This blog provides a comprehensive study on the flotation process of chalcopyrite to help you achieve optimal grade and recovery.
Mineral and flotation characteristics of chalcopyrite:
- Mineral characteristics:
There are over 280 types of copper-bearing minerals found in nature, with chalcopyrite, chalcocite, and bornite being the main ones. Chalcopyrite accounts for approximately 70% of these minerals.
Chalcopyrite is a copper iron sulfide mineral and is the most abundant copper ore mineral found in various hydrothermal environments. It is often associated with sphalerite and galena. When oxidized, it forms copper minerals such as malachite, azurite, cuprite, and tenorite.
Chalcopyrite Properties:
Chemical formula: CuFeS2
Crystal structure: Tetragonal
Appearance: Often dense massive or granular with a brassy to golden yellow color.
Hardness: Ranks 3.5 to 4 on the Mohs scale; softer than pyrite but can be scratched by a knife.
Streak color: Diagnostic as green-tinged black
Other properties: Exhibits good electronic conductivity enhancing its floatability; weak paramagnetic properties; similar appearance to pyrite and gold ore.
Chalcopyrite occurs in most sulfide deposits worldwide including Río Tinto in Spain, Ani in Japan, Butte in Montana, and Joplin in Mozambique. Chile is the world’s leading producer of copper followed by the U.S. and Peru.
Due to its association with low-grade molybdenum, gold, silver, and other rare precious metals,
flotation recovery becomes challenging for low-grade chalcopyrite ores.
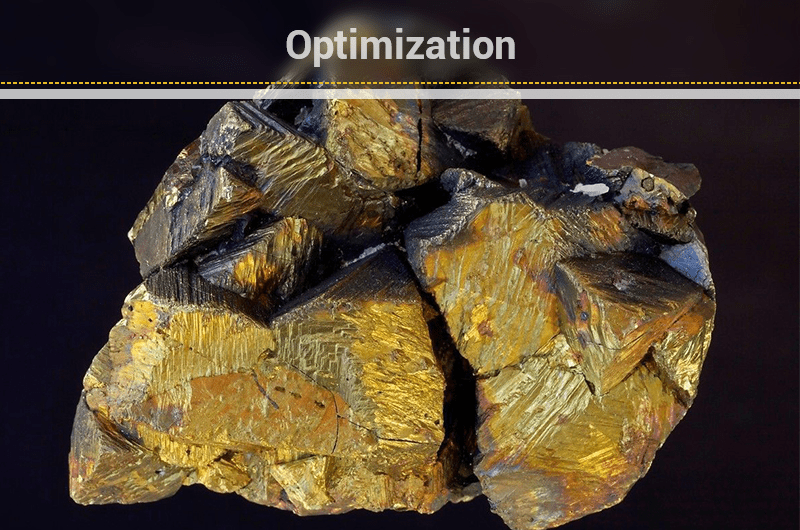
- Flotation characteristics of chalcopyrite
Chalcopyrite is a mineral that exhibits good self-induced flotation and collector-induced floatability in nature. It is hydrophobic in weak alkaline and neutral environments, but forms hydrogen bonds with water in highly alkaline environments, reducing its ability to float.
Ftmmachinery discovered that chalcopyrite naturally floats in oxidizing environments. The presence of steel grinding balls in a ball mill creates a strong reducing environment that affects its flotation performance. Adding oxidants or exposing it to air can restore its flotation performance.
Flotation process of chalcopyrite
The current industrial application of the flotation process for chalcopyrite includes mixed flotation, full priority flotation, partial priority-mixed flotation, and equal flotation.
When using flotation reagents, special attention should be given to the collectors. These include xanthates and their derivatives, black agents and their derivatives, sulfur and nitrogen collectors, sulfhydryl compounds, etc. Experiments have shown that combining 90% ethylxanthate with 10% 2-ethyl-dithiophosphate achieves the highest copper recovery rate and copper concentrate grade.
- Mixed flotation process
The mixed flotation process involves first floating chalcopyrite and other useful minerals, followed by preferential copper floating while suppressing other minerals to obtain qualified copper concentrate.
This process is suitable for ores with low raw ore grades and simple properties. It has advantages such as saving on grinding costs, flotation chemicals, and equipment. However, it faces challenges in separating useful minerals resulting in low concentrate grade.
A copper and molybdenum sulfide ore plant in the United States used a ball-milled mixed-flotation process which yielded a 19.23% copper grade with an 85.5% recovery rate along with a 48.53% molybdenum grade at a 90.96% recovery rate.
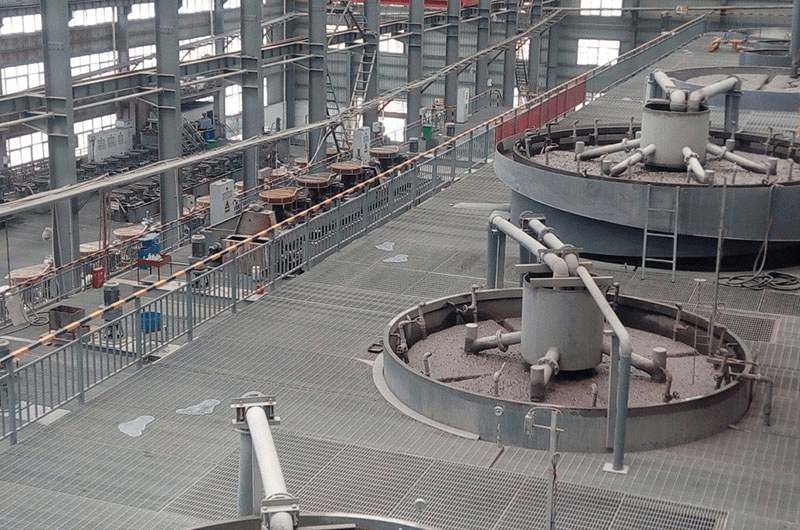
- Full priority flotation process
There are two types of full priority flotation processes:
One involves inhibiting associated minerals, such as pyrite, by adding lime-based inhibitors. Although this process achieves good flotation results, it requires a large amount of lime and reduces the grade of copper concentrate, as well as the recovery of copper and associated rare precious metals like Au, Ag, and Mo.
Another approach is to float chalcopyrite under neutral to weakly alkaline conditions using highly selective agents for chalcopyrite.
This method is suitable for processing ores with simple composition, few recoverable useful minerals, significant differences in flotation between useful minerals or minerals symbiotic with chalcopyrite that can be effectively suppressed without significantly affecting the flotation of chalcopyrite.
The copper-molybdenum plant in Nigeria primarily employs this process to prioritize obtaining a mixed concentrate of copper-molybdenum while suppressing pyrite. The obtained copper concentrate has a grade and recovery rate of 24.32% and 96.77%, respectively. The molybdenum recovery rate is 81.04%, while gold and silver have recovery rates of 82.00% and 84.03%. The flotation index is ideal; the process is simple with advantages including straightforward flow and no need for regrinding crude concentrate.
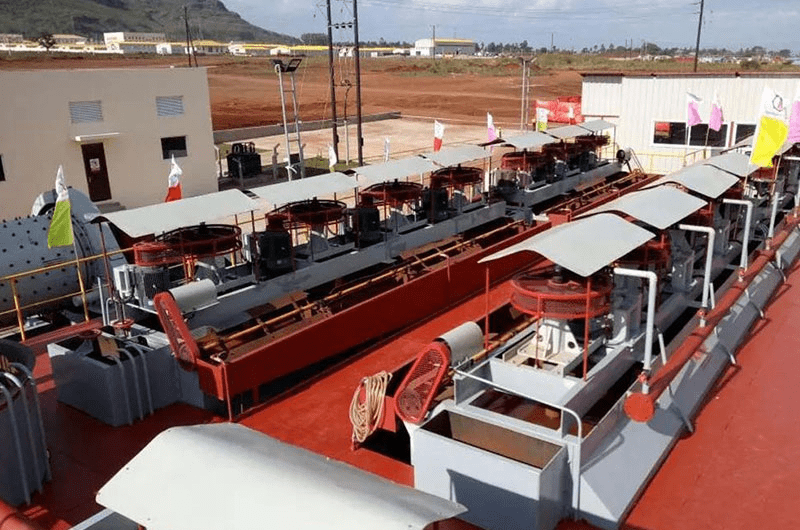
- Partial priority – mixed flotation process
The partial priority – mixed flotation process involves the rapid flotation of easily floatable copper ores, followed by the mixed flotation of a concentrate containing both copper and other valuable minerals. The mixed concentrate is then subjected to flotation separation, and finally, the copper concentrate is either combined or treated separately.
This process reduces the amount of flotation reagents required and improves the efficiency of flotation. However, it requires more flotation separators.
This particular flotation process is employed at a copper-molybdenum plant in Chile. Initially, MC-103 was used to float copper-molybdenum ore, and subsequently, a chemical agent with strong recovery ability was utilized to float difficult-to-float copper-molybdenum ore. The overall result increased the molybdenum grade to 48.83% with a recovery rate of 90.60%, effectively addressing issues related to low molybdenum recovery and high costs.
- Equal flotation process
The equal flotation process can be applied to polymetallic ores where one mineral exhibits good floatability while others can be categorized as easy or difficult for floating.
This type of flotation process yields favorable specifications without requiring regulators, inhibitors, or activators additives that alter natural mineral floatability. Consequently, it minimizes chemical usage and simplifies the equipment needed for effective froth-flotation operations.