Hard granite rock must be crushed to produce different sizes of aggregates and sand.
The top six best-selling granite crusher machines include jaw crusher, cone crusher, impact crusher, sand making machine, mobile crusher, and portable crusher.
This article will discuss the pros and cons of these granite crusher machines to help you choose the right one.
Granite rock crushing equipment is popular due to the wide range of applications for granite products. Granite products are commonly used as raw materials or combined with other aggregates in construction projects such as houses, apartments, commercial spaces, public buildings, bridges, and roads.
Applications for different sizes of granite sand and gravel:
- 80-150 mm (large-sized gravel): mainly used in large-scale water conservancy and hydropower construction
- 40-80 mm (large-sized gravel): primarily used for road construction and railway tracks
- 20-40 mm (medium-sized gravel): mainly used in civil construction projects
- 5-20 mm (small-sized gravel): primarily used in large concrete buildings
- Under 5 mm (sand): utilized in various building and road construction projects
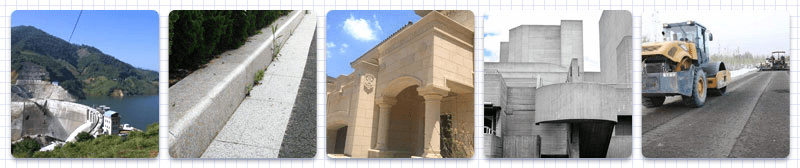
Jaw Crusher
With its large feeding inlet and strong crushing capacity, jaw crushers can efficiently crush bulky granite rocks (above 450mm) into smaller sizes. They are efficient primary granite crushers.
The fine crushing jaw crusher developed by Ftmmachinery is capable of finely crushing granite stones.
80-150 mm (oversized gravel): mainly used for large-scale water conservancy and hydropower construction.
40-80 mm (large-sized gravel): mainly used for road, road base, and railway construction.
20-40 mm (medium-sized gravel): mainly used for civil construction.
5-20 mm (small-sized gravel): mainly used for large concrete buildings.
Under 5 mm (sand): used in various building and road construction projects.
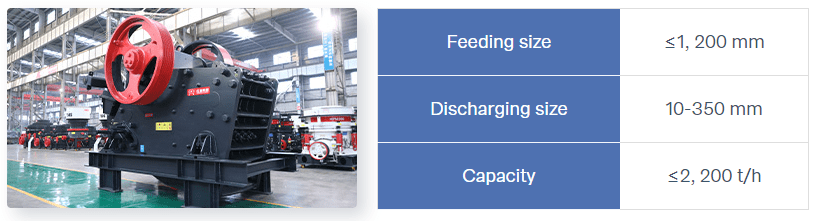
Cone Crusher
Granite rock, which is highly hard and prone to wearing down the crusher’s wear-resistant parts, should ideally be crushed using a machine that employs the lamination crushing principle. This helps minimize the loss of these parts.
The cone crusher crushes granite rock through extrusion, resulting in relatively low equipment wear and tear as well as minimal wear costs.
As a result, it has become a popular choice for granite crushing due to its advantages such as high resistance to wear, large output, and consistent cubical products. It is often used in secondary crushing processes. Additionally, if the particle size is small enough, granite can be directly fed into the cone crusher.
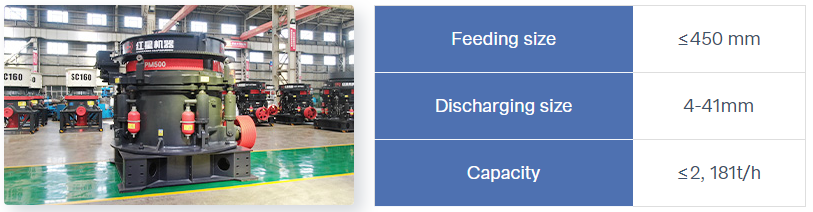
Advantages of Cone Crusher
The cone crusher has a high output and stable production, making it suitable for large-scale granite crushing plants with high productivity.
Over 90% of the granite gravel is perfectly cubical in shape, resulting in a low presence of needle-like and flake particles.
Its modular design allows for easy conversion between primary, secondary, and tertiary crushing by simply changing the cavity type.
Additionally, the cone crusher is equipped with a comprehensive dust collection and reduction system as well as an advanced noise treatment device to effectively address dust and noise pollution.
Disadvantages of Cone Crusher
One drawback is its relatively expensive price.
Impact Crusher
The impact crusher excels in both crushing and shaping. It produces superior product shape compared to the cone crusher.
Considering the significant wear caused by granite on the impact crusher, we refrain from using it for coarse crushing of granite. Instead, we utilize its shaping capability to achieve perfectly shaped granite products. Typically, it is positioned after a jaw crusher or a cone crusher.

Advantages of Impact Crusher
The impact crusher features a spacious feeding port, a deep crushing cavity, and a high crushing ratio, enabling efficient fine crushing of granite.
The gap between the impact plate and the hammer can be easily adjusted to effectively control the granularity of the final crushed granite.
The high chrome blow hammer is highly resistant to impact and wear.
Disadvantages of Impact Crusher
Impact crusher is better suited for crushing medium-hard and brittle materials like limestone and dolomite. Hard granite rock can cause significant wear on blow hammers, necessitating periodic replacement.
The impact crusher generates more noise and dust.
Sand Making Machine
The granite sand making machine serves the dual purpose of creating and shaping sand.
The sand making machine provides a superior shaping effect compared to the impact crusher. If you require granite sand with exceptional cubic shape for your sand production line, consider purchasing this machine.
The granite sand produced by this machine exhibits uniform particle size, high compressive strength, strong adhesion, and long-lasting durability. It finds extensive applications in highways, railways, bridges, airports, real estate development, and other fields.
This machine is employed in the final stage of the granite sand production line.
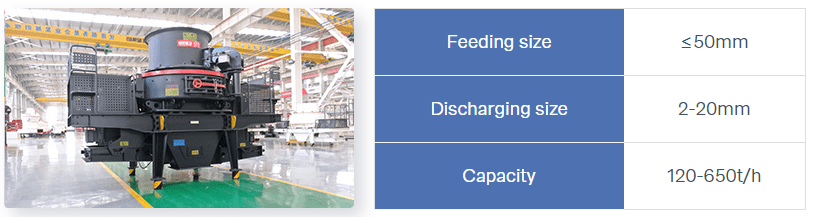
Advantages of Sand Making Machine
The advanced stone-on-stone or stone-on-iron crushing principle produces granite sand with uniform particles and a shape similar to natural sand. It can also reshape unsatisfactory sand into cubical shape to meet the high requirements of machine-made sand and gravel in certain fields.
The design of the large discharge port ensures smooth material flow, prevents blockage, avoids equipment damage, and improves crushing efficiency.
The wearing parts of the granite sand making machine are made of high-end wear-resistant materials, enhancing its resistance to wear, compression, corrosion, etc. Its lighter weight facilitates transportation and installation.
The adoption of a water seal ensures effective sealing performance for the system, preventing dust overflow and reducing environmental pollution.
It is equipped with a safety protection device that automatically cuts off power and activates the protection system when any problem occurs in the equipment. This guarantees equipment safety as well as personal safety.
Disadvantages of Sand Making Machine
Its output is smaller compared to other granite rock crushers.
Mobile Crusher
Mobile crushers are stone crushing machines that are mounted on tracks and can be easily moved between production sites. They offer complete mobility, allowing them to quickly relocate to a new processing site and begin production. As a result, they are highly suitable for large-scale open-pit granite quarries.
Depending on the type of crusher installed, mobile crushers can include options such as jaw crushers, cone crushers, impact crushers, or sand making machines.
By combining hoppers, feeders, and screeners with these crushers, you can create a mobile crushing plant that integrates feeding, crushing, screening, and conveying functions.
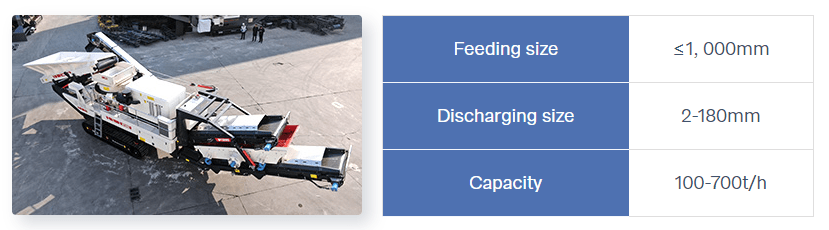
Advantages of Mobile Crusher
Mobile crushers can be stationed directly at the quarry or aggregate site, reducing additional logistics costs for conveyor belts or a larger number of dump trucks needed to transport granite products.
They require less lead time compared to stationary crushers.
They do not require civil works or result in wastage in plant structural and electrical components.
Disadvantages of Mobile Crusher
Although compact in structure, mobile crushers have many components, making maintenance challenging.
The space between the crusher discharge and the conveyor belt is limited, and the feed opening is slightly smaller, which reduces the throughput of the mobile equipment.
Portable Crusher
Portable crushers are mobile and can be transported from one production site to another using a tractor. The process of transferring them requires more time and labor compared to self-propelled mobile crushers. They are commonly used in granite mines and quarries where raw materials are concentrated, eliminating the need for frequent site transfers.
Additionally, portable crushers can be combined with hoppers, conveyor belts, and screening machines to create a stone crushing plant that integrates feeding, crushing, screening, and conveying functions.
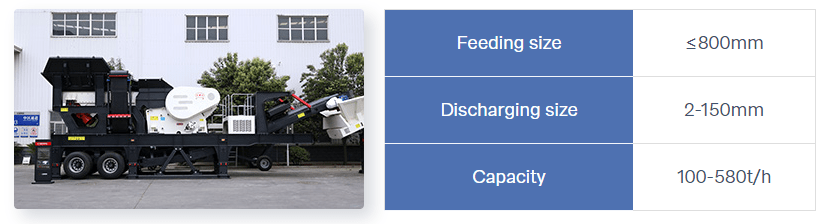
Advantages of Portable Crusher
Portable crushers can move flexibly without the need for concrete infrastructure, allowing for mobile operations to be completed within 48 hours and ensuring continuous production in the quarry.
Compared to mobile crushers of similar size, portable crushers offer lower prices, higher output, and greater economic benefits.
Portable crushers have an open design that makes maintenance easier and reduces downtime.
Disadvantages of Portable Crusher
Transporting portable crushers requires more time and labor as they are transported by a trailer and secured using a hydraulic support system at the production site.
Tips: How to Choose the Right Granite Rock Crusher?
The above provides a brief introduction to the 6 popular granite crushers available on the market. To achieve efficient granite rock crushing, consider the following factors:
- Wear-resistance
Granite rock is highly hard and contains a high silicon content, making it difficult to crush and requiring relatively high crushing costs. Choosing the wrong granite crusher will accelerate wear part damage, potentially necessitating replacement within days and increasing operating costs. - Grain shape
As granite is brittle, an improper crusher choice can increase needle-like and flake-like material content while also increasing internal cracks in the finished product. This reduces its application scope and revenue potential. - Production
During granite crushing, two or more types of crushers are typically used, making the combination of crushers crucial for success. A well-designed granite rock crushing line ensures smooth production with less manpower required and higher output achieved. - Dust
Granite crushing inevitably generates dust that can pollute the environment or even cause downtime if not managed carefully. Therefore, choose a granite crusher equipped with a sealing system and dust control measures. - Noise
Reducing noise is an important aspect of environmental protection considerations when selecting a granite crusher model. Opt for one that comes with noise-reducing accessories.
Granite rock crushing process
As a professional mining equipment manufacturer, Ftmmachinery can provide you with efficient and sturdy rock crushers and assist in designing a reasonable granite stone crushing plant based on your requirements (output, grain shape, particle size, working site).
Using the granite sand making line as an example, the crushing process is as follows:
- Coarse (primary) crushing: Vibrating feeder evenly feeds bulky granite rocks into the jaw crusher.
- Secondary crushing: Belt conveyor sends coarsely crushed granite stones to the cone crusher.
- Screening: Belt conveyor transports finely crushed granite stones to the vibrating screen.
- Sand making: Fragments that meet sand making requirements are sent to the sand making machine; those that don’t meet requirements are sent back to the cone crusher for re-crushing.
- Screening of finished products: Various specifications of finished granite products and granite powder are screened out.
- Sand washing: If there are many impurities in the sand, use a sand washing machine to improve the quality of the granite sand.
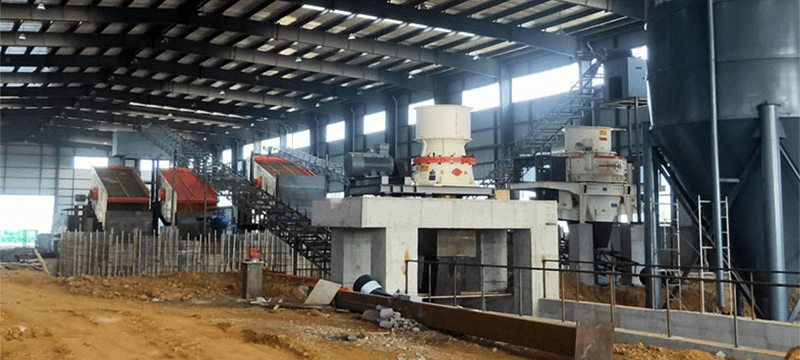
Granite rock crushing line with an output of 200 tons per hour (case)
Feeding size | Finished product specification | Device configuration |
≤630mm | 0-5mm 5-10mm 10-20mm 20-40mm | Silo |
ZSW490*110 Vibrating Feeder | ||
HD98 Jaw Crusher | ||
HPM300 multi-cylinder hydraulic cone crusher | ||
3YK1854 Vibrating screen | ||
Several conveyors |
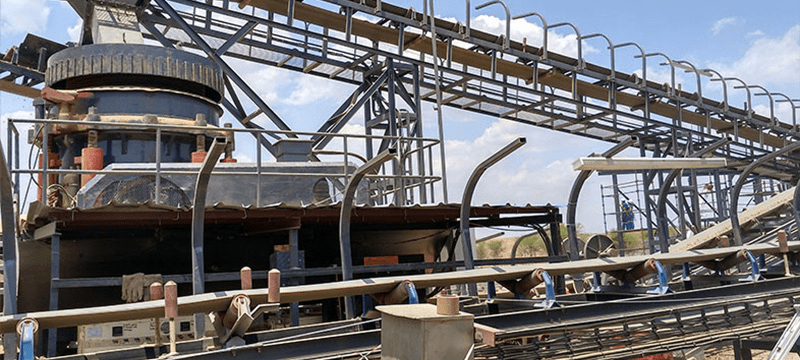
Granite rock crushing line with an output of 500 tons per hour (case)
Feeding size | Finished product specification | Device configuration |
≤450mm | 0-5mm 10-20mm 20-33mm 33-65mm | Silo |
GZD1000*36000 Vibrating Feeder | ||
CJ96 Jaw Crusher | ||
SC560 Single Cylinder Hydraulic Cone Crusher | ||
VSI6X sand making machine | ||
3YK2160 Vibrating screen | ||
Several conveyors |