation processing. Flotation separation is a crucial process in the current mineral beneficiation market for copper ore. By understanding the characteristics of the ore, we can tailor a suitable processing plant and equipment.
Copper Concentrate Processing Plant
Copper ore is categorized into sulfide ore, oxide ore, and mixed ore based on its oxidation rate. The primary technological process for copper ore is flotation. For refractory mixed copper ore and refractory oxide ore, the hydrometallurgical process is generally utilized.
The beneficiation process of copper ore relies on the physical and chemical properties of different minerals present in the copper ore. After crushing and grinding the ore, various beneficiation processes such as gravity separation, flotation, magnetic separation, electric separation are employed to separate valuable minerals from gangue minerals while keeping associated useful minerals separated from each other as much as possible. This process aims to remove or reduce harmful impurities in order to obtain raw materials suitable for smelting or other industries.
Preparation process prior to separation
Crushing procedure
Grinding procedure
Screening and classification
Flotation Process
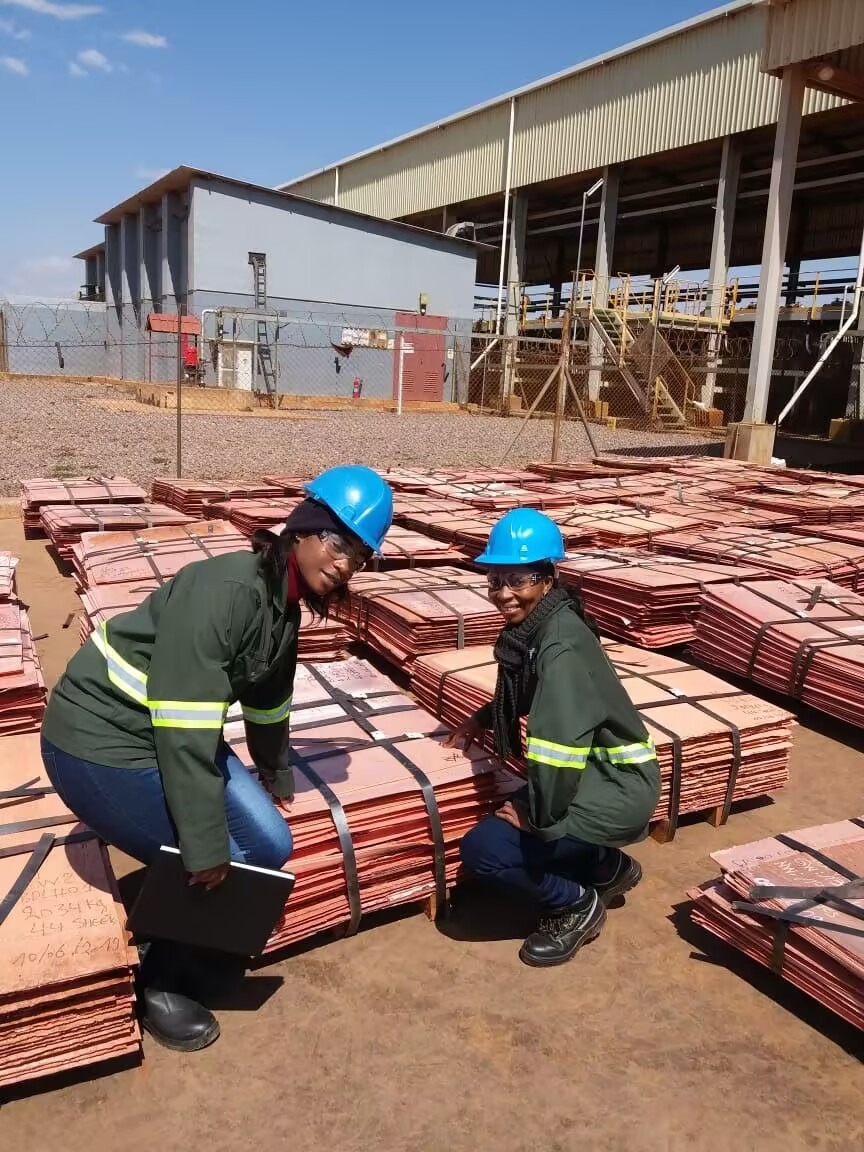
Copper Production from copper OxideOre to Finished Product
From its original home buried underground in a mine to its use in a finished product such as wire or pipe, copper passes through a number of stages. When it is recycled it can pass through some over and over again. Below is a quick description of the path.
Mining, Crushing
The beginning for all copper is to mine sulfide and oxide ores through digging or blasting and then crushing it to walnut-sized pieces.
Grinding
Crushed ore is ball or rod-milled in large, rotating, cylindrical machines until it becomes a powder usually containing less than 1 percent copper. Sulfide ores are moved to a concentrating stage, while oxide ores are routed to leaching tanks.
Leaching, Exacting
Oxide ore and tailings are leached by a weak acid solution, producing a weak copper sulfate solution.
Electrowinning (SX/EW)
The copper-laden solution is treated and transferred to an electrolytic process tank. When electrically charged, pure copper ions migrate directly from the solution to starter cathodes made from pure copper foil. Precious metals can be extracted from the solution.
Cathodes of 99.99% purity may be shipped as melting stock to mills or foundries. Cathodes may also be cast into wire rod, billets, cakes or ingots, generally, as pure copper or alloyed with other metals.
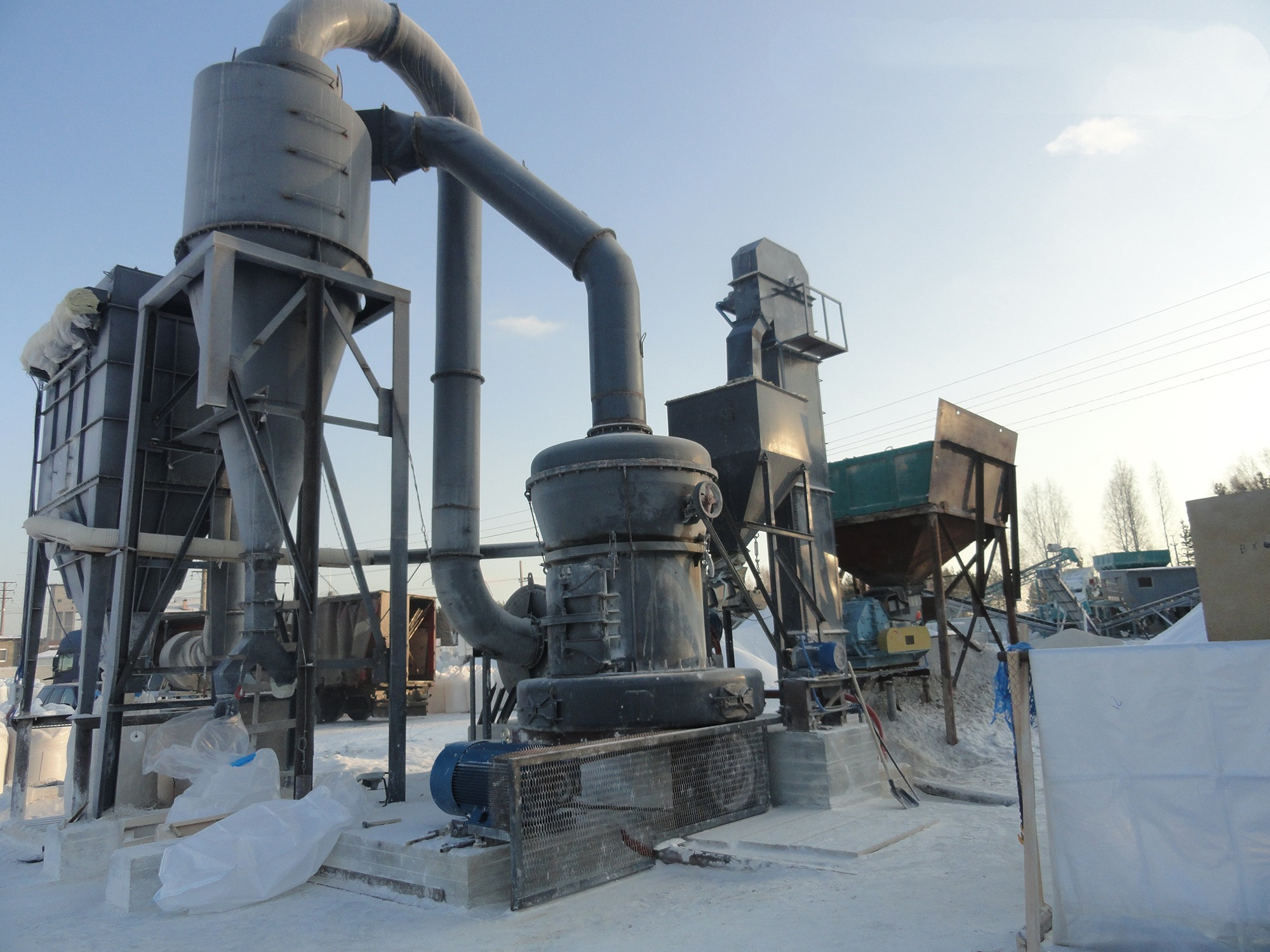
Composition of powder grinding line
The powder grinding line is equipped with various machines such as a jaw crusher, hopper, bucket elevator, classifier, dust collector, high-pressure mill, reducer, vibrating feeder, and air-blower.
It has simple technical procedures and low investment costs. Additionally, it has a profitable market which greatly promotes the grinding business both domestically and internationally.
Handling materials in the powder production line:
It can grind non-flammable and non-explosive minerals with a hardness below grade eight and moisture content below 6%. These minerals include feldspar, calcite, talc, barite, fluorite,rare earths , marble,c eramics , bauxite,manganese ore , phosphate ore,silica sand,and activated carbon.
he grinding technology is advanced, with high-quality and reliable machines that have a cost-effective and durable service life.
The grinding process is simple, with a large ore processing capacity resulting in over 40% increased output.
The efficiency of the entire production line is extremely high, ensuring safe and stable operation with an exceptionally low failure rate.
It has low energy and electricity consumption, minimal resource waste, low investment costs, and high profitability.
It achieves a good grinding effect with a high powder yield. The finished powder has uniform fineness and fewer impurities.
Powder grinding flow:
The powder grinding flow typically consists of three phases: crushing, grinding, and collecting. The main phase involves using a grinding machine for processing.
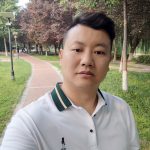
Tell us about your mining site and we can quickly recommend solutions to help maximize your benefits.
Because we are a professional provider of various mining equipment such as gold mines, copper mines, lithium mines, etc.
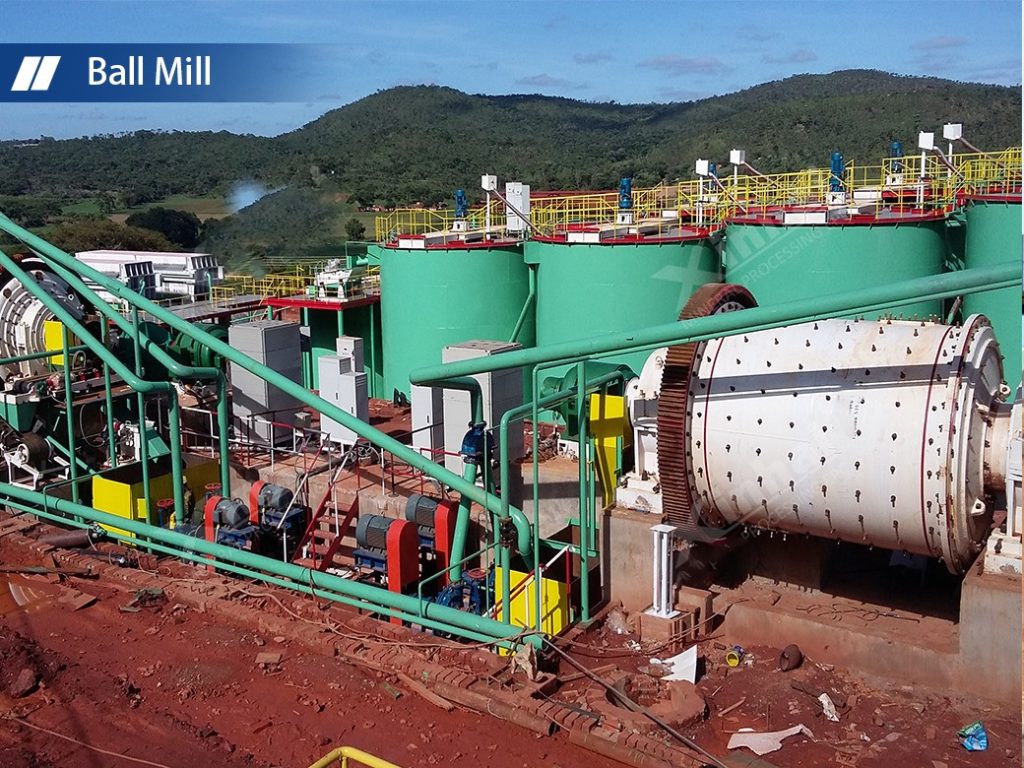