Traditional phosphate ore beneficiation processes include scrubbing and desliming, gravity separation, flotation, and heavy magnetic-flotation combined processes; new phosphate ore beneficiation processes include microbial treatment method, dry electrostatic separation method, magnetic hood method, and selective flocculation method. Only by selecting the appropriate phosphate ore beneficiation process can high grade and high recovery rate of phosphate concentrate be obtained at low cost.
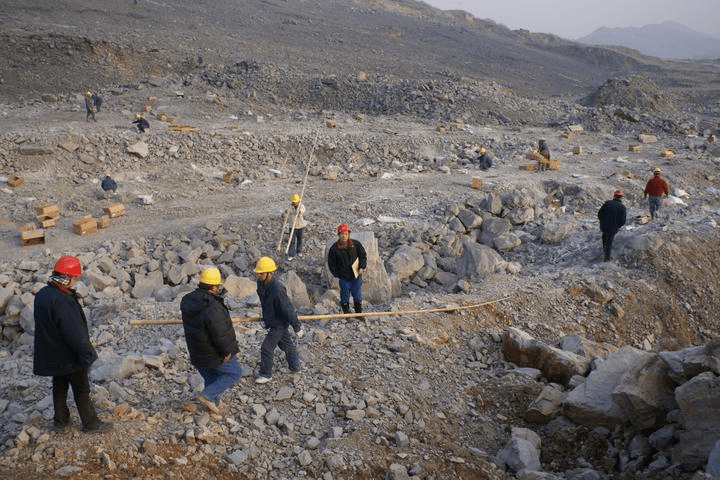
The selection of phosphate ore beneficiation process mainly depends on the nature of the ore. Scrubbing and desliming process is suitable for treating highly weathered phosphorite, but the grade and recovery rate of phosphate concentrate are low; heavy medium separation process in reselection has less environmental pollution and good performance in treating coarse-grained phosphorite, but it is not suitable for treating disseminated fine-grained phosphorite. Flotation is the main method for phosphate ore beneficiation, which is suitable for treating complex refractory phosphorite with good flotation indicators. The heavy magnetic-flotation combined process is applicable to cases where useful semi-weathered minerals are present in phosphate ores with high utilization rate of ores but complex beneficiation process often requires complicated drug removal treatment. Microbial treatment method is suitable for treating complex properties and low-grade phosphorite with good leaching effect on ores but slow processing speed usually takes several months. Although dry electrostatic separation method, magnetic hood method,and selective flocculationmethod have good laboratory indicators as new methods forphosphateorebeneficiationprocesses,theyarehardlyappliedinindustryandthereforearegenerallynotadoptedorneedtobeusedwithcautioninindustrialproduction.
Phosphate ore beneficiation processes can be applied to phosphates with complex structure construction,varied mineral occurrence relationships,fine grain size,intimate intergrowth,widespread mixing symbiosis,and difficult monomer dissociation.
Phosphateorebeneficiationprocessescanbedividedintophosphaterockcrushing,phosphaterocksorting,andphosphateconcentratedewatering.
I. The ore crushing process in the phosphate ore beneficiation process.
The purpose of ore crushing is to separate fine-grained phosphorite from other gangue particles, achieve monomer dissociation of phosphate minerals, and facilitate subsequent sorting processes. The ore crushing process includes crushing, screening, grinding, and classification processes. The conventional phosphate rock crushing process consists of three stages in a closed circuit, namely coarse crushing, medium crushing,and one-stage screening operation. Crushing machines (crushers) and ball mills are used to reduce the particle size of the ore so that the phosphate minerals can be dissociated from impurity minerals individually. Phosphate minerals and impurity minerals in phosphorite often bond together to varying degrees; only when they are ground to a certain particle size can they be dissociated.The degree of grinding depends on the particle size of phosphate minerals and impurity minerals.This operation is often a fundamental step in phosphorite enrichment.
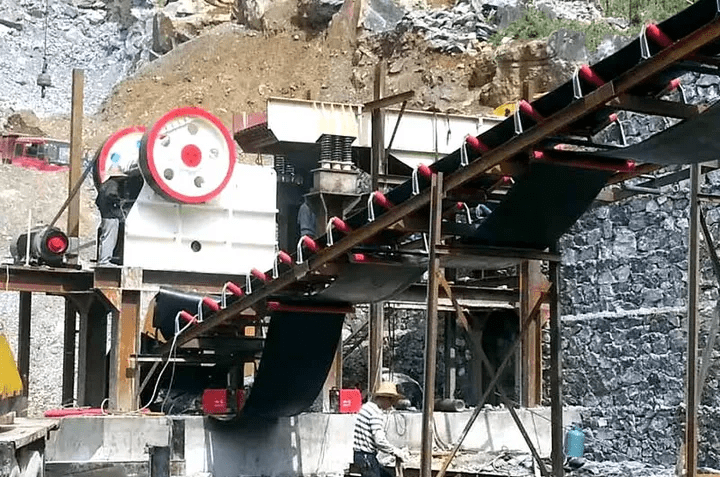
II. Ore sorting process in the phosphate ore beneficiation process.
The purpose of the ore sorting process is to achieve enrichment of already monomer dissociated phosphate ore. The selection process of phosphate ore usually adopts flotation process, and the common flotation processes for phosphate ore are: single reverse flotation, positive flotation, reverse positive flotation (positive and negative flotation), and double reverse flotation. Usually, phosphorus ores contain recoverable associated metals such as iron ores, so magnetic separation and other processes can be added in the flotation to recover useful associated metals. Commonly used principles of floatation include: priority floatation process, mixed floatation process, partial mixed floatation process, and equal floating flowchart. For low-grade phosphorus ores, a mixed floatation principle is often adopted: first float out the phosphorus ore and recovered useful minerals, then separate the phosphorus ore from useful minerals. This method can save on floatation reagents, reduce the number of floatation equipment units, and decrease overall costs.
1. Flotation in the phosphate ore beneficiation process: By utilizing different surface properties between phosphate minerals and impurity minerals using a collector to make phosphate minerals rise up while achieving separation; this operation is called positive flotation. Another method is to make impurity minerals rise up while allowing phosphorous minerals to sink down; this is called reverse flotation. In order to enhance separation efficiency, it’s often necessary to add depressants that inhibit certain mineral’s upward movement during floating operations.
The slurry containing phosphorous mineral obtained from a flotator can be further processed through thickening,filtrating,and dewatering steps to obtain concentrate.
2.Magnetic Separation in Phosphate Ore Beneficiation Process:Use magnetic separator machine(magnetic separator)to remove magnetic impurities from phosphate ores.
3.Optical-electric Separation in Phosphate Ore Beneficiation Process:Utilize differences in color between phosphate minerals and impurity minerals, use photoelectric devices for identification, and control compressed air jets to separate phosphate minerals from impurity minerals.
4.Calcination in Phosphate Ore Beneficiation Process: Used to remove organic matter, carbon dioxide, and a portion of fluorine from phosphorous ores. The calcination temperature varies depending on the specific purpose but is generally between 400-1 phosphorus ore.
5.Dense Medium Separation in Phosphate Ore Beneficiation Process:Due to differences in density between phosphate minerals and impurity minerals, select a medium with a density that falls between the two. This causes one type of mineral to float while the other sinks, achieving separation objectives. The enrichment process for phosphate ores depends on specific circumstances. For example, the beneficiation process for Florida phosphate ores includes wet screening classification, desliming, and flotation as main procedures. The beneficiation process for Moroccan rich-phosphorus ores includes crushing classification,water washing,wet screening,desliming,and dewatering steps among others.
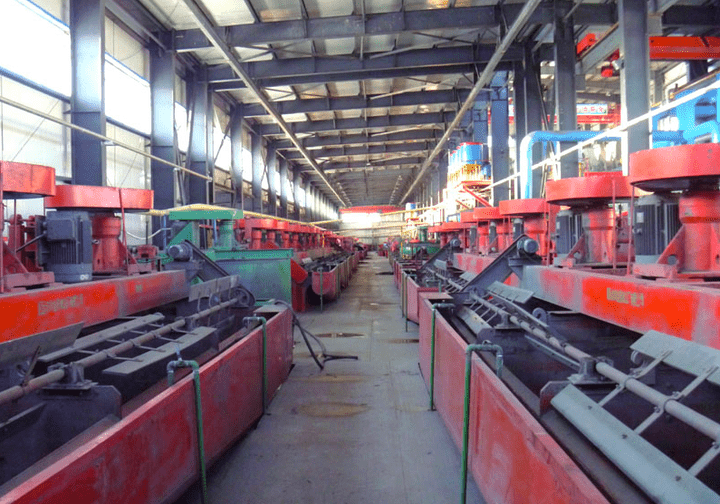
III. The dewatering process in the beneficiation process of phosphate ore.
The purpose of ore dewatering is to facilitate the storage and transportation of products such as phosphate ore. Ore dewatering usually includes two processes: concentration and filtration. Concentration of phosphate ore is generally carried out using concentrators (concentrators), while filtration is generally carried out using disc filters.
Phosphate is an important raw material for the production of phosphorus fertilizer, yellow phosphorus, phosphoric acid, phosphides, and other phosphate salts. It is a non-renewable and irreplaceable resource. China has a large reserve of phosphate resources, but more than 70% are low-grade ores that cannot be industrialized solely through scrubbing processes. Further enrichment is needed for utilization purposes. Currently, the beneficiation process for medium- to low-grade phosphate ore mainly utilizes flotation technology for enrichment, and the flotation effect depends on the interaction between mineral particles and bubbles in the aqueous medium, with flotation reagents playing a particularly important role.
Commonly used flotation processes in the beneficiation process of phosphate ore include: positive flotation process flow, reverse flotation process flow, positive-reverse flotation process flow, reverse-positive flotation process flow, and double-reverse flotation process flow.
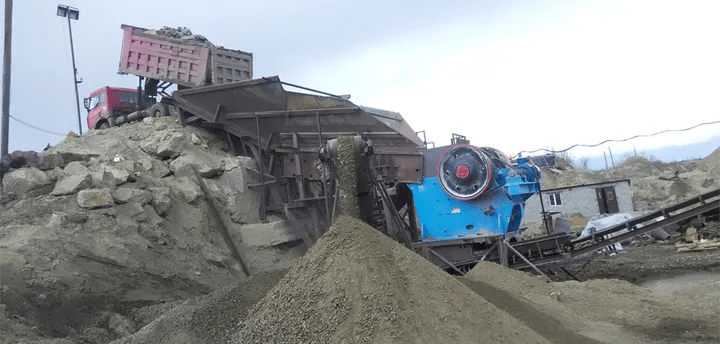
1. Beneficiation Process Flow – Positive Flotation Process Flow: In this process, the phosphate ore is ground until monomer dissociation occurs; then water is added to adjust the slurry to a certain concentration; specific collectors are used to enrich useful phosphate minerals in foam products; at the same time , specific agents are used to suppress gangue minerals such as silicates and carbonates in phosphate ores. Commonly used flotation reagents include “S”, “L”, “sulfonated phenol tar”, “F” series inhibitors etc.. This beneficiation process for phosphate ores applies to siliceous or calcareous-siliceous phosphorite, endogenic phosphorite, and sedimentary phosphate ores. The process is simple, with good impurity removal effect and effective reduction of impurities such as Me and Fe. However, it has high energy consumption and high beneficiation costs.
- Phosphate ore beneficiation process – phosphate reverse flotation process: This process generally uses inorganic acid to adjust the pH of the slurry to a certain range (pH=4.0~5.0). In a weak acidic medium, specific collectors are used to enrich calcite in the foam product, while phosphate minerals remain in the tank. The commonly used flotation agents are mainly inorganic acid adjusters and modified fatty acid collectors, which modify fatty acids through sulfonation or add additives during saponification to improve their water solubility, temperature resistance, collection ability, and selectivity. This phosphate ore beneficiation process is generally suitable for separating phosphate minerals and dolomite-type vein minerals, with an exclusion rate of dolomite-type vein minerals reaching 70%~80%. The process does not require heating and can be carried out at low temperatures without increasing energy consumption or costs. However, its applicability is limited and mainly targets calcium-bearing phosphate ores; it has poor separation effects on siliceous phosphate ores.
- Phosphate ore beneficiation process – positive-reverse flotation process: This process first adjusts the slurry to weak alkalinity using inorganic alkali and then uses specific collectors to enrich useful phosphorus minerals in the foam product while excluding silicate vein minerals that belong to silicates from the tank. The foam becomes positive floatation concentrate; then inorganic acid is added to adjust the slurry back to weak acidity after grinding or without grinding; after adjusting pulp density with collector enrichment carbonate impurities as carbonates by leaving useful phosphorus mineral inside tank obtaining reverse floatation concentrate whose main purpose is removing MgO impurities from phosphorous concentrates.
The common flotation agents include inorganic alkalis and inorganic acid adjusters such as XM-10 (a type of sodium hexametaphosphate), water glass (sodium silicate), sulfur-phosphoric mixed acids inhibitor.
This phosphate ore beneficiation process is suitable for processing siliceous calcium-bearing phosphate ores. It can obtain higher phosphorus concentrate grade compared to single positive or reverse flotation, and the combination of positive and reverse flotation can effectively improve the processing performance of phosphorus concentrates. However, the cost of reagents is high, which poses great difficulties in water resource recycling for beneficiation plants. - Phosphate ore beneficiation process – reverse-positive flotation process: This process first floats out carbonate vein minerals under acidic conditions using collectors to obtain a reverse floatation concentrate; then it undergoes secondary grinding to dissolve silicate vein minerals under alkaline conditions and float out phosphate minerals to obtain a positive floatation concentrate. This process is suitable for low-grade silicon-calcium gelatinous phosphate ores. The process does not require heating, has low energy consumption but requires separate treatment of circulating water, which greatly affects production.
- Phosphate ore beneficiation process – double-reverse flotation process: This process generally adjusts the slurry to weak acidity using inorganic acid and enriches some calcite-type vein minerals with fatty acid collectors; then it enriches quartz-type minerals with fatty amine collectors, and the remaining phosphate minerals in the tank become final concentrates.
The commonly used flotation agents are inorganic acid adjusters, fatty acids, and fatty amine collectors.
This phosphate ore beneficiation process is mainly suitable for processing mixed-type phosphate ores with low silica vein mineral content and low carbonate content. It particularly achieves good separation effects on dolomite-type vein minerals and quartz-like vein minerals. It can be carried out at low or room temperature with a simple flowchart design that has low energy consumption requirements as well as simple reagent systems with fewer types of reagents used.
However, this method uses amine collectors as cationic collectors which produce sticky foam resulting in poor selectivity; they are also sensitive to slime particles present in the ore feedstock requiring additional desliming operations, which further complicates the process.
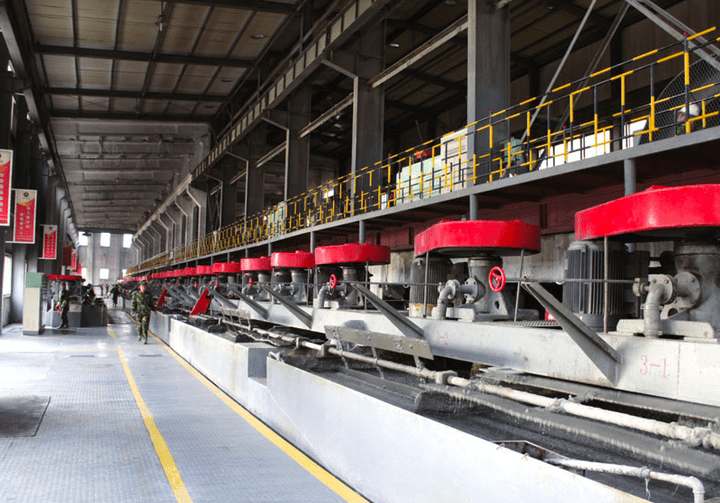
The above is an introduction to the commonly used flotation process and flotation reagents for phosphate ore. In the process of phosphate ore beneficiation, the selection of the beneficiation process flow needs to be determined based on the requirements of phosphorus concentrate product indicators and differences in raw ore properties. Therefore, it is recommended to conduct beneficiation tests first, and then scientifically and reasonably customize the process flow and flotation reagent system based on the results of the beneficiation tests to ensure ideal beneficiation indicators and economic benefits.
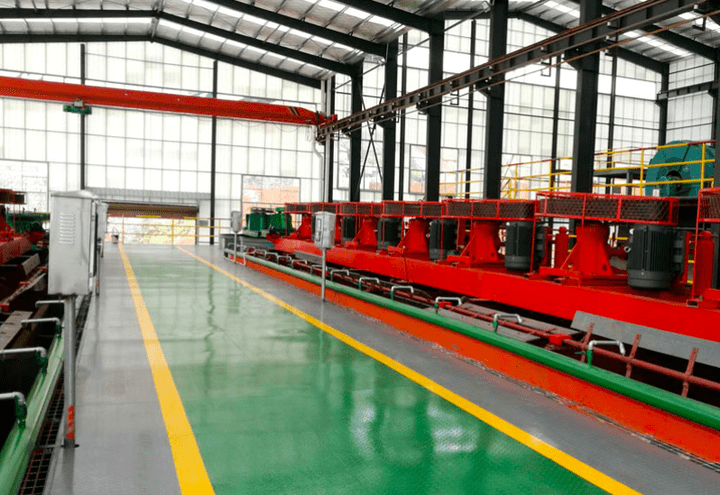
The selection of phosphate ore beneficiation process flow needs to consider the cost of mineral processing. The more complex the beneficiation process, the higher its cost. Generally, flotation costs are higher than other mineral processing costs. When it is necessary to choose a principle flotation process flow, a mixed flotation method should be prioritized to reduce the use of reagents and number of flotation equipment. When considering mineral processing costs, fixed costs, variable costs, and profits should be comprehensively considered in order to rationalize interests in mineral processing plants.
Facing competition and impact from phosphate ore market, reducing phosphate ore beneficiation – mining cost is almost their only way out. How to reduce phosphate ore mining cost has always been a problem that everyone has been exploring. “More crushing less grinding” is an effective way to reduce mining plant costs. Crushing-grinding generally accounts for more than 60% of mining plant expenses; energy consumption accounts for 60%~70%of total energy consumption in entire mining plant; grinding energy consumption accounts for 80%~90%of crushing-grinding energy consumption; therefore,reducing grinding energy consumption is keyto reducing overall energy consumption inthe entirephosphateoreminingplant.
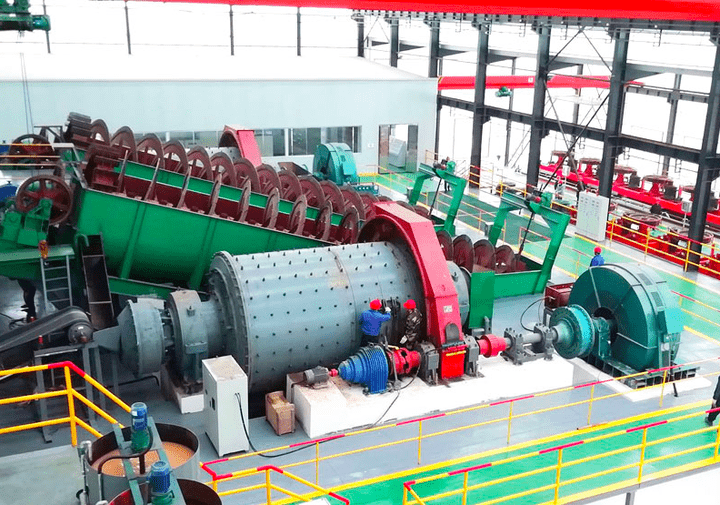
Practice has proved that adopting “more crushing less grinding” measures can effectively reduceenergyconsumptioninthe crushingandgrindingprocess,andtherebyreducethecostsofphosphateorebeneficiation.”Morecrushinglessgrinding”measuresinclude:1. Changingfromopen-circuitcrushingto closed-circuit crushing; 2. Changing from two-stage crushing to three-stage crushing, reducing the feed particle size to grinding; 3. Improving the screening efficiency of screening equipment; 4. Using efficient crushing equipment (such as high-pressure roller mill) at the final stage of crushing.
Adopting a reasonable phosphate ore beneficiation process flow is another effective way to reduce phosphate ore beneficiation costs. Commonly used processes in phosphate ore beneficiation include reselection, flotation, and heavy magnetic-flotation combined process. Reselection has low cost and less environmental pollution, but lower grade and recovery rate of final concentrate; flotation has high cost but higher grade and recovery rate of final concentrate; heavy magnetic-flotation combined process can often recover associated useful metals other than phosphorus ores, but it has complex process and higher beneficiation costs.Therefore, when fully weighing the benefits and costs of each process, choose a reasonable phosphate ore beneficiation process flow.
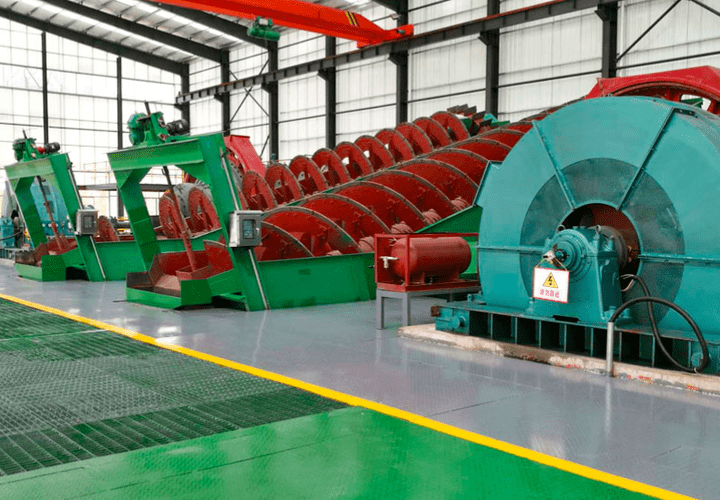
In addition,the selectionofhigh-qualityequipmentwithgoodmineralprocessingindicatorsisalsoanimportantwaytoreducethecostsofphosphateorebeneficiation.Good mineral processing equipment can improve annual operation rate,recoveryrate,andreduceenergyconsumptionandmaintenance rateofthebeneficiationplant,resultinginlowercosts.Onthecontrary,poorqualityproductionequipmenthasoppositeeffects.Therefore,thechoiceofgoodequipmentplaysanimportantroleinreducingthecostsofphosphateorebeneficiation.
Henan Guogao Mining Machinery Co., Ltd.provides turnkey services from mining tests to final production.Itcan design a reasonable crushing-grindingprocessforcustomers,anddesignasuitablephosphateorebeneficiationprocessforcustomers,andselectgoodmineralprocessing equipment for customers.Thus,itcan effectively reduce customers’phosphateorebeneficiationcostsandrationalizetheirinterests.Reducingphosphateorebeneficiationcosts.