our services
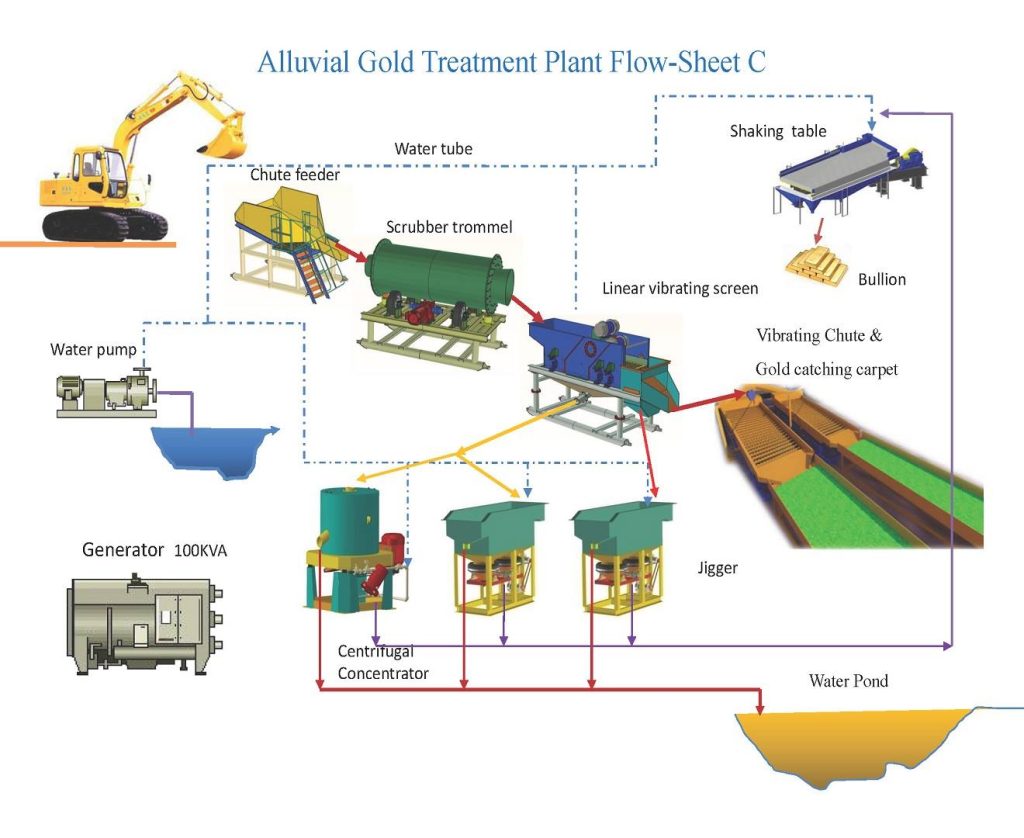
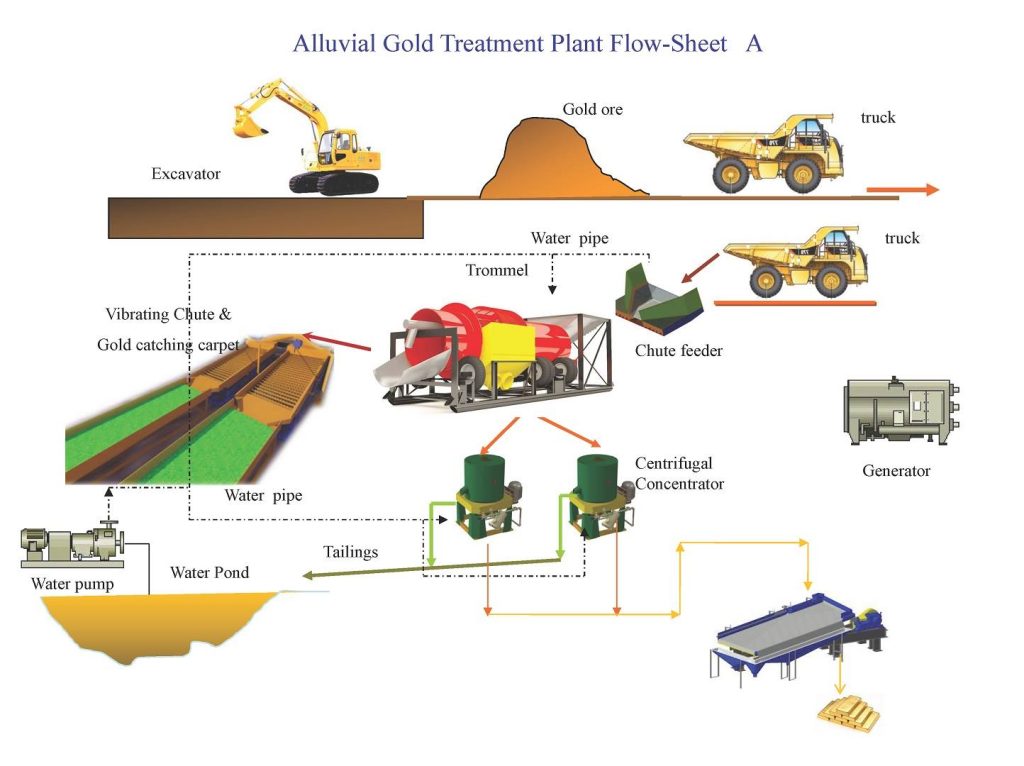
The principle of placer/alluvial gold recovery process is to maximize the recovery rate of gold and the associated heavy minerals from gangues firstly, and then separate gold from the associated heavy minerals by joint mining solutions such as gravity separation, flotation, amalgamation, magnetic separation and electrostatic separation.
Ore washing operation is an important process before the placer gold separating operation. Its main purpose is to separate the gravel, sand and granular soil, and wash the fine mud adhering to the gravel and the gold ore mixed in it.
Screening operation main purpose is to screen the placer gold ore after washing, and to screen out large pieces of gravel without gold, so as to improve the gold recovery efficiency.
Gravity separation process is due to the large specific gravity and coarse particle size of placer gold, which is generally 0.074~2mm, and the second reason is that the gravity separation process is economical and simple.
Concentrate operation, gravity separation process, magnetic separation process, flotation process, electric separation process or combined process can be used to separate gold and various heavy minerals from each other, so as to further improve the grade of gold.
Since gold is in a free state in placer gold, and the specific gravity difference between gold and sand is very obvious, placer gold gravity separation method is an ideal method to extract gold from placer ore. The task of our placer gold processing production line is to separate gold from a large amount of mixed gravel to ensure a higher metal recovery rate and better economic benefits.
Placer gold washing plant sand mix rock stone together
Placer Gold Mining Process
The goal of placer/alluvial gold mining is to maximize the recovery of gold and associated heavy minerals from gangue. To achieve this, a combined mining scheme involving gravity, flotation, magnetic, and electrostatic separation is used.
Ore washing: This crucial step precedes the separation of placer gold. Its primary objective is to separate gravel, sand, and granular soil while also removing fine mud adhering to the gravel and any mixed-in gold ore.
Screening: The main purpose here is to screen the placer gold ore after washing in order to eliminate large pieces of non-gold-bearing gravel and enhance the efficiency of gold recovery.
Gravity separation: Since placer gold exists in a free state and has a noticeable difference in specific gravity compared to sand, using gravity separation is an ideal method for extracting gold from placer ore.
Concentrate processing: In cases where gold contains various metal minerals or impurities, additional processes such as gravity separation, magnetic separation, flotation, electric separation or their combination can be utilized for mutual isolation. These processes further improve the grade of extracted gold
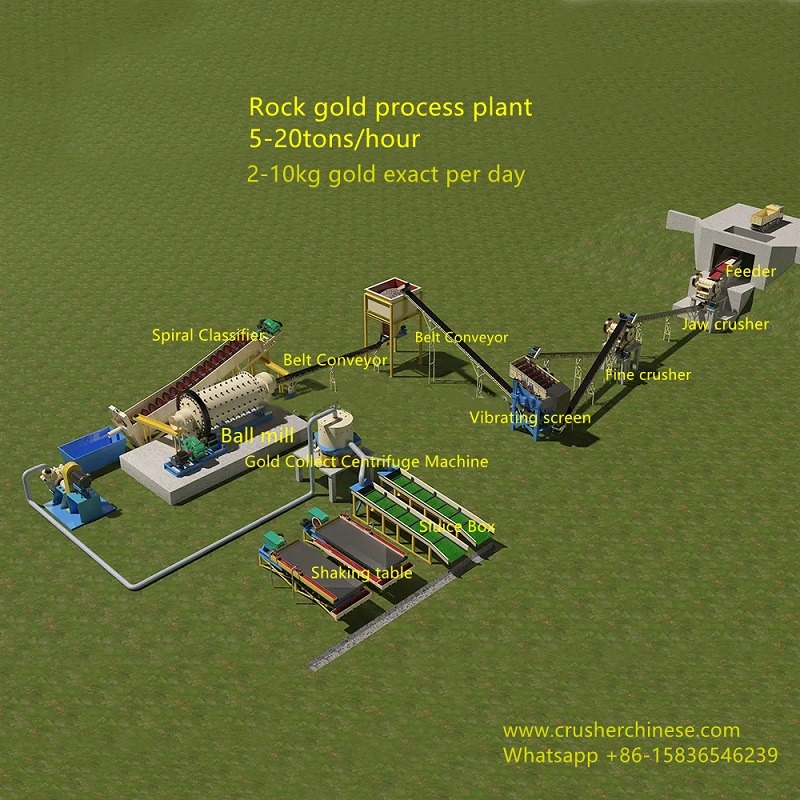
The current mainstream process for hard rock gold mining generally involves crushing, grinding, and gravity separation. Gravity separation is the traditional method widely used in rock gold mining plants and is also suitable for finely crushed rock gold minerals.
Crushing: During the crushing stage, there are mainly two processes – a two-stage one-closed-circuit process and a three-stage one-closed-circuit process. Coarse crushing is done using a jaw crusher or cone crusher, while medium and fine crushing operations use a jaw crusher or other gold crushing machine.
Grinding: To achieve the required fineness for gold ore grinding, a ball mill is usually used in conjunction with a classifier. The qualified particle size should be below 200 mesh.
Gravity separation: Currently, gravity separation is only employed to select rock gold deposits that have simple structures and coarse grain sizes, particularly oxide rock gold deposits with high density. Gravity separation relies on significant differences in density between the target metal (gold) and the surrounding materials where it is found. It also requires that the target metal cannot be bound to the surrounding rock matrix. Some devices used in gravity separation include trommels, sluices, spiral concentrators, cyclones, centrifugal concentrators, and shaker tables.
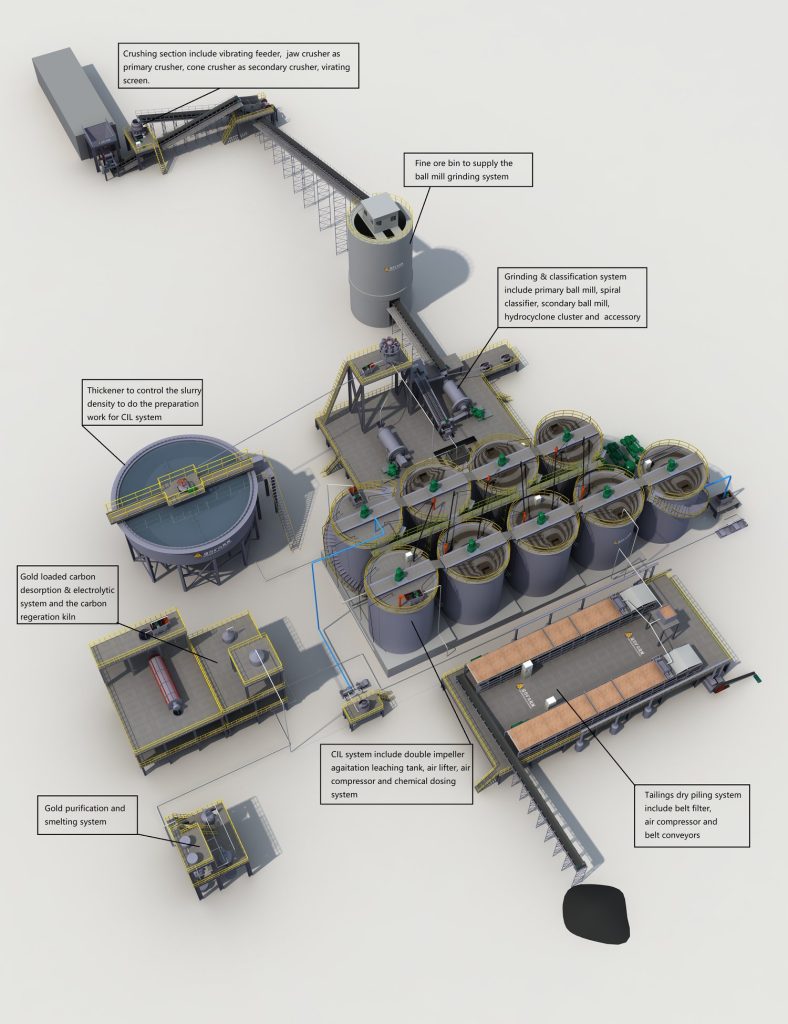
The carbon in leach (CIL) process is widely used in newly constructed gold leaching plants. Many plants are also transitioning to CIL. This process is suitable for treating oxidized gold ore with low sulfur and mud content, but not for high-grade silver ores. The ratio of gold to silver should generally not exceed 1:5. In China, the optimal conditions for the CIL process are as follows: pH level of 10-12, sodium cyanide concentration of at least 0.015%, activated carbon particle size of 1.0-3.35mm (coconut shell activated carbon), and slurry concentration of 40-45%.
CIL is primarily used for processing high-grade gold ores (above 1g/t) as well as those with a large volume of associated minerals such as silver, platinum, copper, etc. The CIL process demonstrates superior performance in extracting these minerals simultaneously. Additionally, GUOGAO Dressing Test Center can assist you with component testing of your ores.
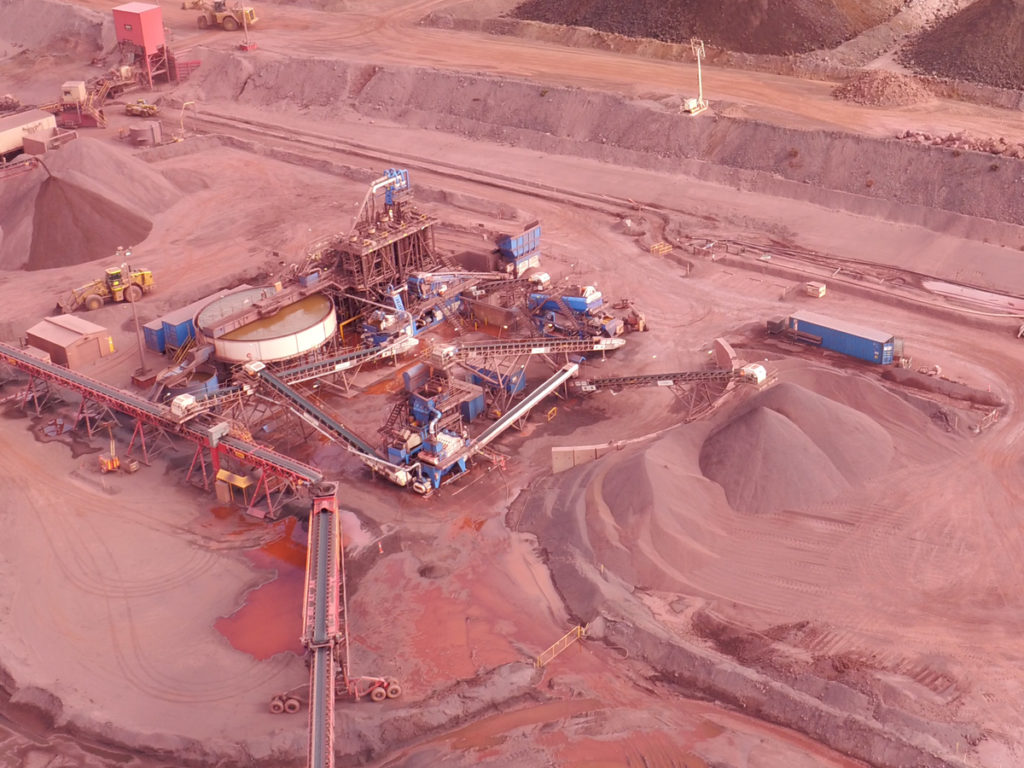
Copper industrial minerals include natural copper, chalcopyrite, chalcocite, tetrahedrite, azurite, malachite, and more. Chalcopyrite is the primary compound mined, followed by chalcocite and bornite.
To fully utilize copper ore, it must undergo flotation processing. Flotation separation is a crucial process in the current mineral beneficiation market for copper ore. By understanding the characteristics of the ore, we can tailor a suitable processing plant and equipment.
Copper ore is categorized into sulfide ore, oxide ore, and mixed ore based on its oxidation rate. The primary technological process for copper ore is flotation. For refractory mixed copper ore and refractory oxide ore, the hydrometallurgical process is generally utilized.
The beneficiation process of copper ore relies on the physical and chemical properties of different minerals present in the copper ore. After crushing and grinding the ore, various beneficiation processes such as gravity separation, flotation, magnetic separation, electric separation are employed to separate valuable minerals from gangue minerals while keeping associated useful minerals separated from each other as much as possible. This process aims to remove or reduce harmful impurities in order to obtain raw materials suitable for smelting or other industries.
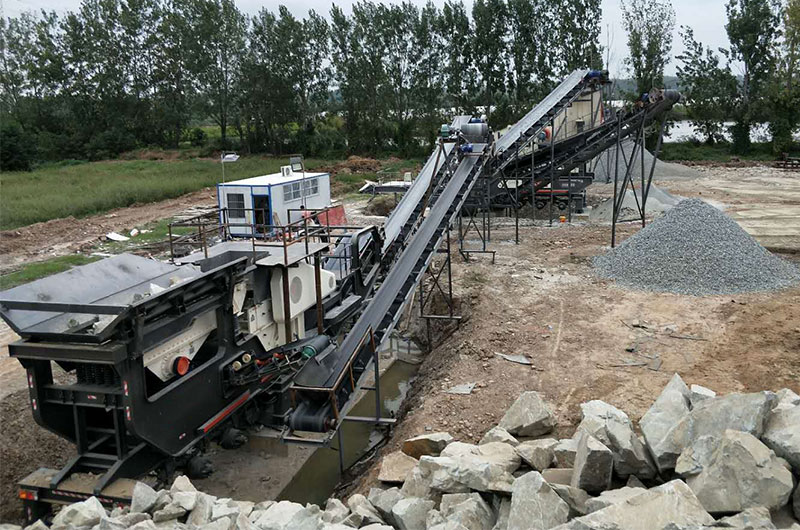
Applications: Crush limestone, granite, marble, basalt, calcite, ballast, diabase, river gravel, andesite, iron ore, gold ore, concrete, slag, coal, and other kinds of mine, rock, road, construction waste recycling materials.
Why choose Guogao Mining Machinery?
Focus on the research and innovation of mineral processing equipment, having won over a hundred national patents. Strive for excellence, aiming to integrate equipment and processes comprehensively, improve productivity, reduce energy consumption, extend equipment stability and operation time, and provide cost-effective services.
With a Grade B qualification in the metallurgical industry, we have abundant experience and expertise in ore mining, selection, and smelting. We have completed over 2000 mine designs and research projects. Not only can we provide clients with reasonable process flows, but we can also offer customized equipment configurations.
According to the needs of customers, manage, organize and coordinate various aspects of the entire project construction period, so that the project can be constructed and completed on schedule, meet standards and achieve production. It can also provide operation contracting or management services during the mining production period according to customer needs, ensuring the development of beneficiation plants.