Copper extraction techniques refer to methods for obtaining copper from ores. This involves a series of chemical, physical, and electrochemical processes that have evolved and vary by country based on the ore source, local environmental regulations, and other factors.
Like all mining operations, the ore must typically be concentrated through beneficiation. To do this, the ore is crushed and then roasted to convert sulfides into oxides. These oxides are smelted to produce matte, which undergoes various refining processes including electrolysis. Many of the byproducts of extraction are reclaimed for economic and environmental reasons. For example, sulfur dioxide gas is captured and converted into sulfuric acid for use in the extraction process.
Most copper ores contain only a small percentage of copper metal bound within valuable minerals, with the rest being unwanted rock or gangue minerals such as silicate or oxide minerals that hold little value. In the 21st century, the average grade of copper ores is below 0.6% copper, with less than 2% of total volume consisting of economically valuable ore minerals (including copper). The main objective in treating any ore metallurgically is to separate valuable minerals from gangue minerals within the rock.
The initial stage in any metallurgical treatment circuit involves accurate grinding or comminution where rocks are crushed into small particles (<100 μm) made up of individual mineral phases. These particles are then separated to remove gangue before undergoing physical liberation to separate ore minerals from rock. The liberation process depends on whether the copper ores are oxide or sulfide.
Subsequent steps depend on the nature of the copper-containing ore. For oxide ores, a hydrometallurgical liberation process is usually used that takes advantage of their soluble nature in order to treat them at metallurgical treatment plants effectively. Froth flotation is employed for both secondary (supergene) and primary (unweathered) sulfide ores to physically separate them from gangue. In the case of special native copper-bearing ore bodies or sections rich in supergene native copper, a simple gravity circuit can be used to recover this mineral.
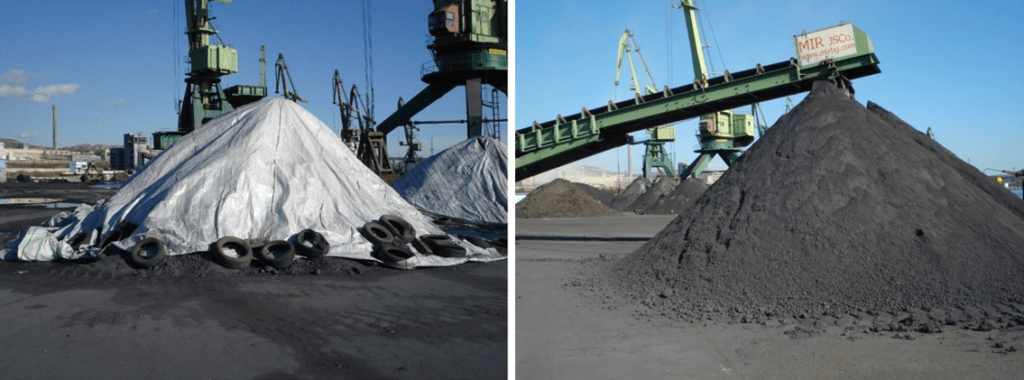
Copper concentrate is the initial product of the copper production line and consists of roughly equal parts copper, iron, and sulfide. Concentrates are used as raw materials for all copper smelters, which process them to obtain impure forms of metallic copper known as anode or blister copper. These forms are later used to produce high-purity refined copper. The production of concentrates involves crushing and milling the ore until it reaches a particle size that allows for flotation-based extraction of copper. Copper concentrates from different regions typically contain between 24% and 36% copper. Afterward, they undergo a final filtration and drying process to reduce humidity levels to 8-9%.
Production Process
Copper goes through various stages and degrees of refinement during its production process, with byproducts such as molybdenum, sulfuric acid, and precious metals also present in the ore.
Mining and Crushing
Grinding
Concentrating
Leaching or Smelting
SX/EW or Electro Refining
Copper is processed in multiple stages starting from ore extraction and crushing until electrolytic refining yields pure Copper Cathodes with a purity level of 99.99%.
The first step in obtaining any form of commercial-grade copper involves mining sulfide or oxide ores through digging or blasting followed by crushing them into walnut-sized pieces.
The crushed ore is then ball- or rod-milled in large rotating cylindrical machines until it becomes a powder containing less than 1 percent copper on average. Sulfide ores proceed to a concentrating stage while oxide ores are directed towards leaching tanks.
The initial commercial product derived from this process is called “copper concentrate,” which contains mainly copper along with iron and sulfide components. Additionally, molybdenum bi-sulfide can be obtained during this stage; it undergoes further processing to become commercially viable molybdenum trioxide.
Minerals are concentrated into a slurry containing approximately 15% copper. Waste slag is removed, and water is recycled. Tailings (remaining earth) that contain copper oxide are either directed to leaching tanks or returned to the surrounding terrain. Once copper has been concentrated, it can be transformed into pure copper cathodes using two different methods:
Leaching & Electro-Winning
Smelting & Electrolytic Refining
Copper concentrate is smelted and converted into metallic copper, which can then be further refined to a purity level exceeding 99%. This refinement process yields forms such as copper anode and blister copper. Copper anode serves primarily as raw material in the electrolytic refining process for producing high-purity electrolytic refined cathodes with a purity of 99.99%.
Leaching & Electro-Winning Method
A. Leaching
Oxide ore and tailings undergo leaching using a weak acid solution, resulting in a weak Copper Sulfate solution.
B. Electro-Winning (SX/EW)
The solution laden with copper ions is treated and transferred to an electrolytic process tank where pure copper ions migrate directly from the solution onto starter cathodes made of pure copper foil. Precious metals can also be extracted from the solution.
Smelting & Electrolytic Refining Method
A. Smelting
Multiple stages of melting and purifying the content of copper lead successively to matte, blister, and finally 99% pure copper products. Recycled copper begins its journey towards reuse by being re-smelted.
B.Electrolytic Refining
Anodes cast from nearly pure copper are immersed in an acid bath where pure-copper-foil or steel “starter sheets” act as receiving surfaces for migrating purified-copper ions during electrolysis; these ions accumulate on the sheets until they form refined-copper cathodes.
During this process, gold, silver, and platinum may be recovered from the used electrolytic bath.
After smelting and conversion, a metallurgical gas generation treatment produces additional by-products such as sulfuric acid and anodic slimes rich in silver and gold.
Copper Standards & Types
In the copper industry’s supply chain, mining companies extract ore from deposits and process it to obtain highly pure metal that is sold to fabricators of semi-manufactured products. These fabricators then transform the metal before offering it to end consumers.
Electrolytic copper cathodes are produced in various grades, including off-grades used for low-conductivity appliances and alloys. Cathodes primarily consist of four different qualities: LME registered high grade, non-registered high grade, standard grade, and off-grade. Copper refineries registered with LME manufacture LME registered High (A) Grade cathodes along with Non-LME registered High (A) Grade cathodes, Standard Grade cathodes, and off-grade cathodes.
According to LME copper contract specifications, the sulfur ratio in cathodes must not exceed 15ppm to meet designated standards. In certain regions, copper refineries may produce their LME registered
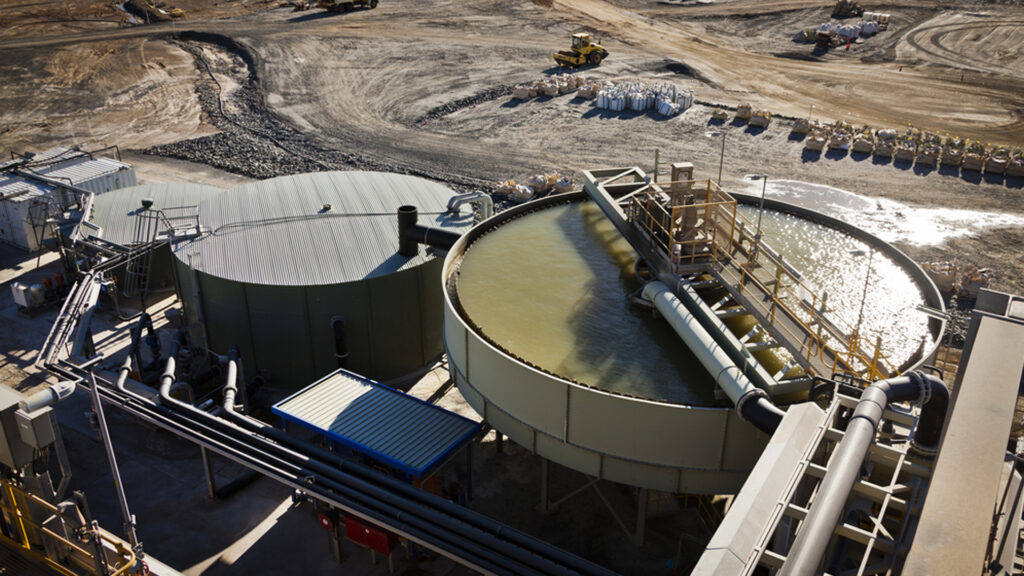