The processing methods of lithium ore include manual selection, flotation method, chemical or chemical flotation combined method, thermal cracking method, radioactive selection method, and particle flotation method. The first three methods are commonly used. The lithium ore dressing plant mainly uses flotation and strong magnetic separation methods. Commonly used equipment for lithium ore dressing includes crushers, ball mills, classifiers, jigging machines, flotation machines, magnetic separators, etc.
Lithium ore beneficiation methods
There are five main types of lithium deposits worldwide, namely pegmatite deposits, brine deposits, seawater deposits, hot spring deposits, and sedimentary deposits. Currently, the main exploited lithium resources are pegmatite deposits and brine deposits, with brine deposits accounting for 90% of the identified resources. The primary mineral raw materials for lithium extraction are spodumene, lepidolite, lithiophilite, petalite and iron-rich mica. Among them, the first three minerals are the most important. There are several methods for lithium ore beneficiation including hand-picking method, flotation method , chemical treatment method , heavy suspension flotation method , heavy liquid separation method , thermal cracking selection method etc., among which the first three methods are more commonly used.
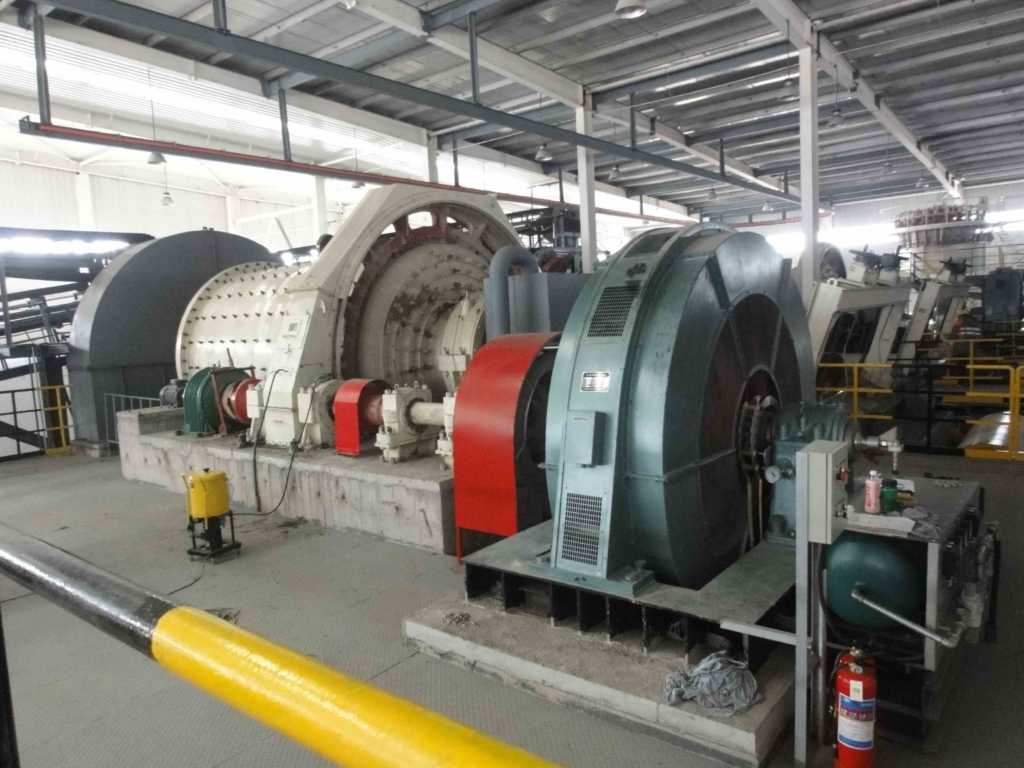
1 Hand-picking Method
This method is mainly used to separate coarse-grained crystallized spodumene and lepidolite compounds based on the difference in color or shape between minerals and gangue minerals. It involves manually selecting lithium minerals from ores using selective grinding and hand-picking methods. Before 1940-1941 it was a major beneficiation method for lithium ores.
2 Flotation Method
The flotation method can be used to separate all major lithium-bearing minerals; therefore it is an important beneficiation method for lithium ores especially for fine-grained disseminated spodumene ores . Spodumene is often floated using organic collectors that float easily in neutral or alkaline media where sodium carbonate and sodium hydroxide serve as adjusting agents; alternatively sodium fluoride and lignosulfonate can also be used as adjusting agents . Due to its special mineralogical properties,the particle size during flotation is crucial: when the particle size is 0.2mm,the recovery rate of flotation reaches 61%, while at a particle size of 0.3mm,the recovery rate drops to 22%.
(1) Positive flotation method for lithium ores
Positive flotation of lithium ores refers to the addition of strong alkali flotation after grinding the ore (to avoid over-grinding and sludging). In a highly concentrated alkaline medium, with vigorous stirring and repeated scrubbing to remove impurities, oleic acid and its soap salts are added as collectors to directly float lithium concentrate while leaving gangue minerals in the tank. No depressants need to be added during this process.
(2) Reverse flotation method for lithium ores
Reverse flotation of lithium ores involves creating an alkaline environment using lime, adding starch or dextrin as inhibitors to prevent upward movement of spodumene, and using cationic collectors to make silicate gangue minerals float on the surface of pulp in the flotation cell. If there are iron-bearing minerals in the lithium ore, foaming agents such as HF or resin salts can be added to further help remove impurities such as iron-bearing minerals.
GUOGAO Machinery Research & Test Center has used full-size level flotation (without desliming), with one rough selection step followed by one scavenging step and four cleaning steps, resulting in a concentrate grade of 4.75% Li2O; after magnetic separation to remove iron impurities,the grade can reach above 5%. Furthermore ,after particle size analysis it was found that as particle size decreases,lithium distribution also decreases,and thus more stringent grinding requirements are needed due to this property of lithium ore.
3 Chemical Treatment Method
Chemical treatment methods are mainly used for extracting lithium from salt lake water. Firstly,salt lake water is evaporated on an area close to 405 hectares; after evaporation,the concentration of lithium chloride can reach 6%. During evaporation,sodium salt and potassium salt precipitate out from brine while remaining solution containing dissolved lithium becomes brine . This brine is then introduced into the factory and soda ash is used to convert lithium chloride into solid lithium carbonate.
4 Heavy Suspension Flotation Method and Heavy Liquid Separation Method
The relative density of spodumene is about 3.2, which is slightly higher than that of main gangue minerals such as quartz and feldspar that often coexist with spodumene. Therefore, heavy suspension flotation method can be used to make spodumene become a heavy mineral product while gangue minerals become light products.
5 Thermal Cracking Method
This method involves heating lithium-bearing ore to 1000-1200°C; after heating, the crystal structure of spodumene changes, its relative density decreases to around 2.40,and it becomes brittle and easily breakable . At this point , selective grinding method is used to turn spodumene into powder form while less grindable gangue minerals like quartz remain relatively coarse ; then screening or wind separation methods are employed for separation . This method can enrich raw ores containing 0.8%-2.0% Li2O in spodumene up to concentrates containing 4%-6% Li
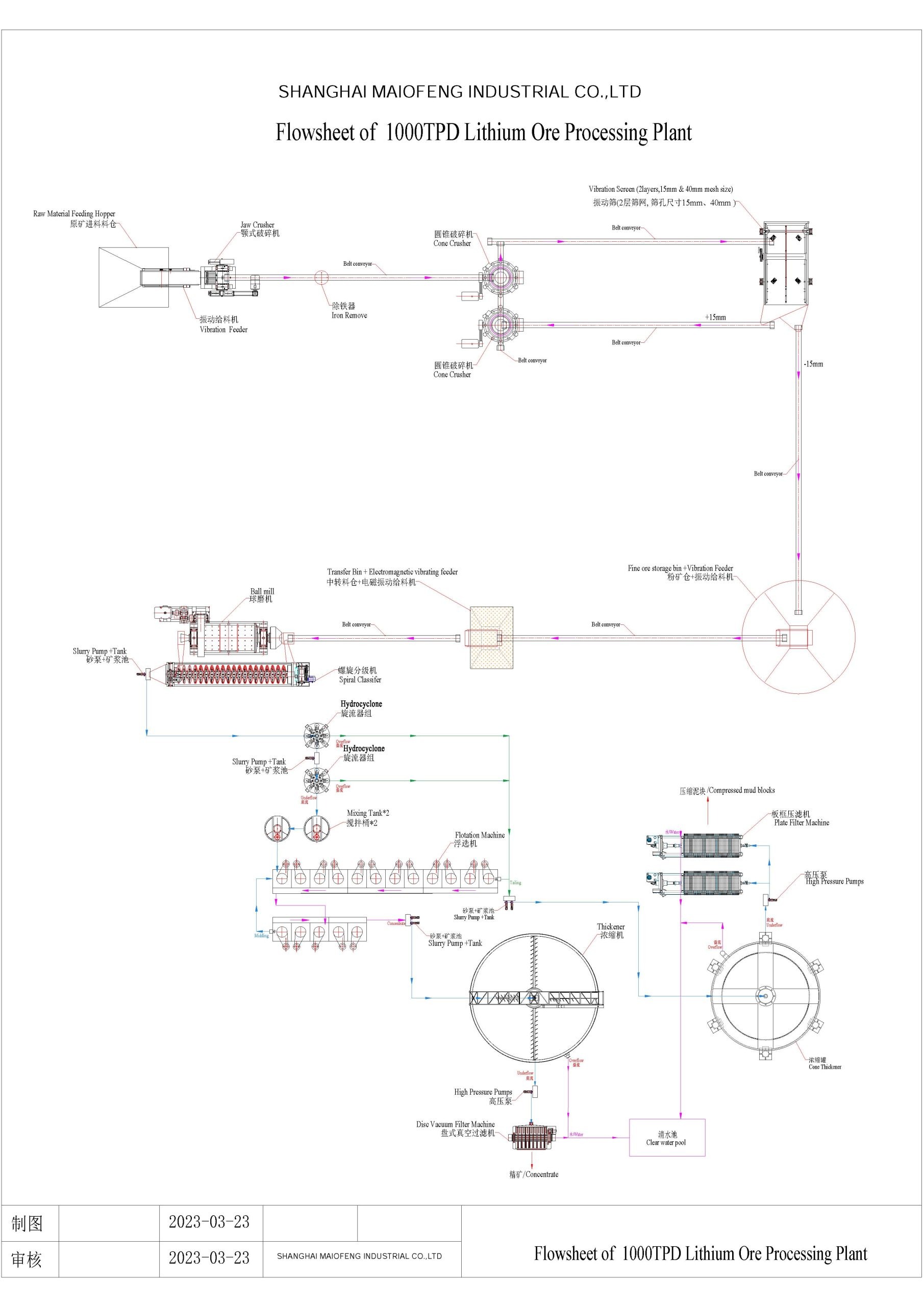