Graphite ore is formed by high-pressure metamorphism and generally appears as bluish-gray. After weathering, it turns yellow-brown or gray-white. The associated minerals are complex, mainly including feldspar, quartz, biotite, pyrite, magnetite, hematite and other impurities. According to the characteristics of flake graphite deposits and the properties of ores, the purification methods vary. The main methods for graphite ore beneficiation process include flotation purification method, alkali-acid purification method, hydrofluoric acid purification method, chlorination roasting purification method and high-temperature method.
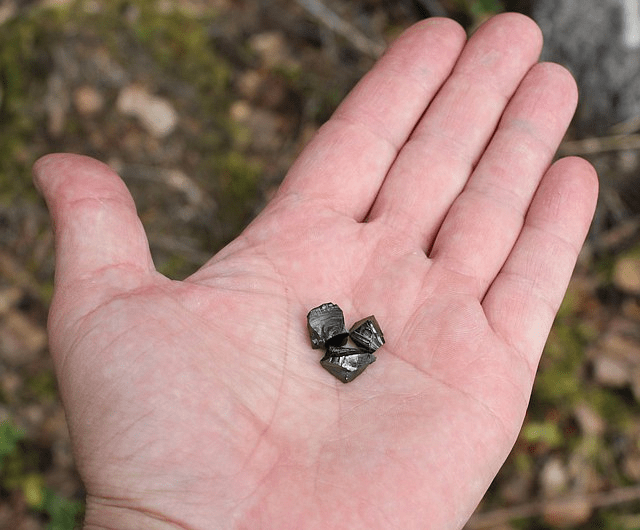
1.Graphite ore beneficiation process – flotation method for purifying graphite ore
Flake graphite ore has good floatability, so flotation can effectively separate graphite from other impurities. In order to protect the graphite flakes and improve the yield and grade of large-scale graphite, the process plant adopts a multi-stage roughing and regrinding, multi-stage selection process. This can timely screen out already dissociated large flake graphite and avoid repeated grinding and fragmentation of the flakes.
During the flotation process, coal oil, diesel oil, heavy oil, sulfonic ester, fatty acid sulfate, phenol compounds, carboxylic acids are commonly used as collectors; No. 2 oil and No. 4 oil are used as foaming agents.
The flotation purification method is mainly suitable for low-carbon flake graphite. It can effectively protect the graphite flakes and improve their grade while having low production cost and energy consumption. However, this process requires multiple stages of fine selection with high return rate of middlings and complex procedures which makes it difficult to control in production.
2.Graphite ore beneficiation process – alkali-acid method for purifying graphite ore
The alkali-acid purification method for flake graphite ore consists of an alkaline fusion process and an acid leaching process.
Alkaline fusion: By utilizing the acid-alkaline resistance property of graphite,sodium hydroxide is mixed with graphite in a certain proportion,then calcined at high temperature under melting state,the chemical reaction between alkali metal hydroxides (such as sodium hydroxide)and some impurities(such as quartz,silicate minerals,and silico-aluminate minerals)in graphites will generate water-soluble or acid-soluble salts.Then silicon removal by washing could be achieved to realize purification purpose。
Acid leaching: The product after desilication by alkaline fusion is subjected to acid leaching treatment, so that the impurities (metal oxides) that do not react with alkali during the melting process can be converted into soluble salts through reaction with acid. Graphite is purified after washing and other processes.
The alkali-acid purification method for flake graphite ore is mainly suitable for medium-carbon graphite and high-carbon graphite ore. This method has simple equipment, strong applicability, small one-time investment, and can obtain high-grade graphite. However, this process needs to be carried out at high temperature which leads to large energy consumption; the reagents used are corrosive to equipment and require a large amount of water.
3.Graphite ore beneficiation process – hydrofluoric acid method for purifying flake graphite ore
Hydrofluoric acid purification of flake graphite ore involves mixing graphite with hydrofluoric acid,reacting at a certain temperature for a period of time,generating compounds (or volatiles) soluble in water.Then impurities are removed by washing,and the purified graphite product is obtained after dehydration and drying.
In order to effectively prevent impurities (metal ions) from precipitating,a small amount of dilute sulfuric acid、dilute hydrochloric acid、dilute nitric acid or fluorosilicic acid will be added into hydrofluoric aci。
Graphite has good resistance to acids,but impurities such as quartz,silicate minerals contained in ores can react with hydrofluoric aci。Therefore,the hydrofluoricacid purification method is mainly suitable for purifying high carbon-graphite ores.This process has simple flow,strong adaptability,and low cost.However,hydrogen fluoride easily evaporates and it’s highly toxic.Improper use may cause safety accidents and environmental pollution.Therefore,safety precautions must be taken during use.Wastewater generated must meet standards before discharge.
4.Graphite ore beneficiation process – chlorination roasting method for purifying graphite ore
Chlorination roasting purification of flake graphite ore involves mixing graphite with a reducing agent in a certain proportion, and then high-temperature roasting in a designated equipment. Impurities (such as silicates and aluminosilicates) in the graphite will decompose into oxides such as SiO2, Al2O3, Fe2O3, CaO at high temperature. These oxides will react with chlorine gas to form gaseous or condensed chlorides. Then by utilizing the low boiling point of chlorides, they can be vaporized and removed through high-temperature roasting to achieve graphite purification.
The chlorination roasting purification method is mainly suitable for processing graphite ores containing silicate minerals. It has high purification efficiency but the toxic nature of chlorine gas used as a reducing agent can cause equipment corrosion and environmental pollution. Therefore, it is less commonly used in practical production.
5.Graphite ore beneficiation process – High-temperature purification process
The physical method mainly used for the purification of flake graphite is high-temperature purification. The melting point of graphite is 3773K, which is higher than that of silicates and second only to diamond. It is one of the substances with the highest melting and boiling points in nature. The high-temperature graphite purification method utilizes the difference in boiling points between graphite and impurities. Graphite ore is added to a graphite crucible, inert gas and protective gas are introduced under certain conditions, and specific equipment is used for heating. When the temperature reaches 2700℃, impurities vaporize and escape, thereby achieving the purpose of graphite purification. The high-temperature purification method has a high efficiency with a purity of up to 99.99%, but it can be affected by various factors, consumes a lot of energy, requires very high equipment and raw material requirements, and involves significant investment.
The above are common processes for selecting graphite ores. As for which one to choose, it depends on determining the mineral properties of flake graphite through ore dressing experiments and selecting suitable beneficiation processes in order to obtain ideal graphite concentrates.
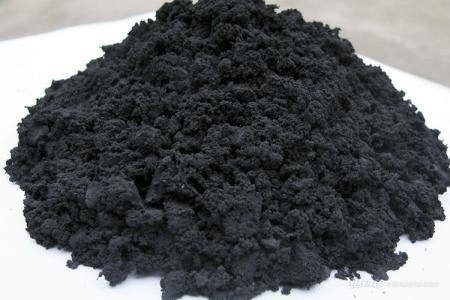
Graphite ore has good hydrophobicity, and the beneficiation process of graphite ore often uses flotation to achieve preliminary enrichment and purification. In order to obtain high-grade concentrate with high fixed carbon content, flotation generally requires one rough selection, one scavenging, and 2-10 times of fine selection operations. Due to the large number of grinding and sorting processes, a large amount of middlings (with a middlings yield generally ranging from 50% to 70%, or even more than 85%) is produced in the process. Therefore, it is necessary to treat the graphite middlings in order to improve the recovery rate.
Graphite products are divided into two categories: flake graphite and microcrystalline graphite. Flake graphite refers to natural crystalline graphite that resembles fish scales. It is a product obtained by processing, beneficiation, and sometimes purification of crystalline (flake-like) graphite ore. Microcrystalline graphite was formerly known as amorphous or earthy graphite. It refers to a dense aggregate composed of tiny natural graphite crystals formed by processing hidden crystalline (earthy) graphite ore through beneficiation and purification.
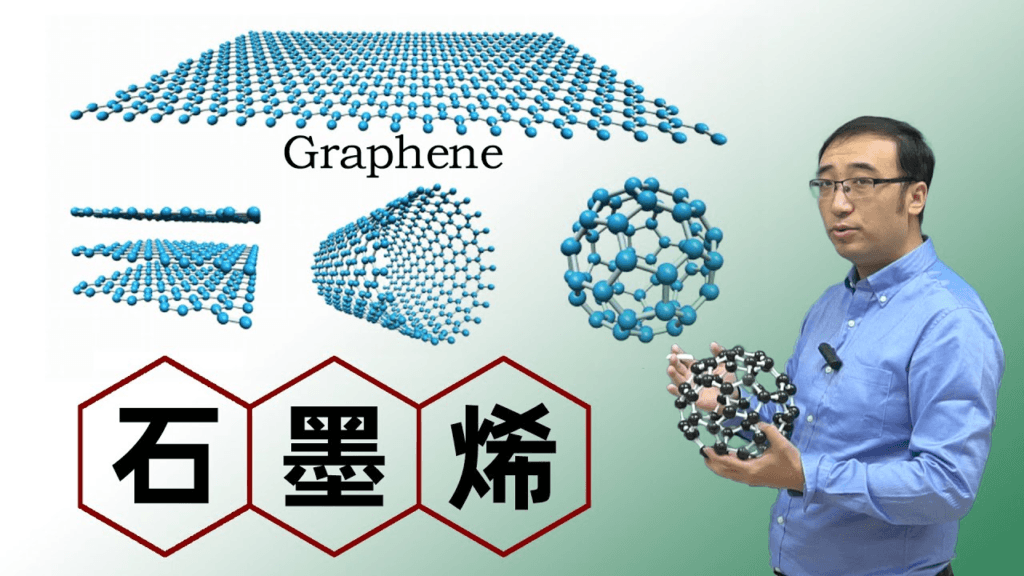
I. Beneficiation methods for crystalline graphite and beneficiation process for graphite ores
Crystalline graphites have good floatability naturally, so flotation method is basically used for their beneficiation in China. Since the size of flake graphites is one of its most important quality indicators, multi-stage grinding and multiple sorting processes are adopted in order to select large flake graphites as early as possible. Commonly used collectors for flotation include kerosene, diesel oil, etc., foaming agents include No.2 oil , No .4 oil , adjusting agents include lime , sodium carbonate , inhibitors include water glass .
Beneficiation process for crystalline graphites: Since the hardness of graphitic ores is generally medium-hard or medium-hard but soft with grades between 2% and 10%, the crushing process is relatively simple. It often adopts three-stage open circuit, two-stage open circuit, or one-stage crushing process. For small and medium-sized mines mainly processing weathered ores, they are directly sent to ball mills without crushing. The flotation process generally consists of multi-stage grinding, multi-stage sorting, and middlings sequential (or centralized) return in a closed-loop flow. There are three forms of multi-stage processes: regrinding of concentrates, regrinding of middlings, and regrinding of tailings. Crystalline graphites mostly adopt the process of regrinding concentrates, and under normal circumstances, the recovery rate can reach about 80%. Some mines have also tried the process of regrinding middlings but with no significant effect. Some small factories also use open-circuit or semi-open-circuit flotation processes due to excessive discarding of tailings points. The beneficiation recovery rate is very low, generally only 40% to 50%.
II. Beneficiation methods for hidden crystalline graphite and beneficiation process for graphite ores
Hidden crystalline graphites have extremely small crystals called microcrystalline graphites as well; graphite particles are often embedded in clay making separation difficult . Due to their high ore grade (generally containing carbon from 60% to 80%), many graphite mines directly crush the extracted ores for sale as graphite powder products . Lu Tang Graphite Mine in Hunan Province once established a flotation plant for floating microcrystalline graphites in the 1950s , but it was shut down due to high costs . Currently , some units are still conducting research on new processes such as oil agglomeration flotation for microcrystalline graphites .
Beneficiation process for hidden crystalline graphites: Although hidden crystalline graphitic ores have higher grades , they are difficult to separate . In China , it is usually the case that the extracted graphitic ores are simply hand-selected and directly crushed into products for sale . The general process is as follows: raw ore → coarse crushing → medium crushing → drying → grinding → grading → packaging.
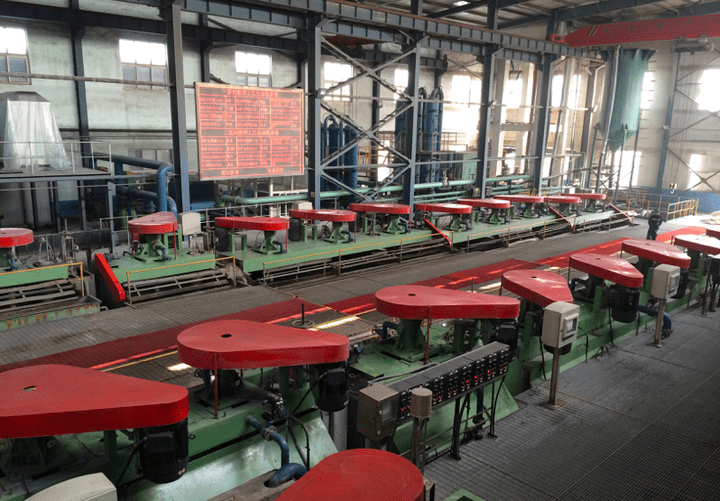
Graphite ore beneficiation process: mainly for various types of graphite ores with different crystal forms, associated with graphite ores such as pyrite or mica, using multi-stage grinding and flotation combined with regrinding and flotation.
- Graphite ore beneficiation process – Multi-stage grinding and flotation process: Due to the natural floatability of crystalline graphite and good floatability of flake graphite, Xin Hai usually adopts the method of multi-stage grinding and flotation for these two types of graphite ores in order to protect the graphite flakes and ensure that they are not damaged, ensuring that the concentrate quality meets requirements. In the process of multi-stage flotation, the application of flotation reagents: collectors should use diesel oil, heavy oil, kerosene, sulfonate esters, phenols, etc.; foaming agents should use No. 2 oil, No. 4 oil , butyl ether oil and ether alcohols.
- Graphite ore beneficiation process – Regrinding and flotation combined process: For graphite ores with multiple gangue minerals, Xin Hai Mining usually uses a combination of regrinding and flotation processes for graphite ore beneficiation. First use gravity separation to separate light minerals from heavy minerals; after separation, use flotation to float tailings containing light minerals.
Graphite ore beneficiation process – There are several methods for processing middlings in graphite mines including middlings concentration return flowback method (single stage or multiple stages), sequential return method (ordinary or hierarchical). Let’s understand the methods for processing middlings in detail.
I. Graphite ore beneficiation process – Middlings concentration return flowback
Middlings concentration return refers to merging middlings in the flowchart back into appropriate positions. Middling concentration returns include single stage middling concentration return(s), two stage(s) or multiple stage(s) middling concentration returns(s), concentrated remilling & returning flowsheet etc.. The advantage is simplifying the process, but when there are many middlings and significant differences in their properties, it may have adverse effects on flotation. If there are too many middlings, it can easily lead to large fluctuations in the flotation liquid level, high fixed carbon content of tailings, and decreased recovery rate of concentrate.
- Graphite ore beneficiation process – Single stage middling concentration return
Single stage middling concentration return means returning all the middlings in the flowchart to a certain operation point such as roughing, coarse grinding or primary selection depending on the nature of the middlings. Single stage middling concentration return is suitable for processing surface graphite sand mainly composed of schistose rock type and significantly improves the fixed carbon content of final concentrate. However, this method is difficult to control and has large process fluctuations. It is generally used in small-scale beneficiation plants.
- Graphite ore beneficiation process – Segmented middling concentration return
Segmented middling concentration return usually involves concentrating low-fixed-carbon-contentmiddlings into one operation point first and then merging high-fixed-carbon-contentmiddlings back into another operation point. The location for segmented middleconcentrationreturn can be determined based onthe propertiesandfixedcarboncontentofthemiddlings.Itisbeneficialtoimproverecoveryrateandensurethefinalconcentratehasthesamefixedcarboncontent.
II.Graphiteorebeneficiationprocess-Middlingssuccessivereturnprocess
Graphitemiddlesequentialreturnincludesordinarysequentialreturnandgradedsequentialreturn.Ingeneral,the sequential returnsuitableforgraphitewithpoorfloatabilitybutneedstorecoverhighly.Theordinarysequentialreturnsmeansthatthemiddlinsare returnedtothepreviousoperationonebyone,andthegradedsequentialreturnsmeansthatthemiddlinsarereturnednottothepreviousoperation,buttoanearlierstageinthe flowchart.Sequentialreturnsareapplicabletothecaseofpoorfloatabilityofgraphitebutneedtostrengthentherecoveryrate.Duetothelimitedopportunityforre-selection,sequentialreturnsensurethatlargescaleflakesarenotlost,hencethehighrecoveryrate.Sequentialreturnscan greatlyreducemiddlingcirculation,reducetheloadoncoarseandscavengingoperations,andbenefittheimprovementoforeconcentrationandrecoveryrate.However,due to the sequential return of middlings, it reduces the opportunity for selection. Due to dilution in previous operations and more associated minerals in middlings, it is easy to reduce the fixed carbon content of final concentrate. However, if there are fewer associated minerals in middlings, lower pulp concentration, using sequential returns can be beneficial for improving concentrate grade and recovery rate. In addition, when middlings are sequentially returned, the water carried by them can reduce the addition of fresh water in flotation operations compared with other return methods. It reduces the burden of beneficiation plant’s thickening and dewatering process and increases the utilization rate of recycled water. However,theopportunityforremillingandreseparationafterthesequential