Manganese is a crucial industrial metal, often referred to as the “essential element for steel production.” Following the processing of manganese ore, its products find extensive applications in industries such as steel manufacturing, battery production, non-ferrous metallurgy, electric vehicles, and chemistry.
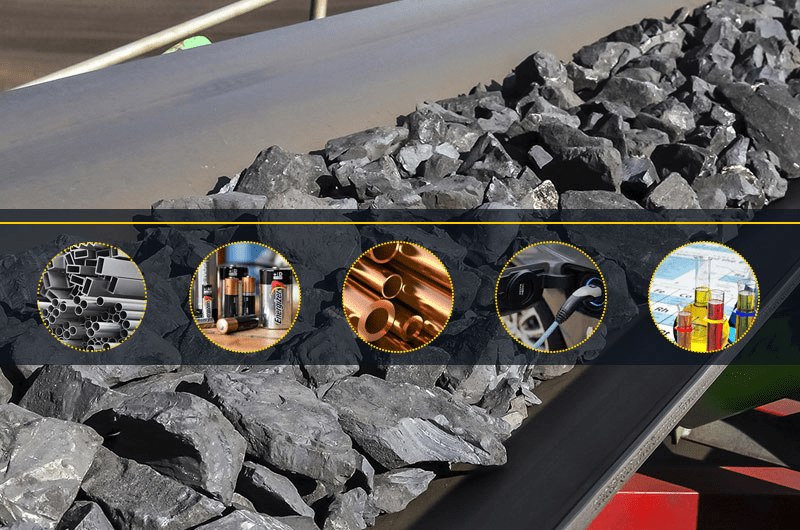
Why should we focus on manganese ore processing?
According to a report by Research and Markets, the global market for manganese alloy is projected to reach USD 21.23 billion by 2027. This growth will be primarily driven by the increasing use of steel and the rising demand for new energy vehicles.
Given the significant role that manganese plays in modern society, it is considered a lucrative investment opportunity. The growing demand for manganese ore has greatly spurred the development of beneficiation techniques and has led to increased attention towards refining processes and equipment used in manganese ore processing.
The manganese ore processing flow consists of five main steps: crushing, washing, grinding, dressing, and drying. Now I will provide you with a detailed introduction to the production line for manganese ore processing.
1.Manganese ore crushing process and equipment
Manganese ore crushing is the first step in the process, which involves conventional multi-stage crushing equipment.
Process flow: Vibrating feeder → jaw crusher → hydraulic cone crusher → vibrating screen
① Jaw crusher — primary crushing
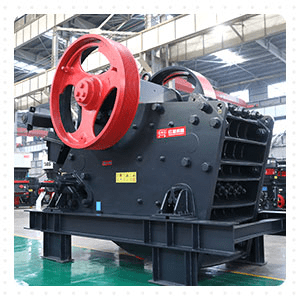
The loading equipment transports the raw manganese ore (≤350 mm) to the silo, and it is then evenly sent to the jaw crusher for coarse crushing by the vibrating feeder.
Estimated cost: $1,000 per set.
② Hydraulic cone crusher — secondary crushing
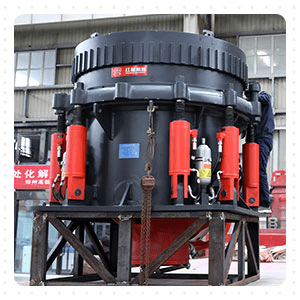
The belt conveyor transports the manganese ore (≤30 mm) that has been coarsely crushed to the hydraulic cone crusher for medium and fine crushing, following the principle of reducing grinding through increased crushing.
Estimated cost: $5,000 per set.
③ Vibrating screen — sieving particle size
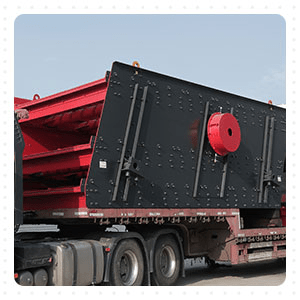
After being sieved by a vibrating screen, the manganese ore measuring 0-10 mm is transported to a silo where it awaits grinding. If the ore size exceeds 10 mm, it is sent back to the cone crusher for further crushing.
Estimated cost: $500 per set.
2. Manganese ore washing process and equipment
If the manganese ore contains a significant amount of sediment, adding a washing process can enhance the efficiency of manganese beneficiation. The ore can be washed directly on the vibrating screen or cleaned using a trommel screen.
Trommel screen — washing and screening
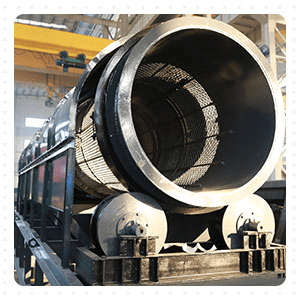
The trommel screen is a new cleaning and screening equipment used for washing manganese ore. It has a high rotating speed to wash and screen out the ore slime.
Estimated Cost: $2,655 per set.
3.Manganese ore grinding process and equipment
The mill grinds the crushed manganese ore into finished products with the required specifications in various fields, laying the foundation for the subsequent dressing process.
Process flow: Ball mill → Spiral classifier.
① Ball mill — further grinding
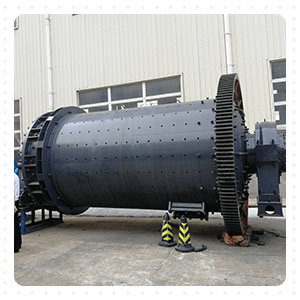
The ball mill can grind ore into a fine and uniform particle size. The 0-12 mm manganese ore is sent to the ball mill for grinding, resulting in manganese powder of 0-1 mm.
Estimated cost: $5,000 per set.
② Spiral classifier — classifying
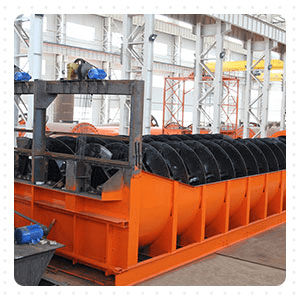
The spiral classifier is essential for classifying solid particles based on their different settling speeds. It can effectively classify manganese ore powder and also serve the purpose of desliming.
Estimated cost: $5,000 per set.
4. Manganese ore dressing process and equipment
According to the manganese ore plant, different types of manganese ore have different process flows. To choose appropriate beneficiation equipment:
Manganese oxide ore
Such as psilomelane, pyrolusite, manganite, etc.
Gravity separation method is applicable: Jig machine → shaking table
Manganese carbonate ore
Such as rhodochrosite, calcium rhodochrosite, calcite with manganese, etc.
Flotation or flotation-magnetic separation is applicable: Flotation machine → magnetic separator
Iron manganese ore
Gravity-magnetic separation is applicable: Shaking table → magnetic separator
For polymetallic composite manganese ore , the composition of the ore is more complex. The dissociation of manganese minerals is not easy. Comprehensive methods such as washing, gravity separation, flotation, magnetic separation and roasting should be adopted to combine mineral components.
① Shaking table — manganese ore gravity separation
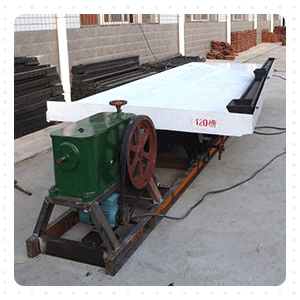
The shaking table is ideal for separating fine-grained manganese oxide ore, allowing for the extraction of high-grade concentrate and waste tailings. It is user-friendly and highly efficient in sorting.
Estimated cost: $1,000 per set.
② Jig machine — manganese ore gravity separation
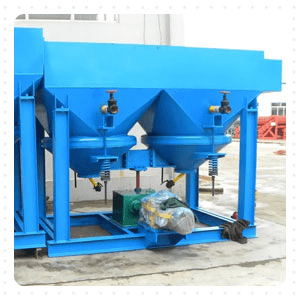
The jig is designed for processing coarse-grained manganese ore and serves as equipment for sorting minerals and gangue based on density differences. It is suitable for handling large particle sizes.
Estimated cost: $1,800 per set.
③ Flotation machine — manganese ore flotation
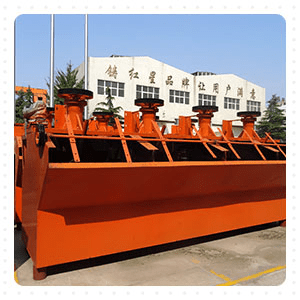
The flotation process offers high flexibility. The choice of reagents depends on the type and quality of the ore. Anionic reverse flotation is commonly used in most manganese ore plants to produce high-grade manganese concentrate.
Estimated cost: $1,170 per set.
④ Magnetic separator — manganese ore magnetic separation
Manganese is a mineral with weak magnetic properties that can be efficiently separated using strong magnetic separation. This machine is designed for removing iron from manganese ore, which aids in the recovery of resources.
Estimated cost: $1,100 per set.
5.Manganese ore drying process and equipment
After the beneficiation process, the machine discharges the manganese ore concentrates and tailings along with a significant amount of water. In order to transport them to either the concentrate plant or tailing plant, they need to undergo dehydration.
Process flow: Concentrator → Dryer → Concentrates/Tailings
① Concentrator — dehydrating treatment
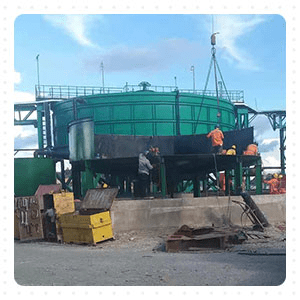
The high-efficiency concentrator is a machine used for concentrating and clarifying manganese concentrates and tailings. It can increase the pulp concentration from 20-30% to approximately 40-70%. The estimated cost is $3,326 per set.
② Rotary dryer — drying manganese powder
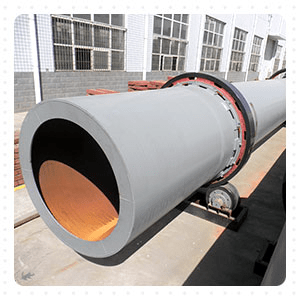
The rotary drum dryer is the optimal choice for drying in manganese ore processing, as it effectively eliminates excess water from manganese minerals and yields dry manganese powder. Estimated cost: $1,000 per set.
Conclusion on Manganese Ore Processing
This flowchart represents a widely used method for processing manganese ore, which efficiently achieves the highest recovery rate at minimal cost. Additionally, Ftmmachinery can tailor flows and machines to suit your specific manganese ore project, offering expert guidance at affordable rates.