Lepidolite is a captivating mineral abundant in lithium, extensively utilized in lithium-ion batteries, electric vehicles, glass ceramics, and greases.
Nevertheless, the composition of lepidolite is intricate. How does lepidolite acquire lithium concentrates? This blog will unveil the entire process and equipment used for lepidolite processing.
Lepidolite is an emerging lithium resource
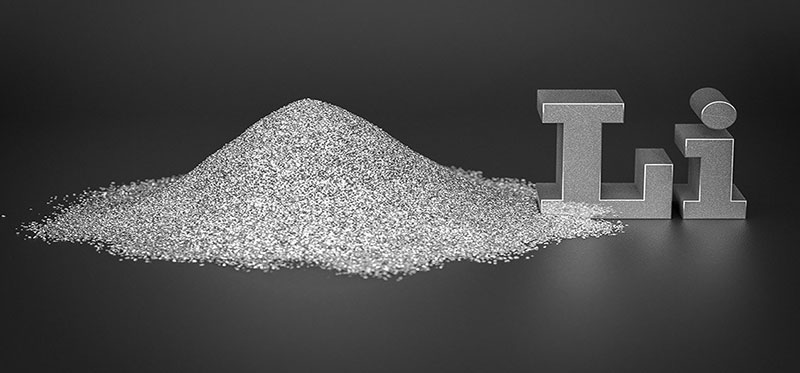
Lepidolite, also known as “scale mica,” gets its name from the Greek words “lepidos” and “lithos,” meaning “scale” and “stone” respectively. This name describes the mineral’s scaly or layered appearance, which is a result of its sheet-like crystal structure. Lepidolite belongs to the mica group of minerals and has a layered structure. It is the most common lithium mineral, typically containing 1.23%-5.90% Li₂O. The iron-rich variation of lepidolite is called iron lepidolite, serving as a transitional product between lepidolite and biotite.
What are the physical properties of lepidolite?
The chemical formula of lepidolite is K(Li,Al,Rb)₂(Al,Si)₄O₁₀(F,OH)₂. It primarily consists of potassium, lithium, aluminum, and silicate. Other minerals found in lepidolite may include small amounts of iron, sodium, rubidium, and cesium.
Lepidolite has a Mohs hardness ranging from 2.5 to 4 and exhibits a glassy to pearly luster. It shows perfect basal cleavage. Lepidolite is mainly produced in pegmatite-type lithium deposits and occurs together with feldspar, quartz, spodumene, muscovite, and tourmaline.
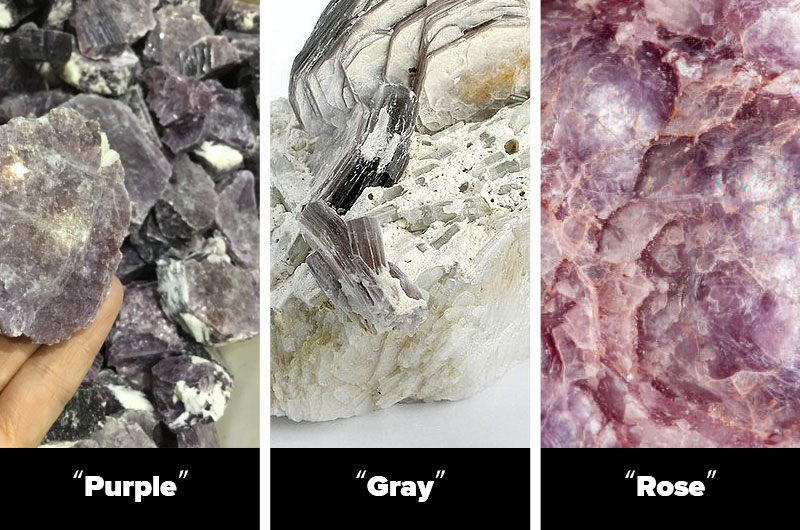
Lepidolite is available in various colors such as purple, pink, rose, and gray. The color of lepidolite is typically a result of the presence of manganese, which can oxidize and create a lovely pink or purple hue.
Because it contains high levels of lithium, lepidolite is mined for lithium extraction purposes. The technological process for extracting lithium from raw ore involves four steps: crushing, grinding, separation, and dehydration.
Now let’s explore the necessary lepidolite processing equipment for each stage with GUOGAO MINE
Crushing equipment of lepidolite
Based on the properties of lepidolite, it is commonly crushed using a two-stage closed-circuit process. Once crushed, the lepidolite is then fed into a ball mill to regulate the particle size to approximately 15 mm.
PE jaw crusher
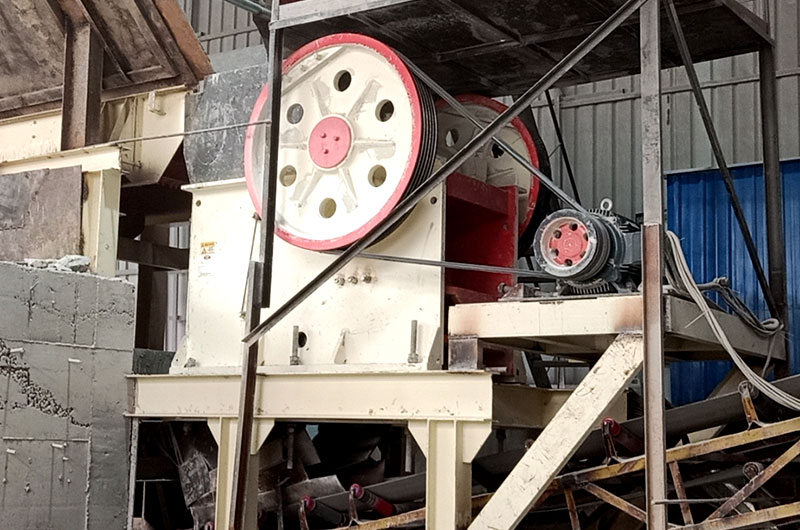
What are the benefits of using a PE jaw crusher?
A PE jaw crusher is ideal for coarse crushing lepidolite, with an output particle size ranging from 20 to 350 mm.
It features a large feeding port and deep crushing cavity, allowing it to process large pieces of lepidolite ore (<1200 mm).
With its high crushing ratio and productivity, it can handle a capacity of 50-1280 t/h for crushed lepidolite.
Additionally, it has a simple structure that makes maintenance convenient and keeps operating costs low.
HPM hydraulic cone crusher
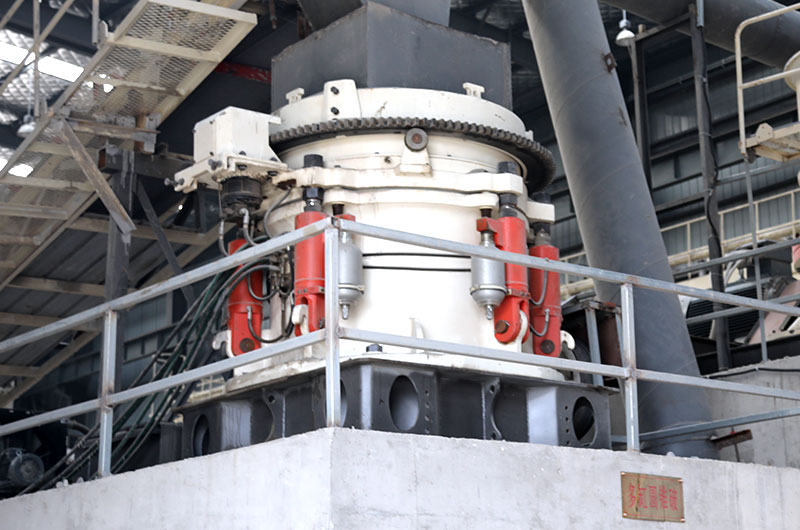
What are the benefits of using an HPM hydraulic cone crusher?
The HPM hydraulic cone crusher is designed for secondary and fine crushing of lepidolite, resulting in an output granularity of 10-38 mm.
It features a hydraulic protection system and thin oil lubrication system to enhance the lifespan of the lepidolite production line.
By utilizing lamination and crushing techniques, the lepidolite products achieve uniform particle sizes.
YK circular vibrating screen
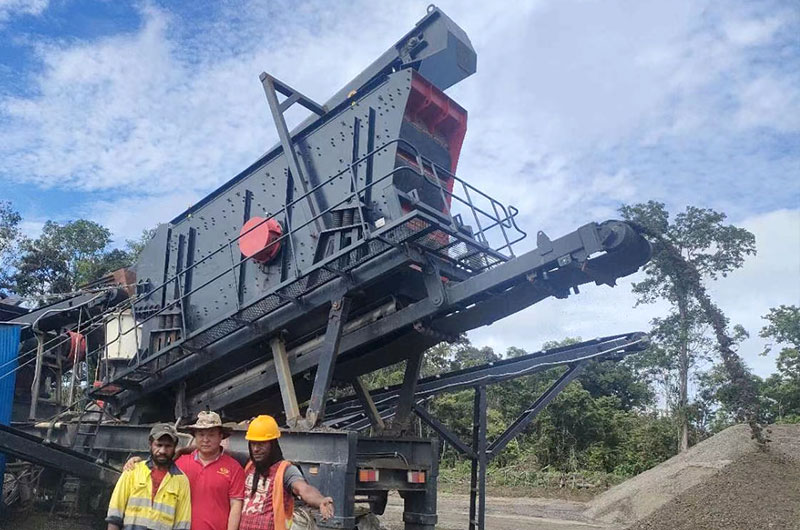
What are the benefits of using a YK circular vibrating screen?
This type of vibrating screen is frequently employed for screening lepidolite ore and can be integrated into a closed circuit with a cone crusher.
It offers high screening efficiency, multiple specifications for screening, and multiple layers.
Lepidolite grinding equipment
To ensure the separation of lithium minerals and gangue minerals, a closed-circuit grinding and grading process is used. Ideally, the lepidolite should be ground to a particle size of -0.074 mm, comprising 70%-80% of the total.
Wet ball mill
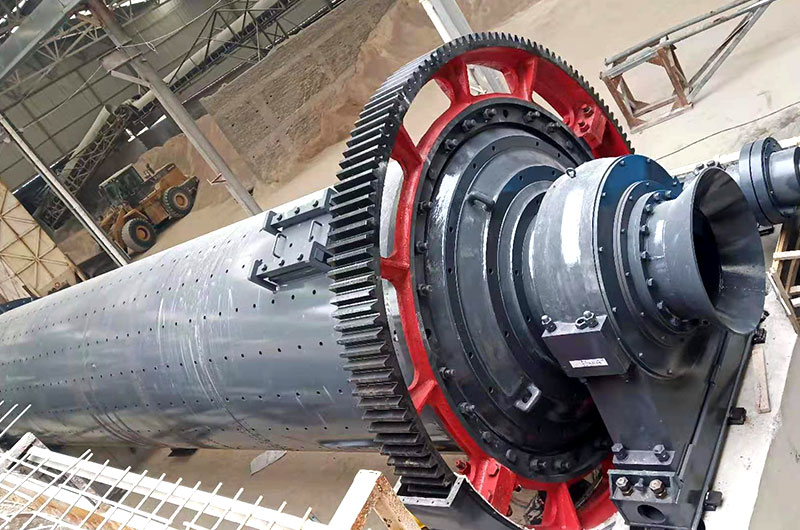
Why use a wet ball mill?
A wet grid ball mill is chosen as the grinding equipment for lepidolite, equipped with a discharge grid plate to prevent excessive grinding.
The design of a large discharge port enhances the processing capacity for lepidolite, resulting in an output range of 0.65-615 t/h.
It boasts high grinding efficiency and easy control over particle size, with an achievable fineness of 0.074-0.4 mm.
The barrel can be lined with either manganese steel or rubber, both offering excellent wear resistance.
Hydrocyclone
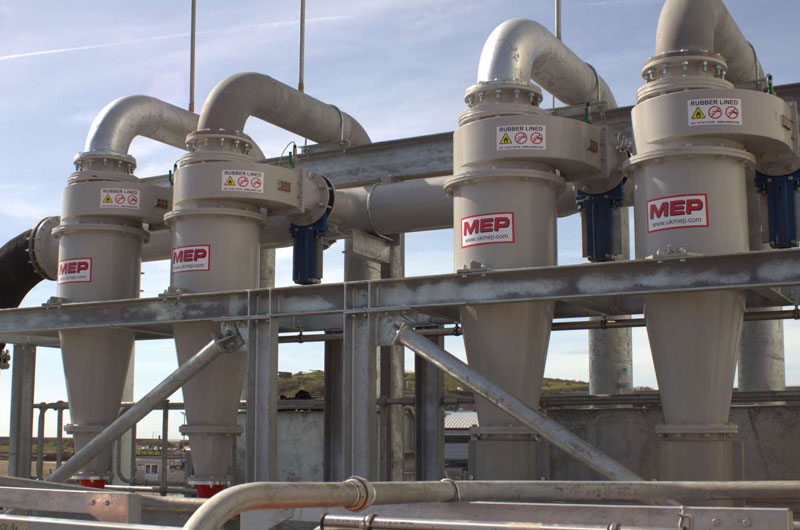
Why should you use a hydrocyclone?
A hydrocyclone is used to classify lepidolite powder by creating a swirling flow.
It effectively removes fine particles, silt, and impurities from lepidolite slurry, ensuring optimal conditions for flotation.
With high classification efficiency of 80%-90% and low energy consumption.
Lepidolite separation equipment
Due to the presence of various associated minerals, it is essential to consider the comprehensive ore recycling for lepidolite. During the separation process, flotation is primarily employed for lepidolite, along with a combination of gravity and magnetic separation methods.
Flotation machine (required)
The majority of lepidolite ores are fine-grained and embedded, often found in association with gangue minerals like quartz and feldspar. Lepidolite has a layered silicate structure that exhibits good buoyancy. Unlike mica minerals, feldspar and quartz have lower floatability, making positive flotation the preferred method.
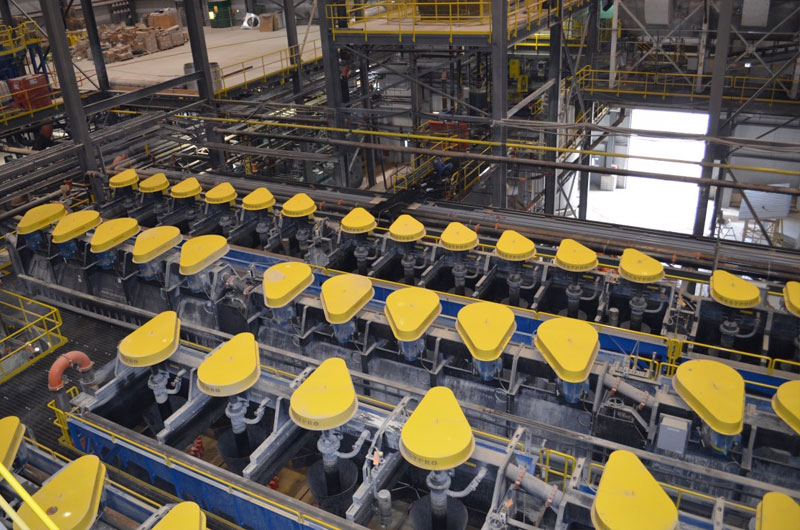
Why should SF and BF flotation machines be used?
Lepidolite pulp is roughed once using a JJF flotation machine, and then fine selected twice using two SF flotation machines.
Flotation machines are perfect for separating fine particles of lepidolite from gangue minerals.
The separation efficiency is high, making it easy to recover lepidolite concentrates of the desired grade.
Float lepidolite first, followed by spodumene, and finally feldspar. The steps are as follows:
1 Float lithium mica with cations in a weakly acidic medium.
2 Concentrate the tailings to 50% solids, mix them with an oleic acid collector and alcohol foaming agent, dilute them to 17% solids, and float spodumene.
3 Treat the flotation tailings with hydrofluoric acid, then add a cationic collector to float feldspar.
Magnetic separator (auxiliary)
Lepidolite magnetic separation is an additional method used to enhance the quality of lithium concentrates. When flotation yields lithium concentrates with high iron content, strong magnetic separation is employed to obtain low-iron lithium concentrates.
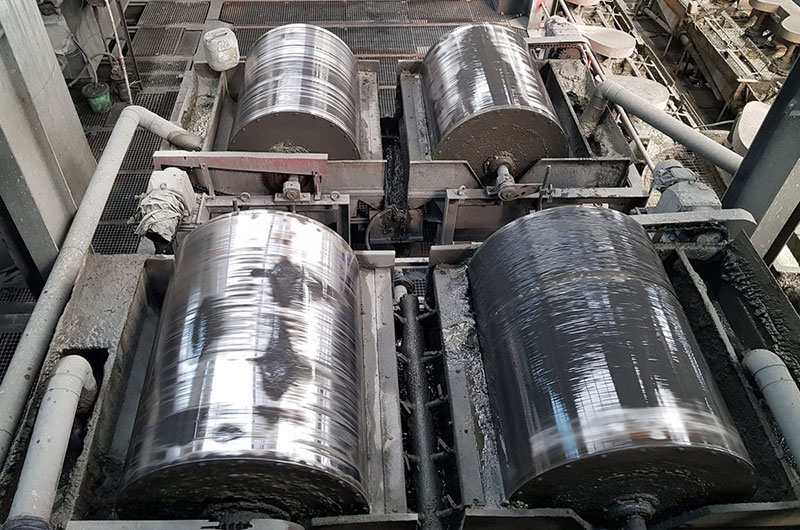
Why should a strong magnetic separator be used?
The majority of the minerals in lepidolite ore are weakly magnetic, necessitating the use of a strong magnetic separator. This is done to eliminate any magnetic minerals or iron-containing impurities from the lithium concentrate by exploiting the differences in their magnetism.
Shaking table
For lepidolite ore containing tantalum and niobium minerals, we use a combination of flotation and gravity separation. At this stage, the recommended gravity equipment is a shaker.
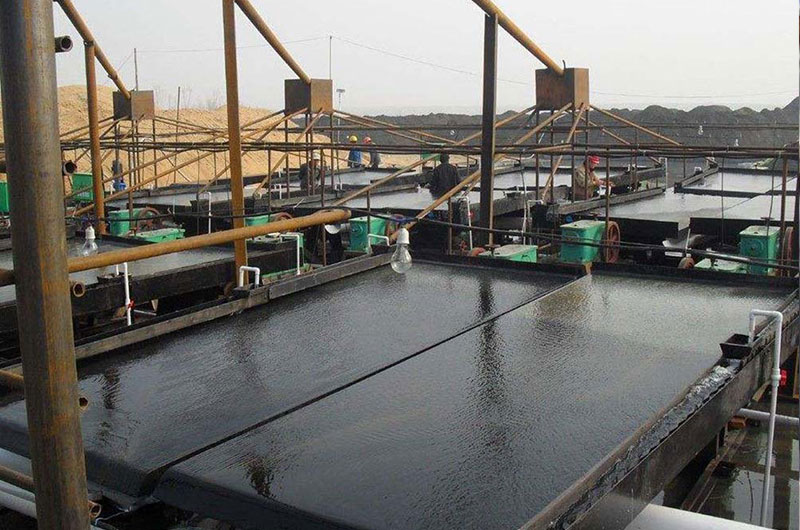
Why should one use a shaking table?
By utilizing the gravitational force of a shaking table, the separation efficiency for recovering tantalum and niobium minerals with high specific gravity is significantly enhanced.
Enhance the value by extracting valuable minerals from lepidolite tailings.
Dehydration equipment of lepidolite
To obtain high-quality lithium concentrates, it is necessary to dehydrate them along with the by-products after sorting. In this case, opting for a high-efficiency thickener is recommended.
High-efficiency concentrator
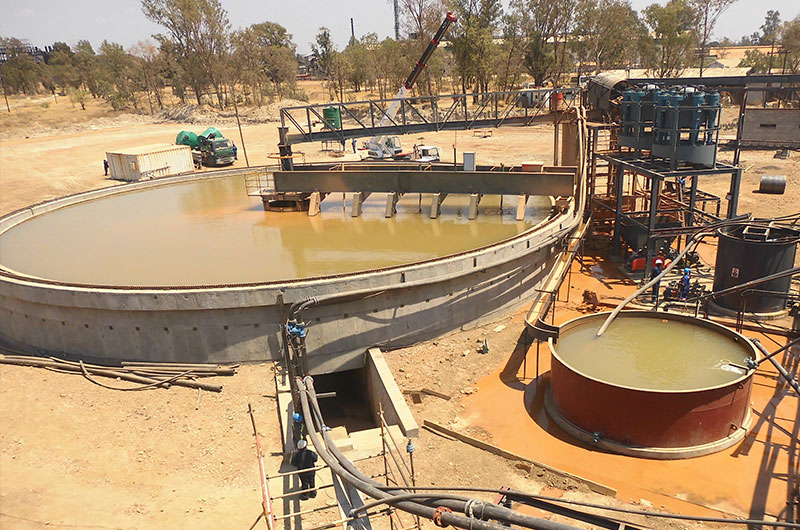
Why should you use a high-efficiency concentrator?
The concentrator removes water from lithium concentrates after separation, reducing the water content to below 15%.
Incorporate inclined plates to decrease the distance for ore particles to settle and increase the sedimentation area.
It offers a large processing capacity per unit, quick dehydration speed, and reduced energy consumption.
Conclusion
The price of lithium has significantly increased, and lepidolite has become an important factor in the lithium industry. The most pressing concern for investors is how to effectively conduct lithium ore beneficiation.
Lepidolite concentrates and by-products (such as spodumene or tantalum-niobium concentrates) can be recovered through methods like flotation, flotation-magnetic separation, or flotation-gravity separation. The choice of equipment model will depend on the requirements of the lepidolite processing plants.
If you are interested in ordering, please contact us
PHONE NUMBER
+86-15836546239(WhatsApp)