Characteristics of Barite
Barite (baryte) is a mineral composed of barium sulfate (BaSO4). The mineral barite (BaSO4) is the principal ore for the element barium, which has the chemical symbol Ba. The heavy metal barium is silvery, soft, highly reactive, and does not occur in its elementary form in nature. Barium is commonly found within the mineral barite, bound with sulfur and oxygen. Barite occurs as pale yellow or colorless tabular crystals. The exploration for and development of petroleum and natural gas resources accounts for nearly 95 percent of domestic consumption and about 90 percent of global consumption of barite.
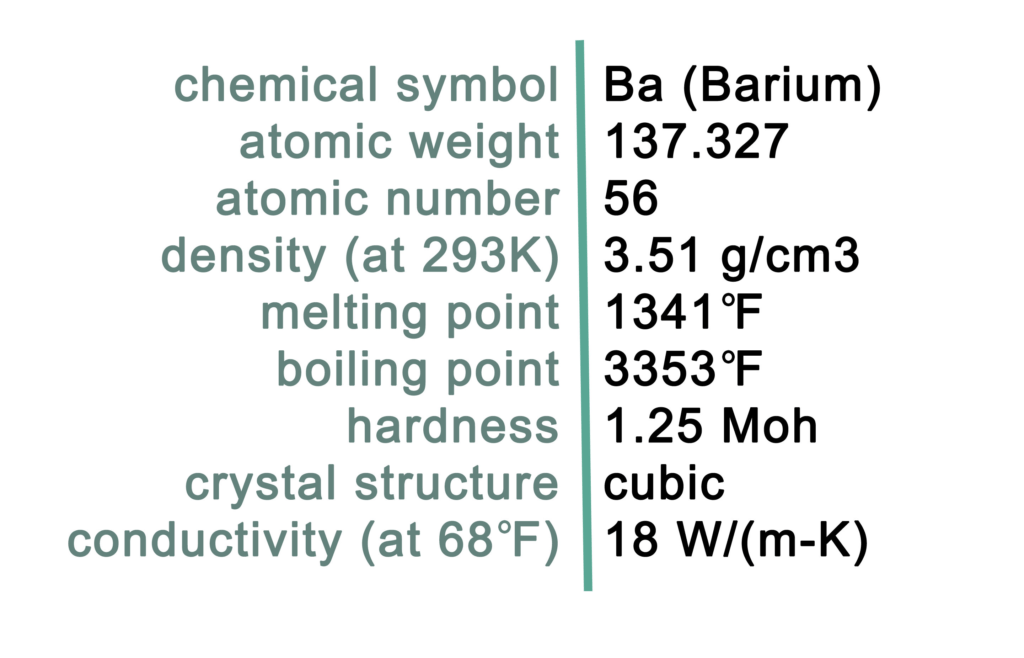
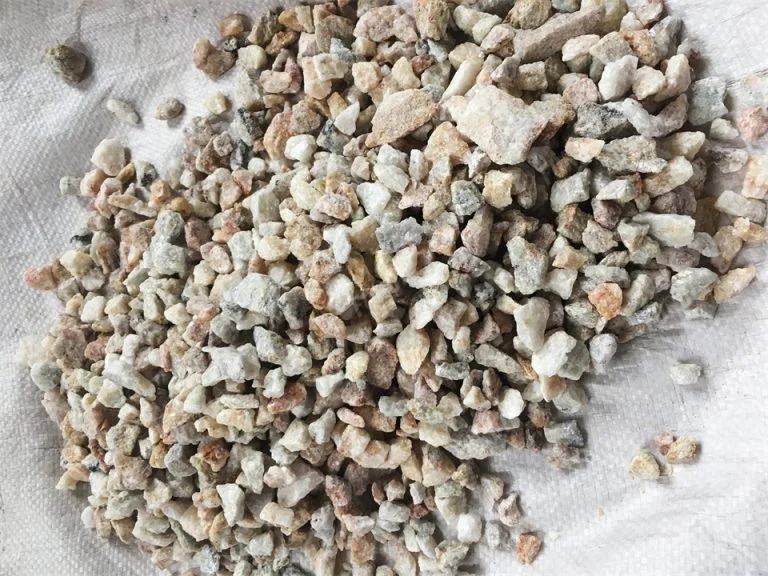
Uses of Barite
Barite is considered a critical mineral in domestic metallurgical applications for energy technologies (Fortier et al., 2018). It is a key component in drilling mud used by the oil and gas industry to prevent blow-outs caused by high pressures. Mined barite is ground into a fine powder and mixed with mud to create a heavy slurry. This slurry is poured down the drill hole, forming a plug around and above the drill bit. Due to its softness, barite does not damage the drill bit, but its high specific gravity effectively counteracts upward pressure, reducing the risk of blow-outs.
Elemental barium is added to optical glass, ceramic glazes, and other products. Barite serves as a weighing agent in various applications such as paper production, brakes, and even playing cards. It is commonly used in paints and rubber manufacturing as well, acting as a filler or enhancing brilliance and clarity. In the medical industry, barite is utilized for radiation shielding or to enhance contrast in radiographs.
Barium in its elemental form is classified as a toxic heavy metal.
Barite Geology
Barite deposits can form through different processes. As bedded sedimentary deposits, barite forms when marine sediment binds barium through biological activity on the ocean floor. These sediments lithify into shale or mudstone with nodular, rosette-like, bedded or massive forms of barite present. Barite can also occur within cavities or veins where permeable rocks allow high-temperature fluid flow leading to precipitation of associated minerals. Extensive formation of barite can be observed along faults and breccia zones or confined within smaller irregular cavities within rocks. Additionally,
barite deposits may result from weathering of cavity-fill mineralization within carbonate host rocks; residual deposits accumulate when these rock formations rich in barites undergo weathering processes.
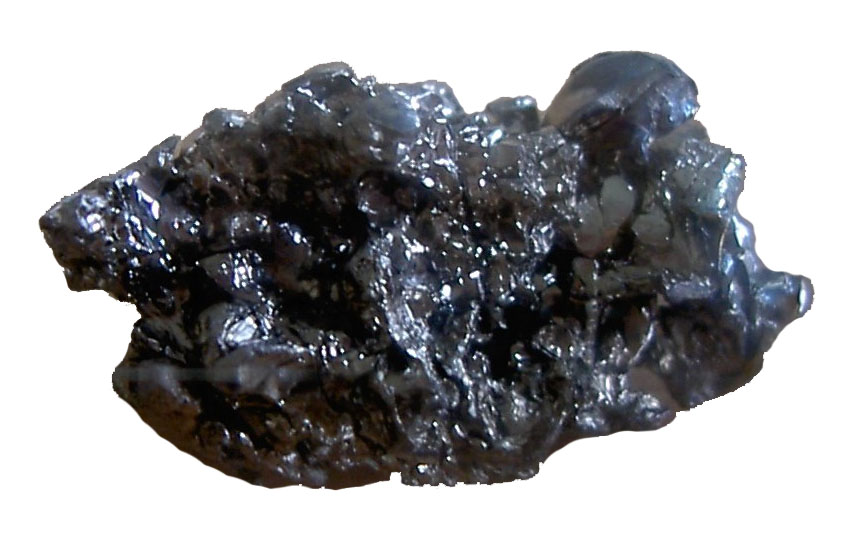
Barium in its elementary form – a toxic heavy metal.
Mineral System | Deposit Type | Geologic Provinces |
---|---|---|
Basin brine | Replacement and bedded barite | Valley and Ridge |
Basin brine | Strata-bound replacement, veins, breccia fill | Piedmont, Blue Ridge |
Table 2: Prospective barite mineral systems, deposit types (Hofstra and Kreiner, 2020), and geologic provinces in Virginia
Barite in Industry
The United States does not maintain a supply of barite in the National Defense Stockpile and is import reliant with approximately 87 percent imported from China, India, Morocco, and Mexico. Economic deposits of barite are relatively common and distributed across the world. Production within the United States is primarily from Nevada and Georgia. Smaller deposits are known in other states across the country.
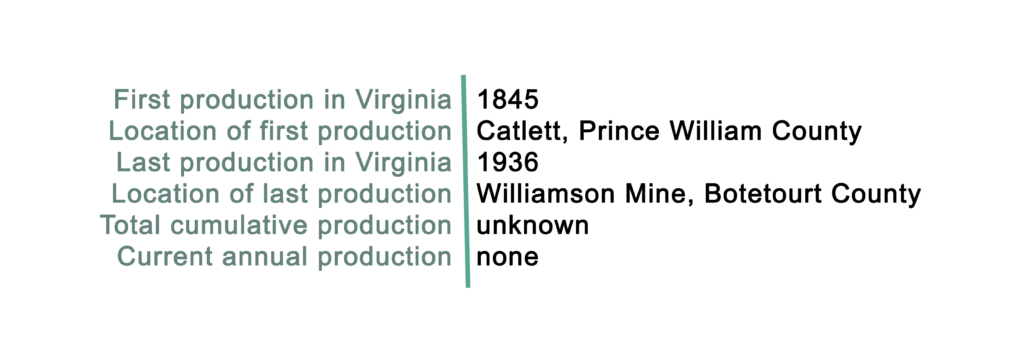
Barite has been mined in Virginia for many years and can be found in numerous counties across the state. However, commercial production is limited to only a few mining areas. The first barite mine in Virginia was established as early as 1845 near the town of Catlett in Prince William County. After the Civil War, additional mines opened and successfully produced barite on a larger scale. Valley and Ridge rocks have consistently served as significant sources of barite in Virginia.
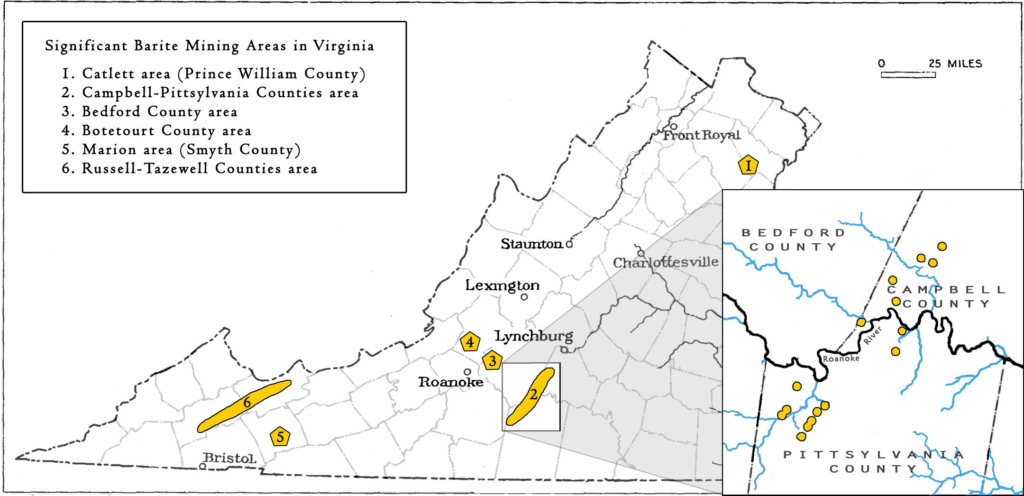
Prince William County
Barite mining in Catlett, Virginia
Barite Mining Catlett, Virginia
Photo from Watson, 1907.
Barite was first mined in Prince William County near the town of Catlett. Mining occurred intermittently between 1845 and 1903. The barite deposits were found within a fracture zone of limestone breccia and sandy shales with fractures filled with barite (Watson, 1907). The old mining operations consisted of open cuts, three shafts reaching a depth of 108 feet, a grinding mill, and a crushing house (Watson, 1907).
Campbell/Pittsylvania Counties
Several mines are scattered along a belt that stretches for 30 miles through Campbell, eastern Bedford, and Pittsylvania Counties. Barite has been mined in the residuum since at least the 1870s (Watson 1907; Edmundson, 1938). In this area, barite is associated with marble and can be identified on the surface by distinctive red clay rich in iron and manganese (Edmundson, 1938).
Bedford County
Barite was first mined in Bedford County in 1866 but yielded minor results and likely lasted only a few years (Edmundson, 1938). Two mines are located just west of the town of Bedford: Saxton Mine and McMillan Mine. Shallow cuts and trenches hundreds of feet long and up to forty feet deep were used for prospecting barite. Vertical shafts were also dug. During its initial operation period, a small quantity of barite was extracted and shipped for use. The mines briefly reopened in 1906 when a thirty-inch-wide vein of barite was discovered in bedrock.
Botetourt County
One of the earliest barite mining operations in Virginia took place in Botetourt County. In1850 several prospect pits as well as an open cut and a shaft were dug (later named the Williamson Mine) into Conococheague limestone residuum just north of Fincastle. Several other sites were prospected, and small quantities of barite were extracted until mining operations ceased in 1906. Operations resumed in 1934 when prospecting led to the discovery of additional barite deposits near Fincastle. During the final years of production (1935-1936) in this area, between seven and nine thousand tons of barite are reported to have been extracted from four deposits. Although these deposits were commercially viable, they were relatively small in size, and field examinations indicated that most of the residual and replacement barite had been mined out by 1936.
Russell/Tazewell and Smyth Counties
Barite mining began in southwestern Virginia around 1875 and became a commercial source by 1880. There are two main mining areas: Russell and Tazewell Counties, as well as Smyth County (Watson, 1907). In both areas, barite occurs with limonite, calcite, siderite, and occasional fluorite as stratified replacements within limestone and dolostone formations from the Ordovician Beekmantown Formation. Loose nodules of barite may also be found in the residuum.
The northeast-trending belt of Beekmantown rocks following the Clinch River was a primary source for barite in Virginia. This stretch spans 35 miles through Russell and Tazewell Counties where many mines produced barite ore between 1880 and 1908. Along this belt several mills were built to crush barites for shipment.
The Leonard Mine operated between 1902-1905 at Russell County’s largest producers’ site for Barites – Leonard Hubbard Counts mine which had an open cut into Beekmantown dolomite where veins filled with fractures of barite were present. A significant amount of barite was also extracted from bedrock fractures in a 400-foot-long cut at the Counts mine. Barite was extracted from bedrock in several trenches and a shaft at the Hubbard mine.
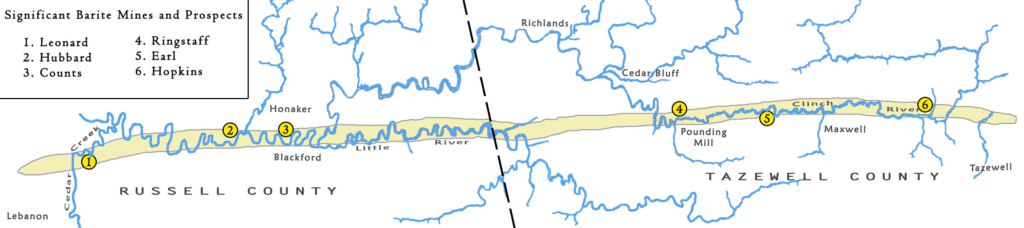
In Tazewell County, barite was extracted from both bedrock seams and residuum. The Hopkins, Earl, and Ringstaff mines were the primary producers in this county. At the Hopkins mine, extensive mine shafts (reaching a depth of 50 feet) and connecting tunnels were constructed through Beekmantown dolomite. In 1904, a total of 234 tons of barite was extracted during a six-month period. The Earl mine is an open cut that measures 250 feet in length and has a depth of 20 feet. The two cuts at the Ringstaff mine were among the largest producers of residuum barite in the area.
Barite deposits can be found within a three-mile radius of Marion in Smyth County, possibly indicating localization along fractures associated with the uplifted Marion dome (Cooper, 1936; Edmundson, 1938). Mining operations began here in 1875 and continued until 1906. The H.P. Copenhaver mine played a significant role as it produced high-grade barite extracted from residuum through open cuts.
While Virginia historically served as an important source for barite, most mines have depleted their deposits. Nuelle and Shelton (1986) investigated potential undiscovered bedded barite deposits in the Valley and Ridge region. They reported that Devonian age rocks such as Needmore Shale, Marcellus-Millboro shale formations, and Tully Limestone commonly contain barite nodules enriched with isotopically heavy sulfur (34S), suggesting remobilization from an incipient source rock for barite. These researchers suggested further exploration of these Devonian rocks to uncover economically valuable barite beds deposited during early stages of Acadian deformation.
References:
- Barite (Barium), Chapter D in Critical Mineral Resources of the United States – Economic and Environmental Geology and Prospects for Future Supply.
- Brobst, D. A., 1970, Barite: World Production, Reserves, and Future Prospects.
- Burfoot Jr., J. D., 1935, The Barite Deposits of the Southern Appalachian States.
- Edmundson, R.S., 1938, Barite deposits of Virginia: Virginia Geological Survey Bulletin 53.
- Fortier et al., 2018, Draft Critical Mineral List – Summary of Methodology and Background Information – U.S. Geological Survey Technical Input Document in Response to Secretarial Order No. 3359.
- Hofstra, A.H., and Kreiner, D.C., 2020, Systems-Deposits-Commodities-Critical Minerals Table for the Earth Mapping Resources Initiative.
- Nuelle L.M. and Shelton K.L.,1986 Geologic and geochemical evidence of possible bedded barite deposits in Devonian rocks of the Valley and Ridge province,
Appalachian Mountains: Economic Geology v.81
p1408–1430
-Watson T.L.,
1907 Mineral Resources of Virginia:
The Virginia Jamestown Exposition Commission
The barite beneficiation production line typically utilizes gravity beneficiation, as it is an energy-saving, efficient, and environmentally friendly method. The primary workflow includes crushing, screening, beneficiation, and dewatering processes. Equipment such as crushers, vibrating screens, jiggers, and dewatering screens are used in the production line. The specific equipment configuration depends on the characteristics of the barite ore. If the mud content is high in the ore, a washing process may also be required.
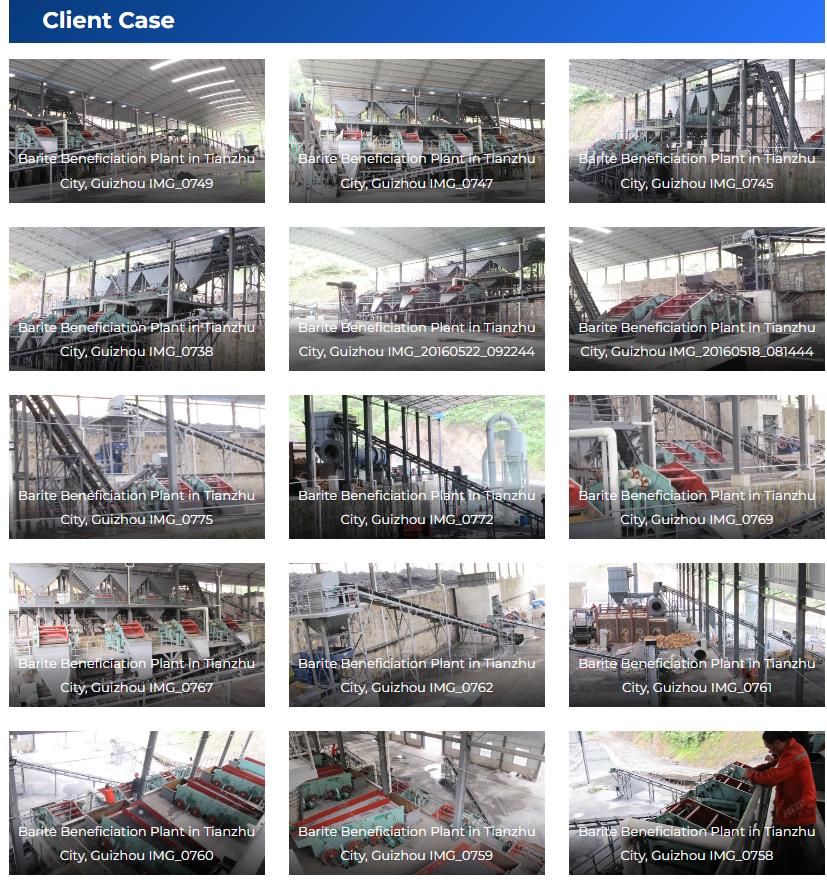