Ultra Fine Grinding Mill is mainly applied to non-inflammable, non-explosive and brittle materials with Mohs hardness under six. Such as calcite, chalk, limestone, dolomite, kaolin, gypsum, etc, totally more than 100 kinds of materials. Product fineness can be controlled between 325~2500 mesh.
The main bearing and each dial of the Ultra Fine Grinding Mill are driven by the electromotor of the main machine through a reducer. The rollers, which roll in the ring, are driven by the dial through a plunger. After being crushed by a hammer crusher, the large materials become smaller ones and are sent to a storage hopper by an elevator. They are then further sent evenly to the middle of the first dial by an electromagnetic vibrating feeder and feeding pipe.
The materials will be driven to the edge of the dial by centrifugal force and fall down into the ring. They will be crushed and ground by roller, eventually becoming powder after three rings’ production. The high-pressure centrifugal blower will inhale air from outside and blow it towards classifier along with crushed materials.
The rotating turbo in the powder concentrator will cause coarse materials to return to mill for regrinding, while fine particles mix with air and enter cyclone for discharge into bottom discharge bin. The air mixed with very few fine particles will be purified using an impulse duster before being discharged through blower and muffler.
1. The product capacity of the Ultra Fine Grinding Mill is twice that of a jet mill and agitation mill, under the same final size and power.
2. The roller and ring are made of special material, greatly improving grinding efficiency. The lifetime of its wearing parts can reach over one year for the same material and final size, which is 2-5 times longer than that of a vertical shaft impact crusher and turbo-mill. Especially when handling calcium carbonate and calcite, the lifetime can reach 2-5 years.
3. There are no rolling bearings or bolts in the grinding cavity, eliminating problems caused by bolt shedding or wear of bearings and seal components.
4. The product fineness can reach D97≤5μm.
5. By using a pulse dust collector and muffler, pollution and noise from dust have been reduced to meet national environmental protection standards.
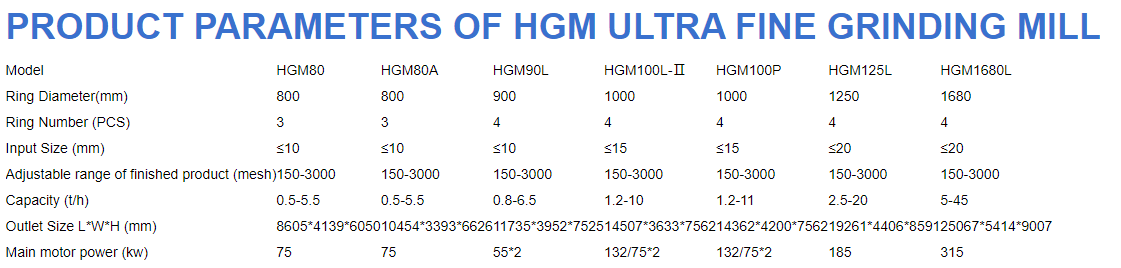