The goal of ore beneficiation, or mineral processing, is to maximize the economic value of the extracted minerals by increasing the concentration of valuable minerals and removing impurities.
Ore beneficiation can extract the following materials
Metallic ores: Iron, copper, gold, silver, lead, zinc, nickel, lithium, and tin.
Non-Metallic ores: Phosphate, potash, limestone, graphite, barite, gypsum, talc, and kaolin.
Industrial minerals: Quartz, feldspar, mica, asbestos, vermiculite, wollastonite, and diatomite.
Others: Coal, slag, tailings.
Considerations for ore beneficiation plants
When choosing a suitable beneficiation plant, several factors should be taken into account to ensure its effectiveness, efficiency, and compatibility with the specific ore and project requirements.
Factors to consider include: ore characteristics, desired end product, throughput capacity, process flexibility, capital and operating costs, environmental considerations, infrastructure and site requirements, regulatory and social factors, tailings management.
Guogao Machinery’s engineers can comprehensively consider these factors to design an economical and feasible ore processing flowsheet and provide corresponding mineral processing machines for customers.
Our ore beneficiation plants are sold in many countries such as India, Australia, USA , UK , Canada , Switzerland , Philippines , Malaysia , Thailand , South Africa , Sudan , Egypt Kenya Indonesia Nigeria etc.
What is the process of ore beneficiation?
While the specific steps can vary depending on the type of ore and desired end product, here is a generalized step-by-step process in mineral processing:
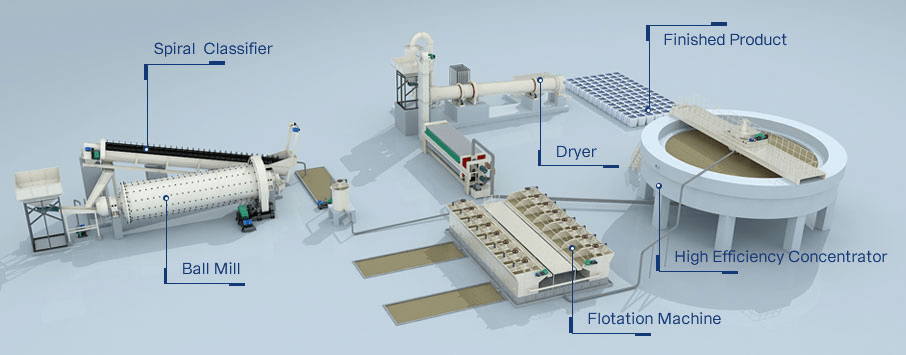
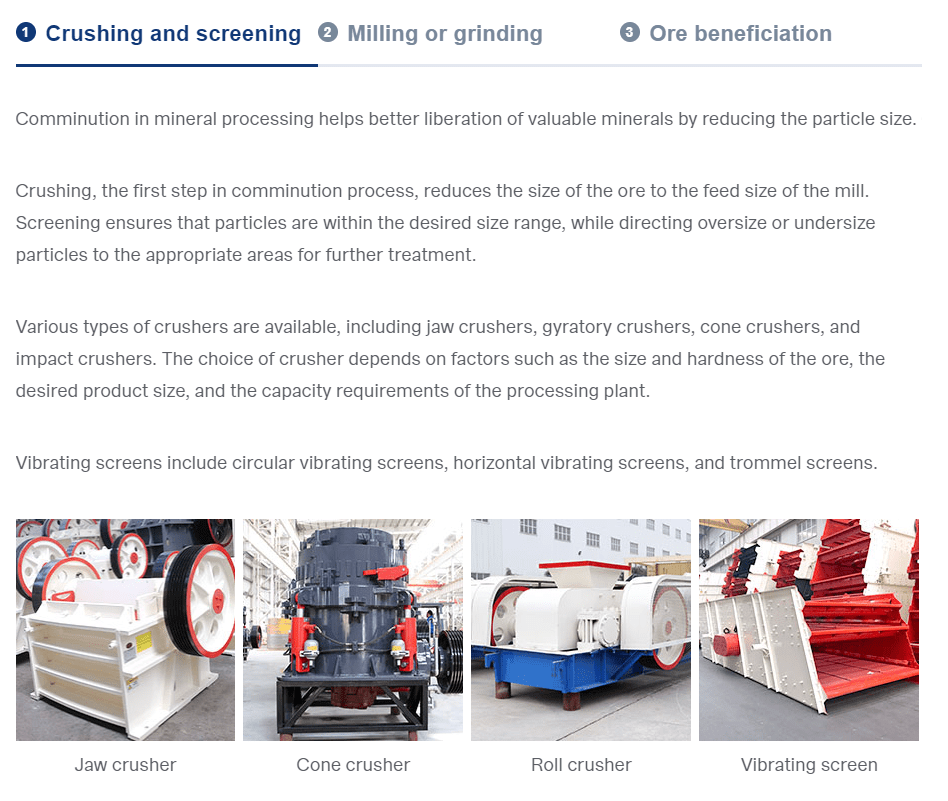
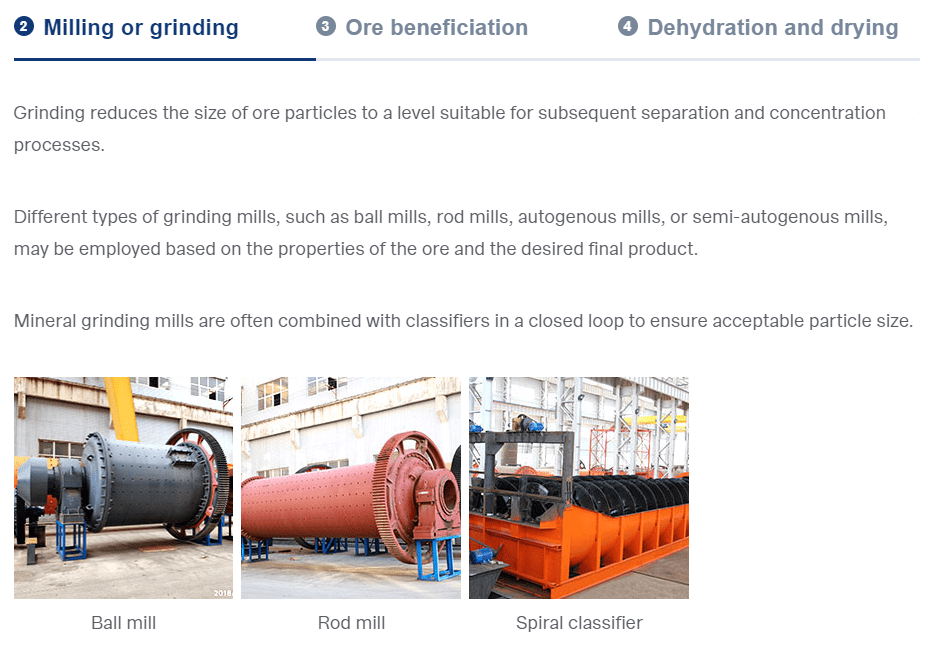
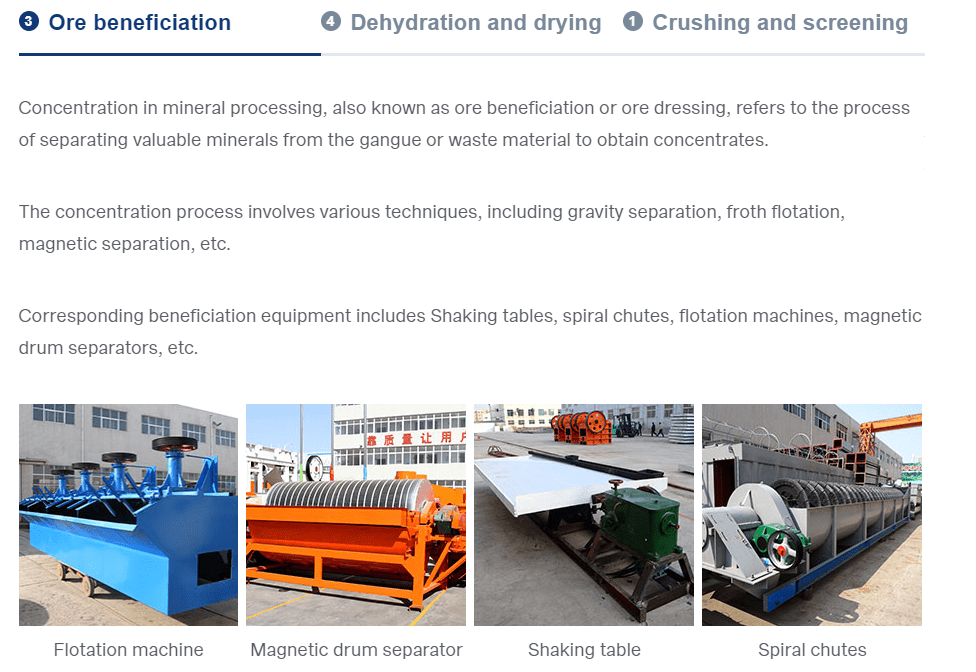
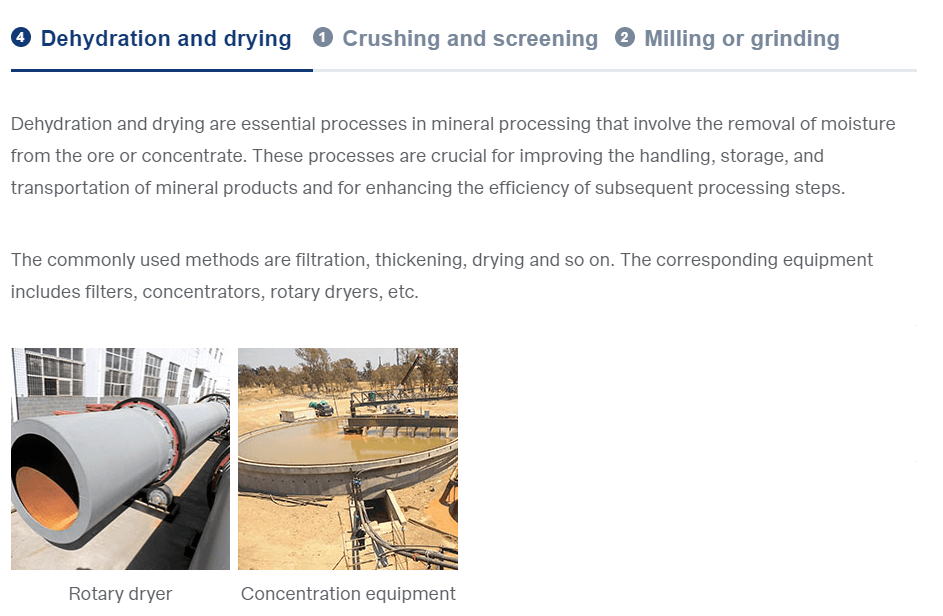
Gugao mine offers customized ore beneficiation processes to customers. This includes adjusting the process flow, selecting suitable equipment, optimizing process parameters, tailings management strategies customization, and implementing automation and control systems.
Now we will present successful cases of various ore beneficiation plants. These cases will include estimated costs, layout designs, and the final product’s effectiveness.
5 TPH low-grade gold ore beneficiation plant in DRC
Beneficiation method | Flotation separation |
Total gold recovery rate | 76% |
Machines needed in the plant:GZD-650×2300 vibrating feeder,PE-150×250 jaw crusher,B500×22 m belt conveyor, 2YK1225 inclined vibrating screen, MBS1224rod mill, FG-3 spial classifier,XJK type flotation machine, |
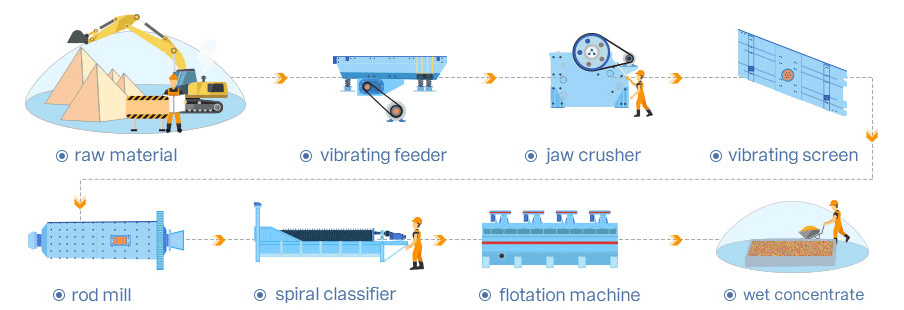
“For low-grade gold ore, this production line finally helped me achieve a recovery rate of 76%, which really surprised me.”
10 TPH gold ore beneficiation plant in tansania
Capacity | 5 TPH |
Raw material | gold ore |
Estimated cost | $ 30000 |
Ore grade | 1.4 g/t |
Feeding size | 100mm |
Beneficiation method | Flotation separation |
Total gold recovery rate | 76% |
Machines needed in the plant:GZD-650×2300 vibrating feeder,PE-150×250 jaw crusher,B500×22 m belt conveyor, 2YK1225 inclined vibrating screen, MBS1224rod mill, FG-3 spial classifier,XJK type flotation machine, |

“The gold ore gravity separating method is not only low in cost but also efficient and no harmful to the environment.”
20TPH gold ore beneficiation plant in Ghana
Capacity | 20 t/h |
Raw material | gold ore |
Estimated investment | $63500-85000$ |
Before beneficiation: grade(t/g) | After beneficiation: recoveryrate(%) | |
Gold concentrate | 33.35 | 81.80 |
Tails | 0.68 | 9.38 |
Raw gold ore | 3.32 | 100 |
Gold concentrate | 34.38 | 90.62 |
Tails | 0.34 | 19.20 |
Raw gold ore | 3.30 | 100 |
Needed equipment: GZD-650×2300 vibrating feeder,Φ1200 cone crusher,B500x10 m belt conveyor, Ф2200×4500 ball mill,a Fote 2280 Spiral classifier, spiral chute, Shaking table (2 sets) |
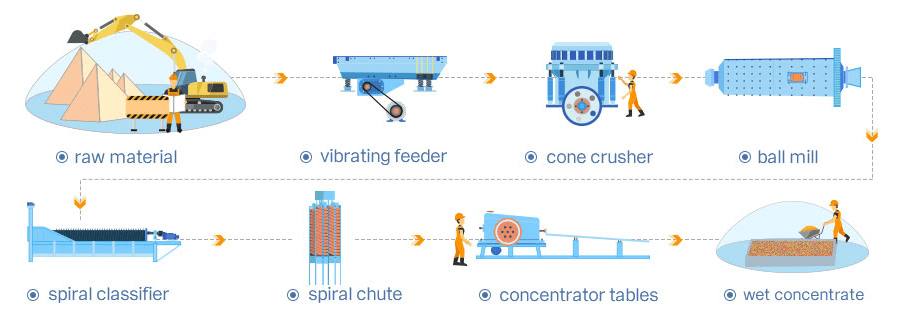
“This mobile gold mine processing line resolved the limitations of my site and saved me 66% in costs.”
10 TPH iron ore beneficiation plant in the india
Capacity | 10 t/h |
Raw material | iron ore |
Estimated investment | 20000$ |
Iron ore grade | Low grade |
Ore beneficiation method | magnetic separation |
Opening size | 65mm |
Concentrate content | 67.81% |
Recovery rate | 92.69% |
This beneficiation plant design: GZD-650×2300 vibrating feeder,PCΦ600×400 hammer crusher,YK1225 circular motion vibrating screen,MBS1830 rod mill, CTB6012 Magnetic drum separator |
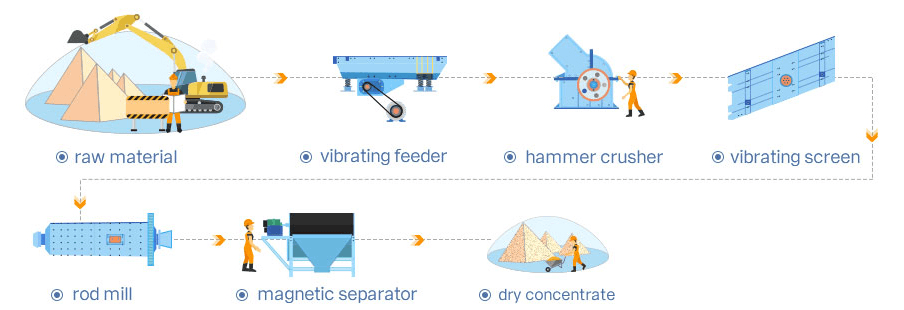
The stage grinding and separation processes are ideal for processing low-grade iron ore. The entire plant helps me minimize energy consumption and costs.
10-50 TPH copper ore beneficiation plant in Zambia
Capacity | 10-50t/h |
Raw material | copper ore |
Estimated investment | $30000-100000$ |
Copper ore grade | 2.5 g/t |
Ore beneficiation method | Flotation separation |
Concentrate content | 44.9% |
Recovery rate | 87.04% |
Ore beneficiation equipment: Customized small mobile jaw crusher, Customized small mobile impact crusher, B500x10m belt conveyor, 2YK1225 circular motion vibrating screen,Ф2200×4500 ball mill,spiral classifier, mixing bucket, JJF type flotation machine. |
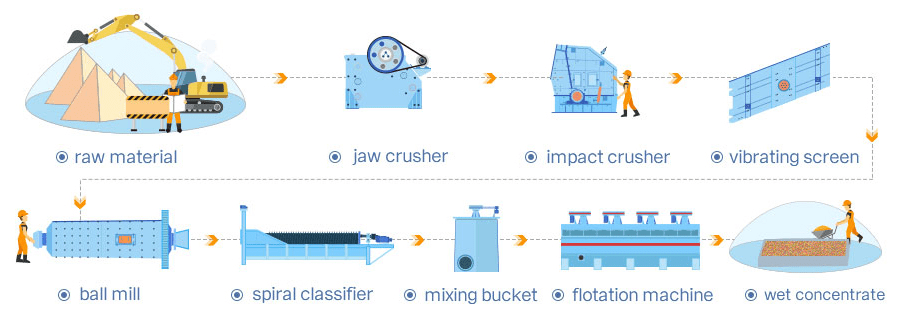
I’m pleased to see that the quality of copper concentrate obtained through this beneficiation method is significantly superior to others.
50-100 TPH manganese ore beneficiation plant in Kenya
Capacity 50-100t/h
Raw material manganese ore
Estimated investment 80000$-120000$
Manganese ore grade 17%
Ore beneficiation method Two-stage high-intensity magnetic separation
Concentrate content 38%
Recovery rate 74%
Manganese beneficiation machines: GZD-850×3000 vibrating feeder,PE-500×750 jaw crusher,Φ1200 cone crusher,B500x10 m belt conveyor, 2YK1535 inclined vibrating screen,Ф2700×4500 ball mill, High-strength Magnetic drum separators
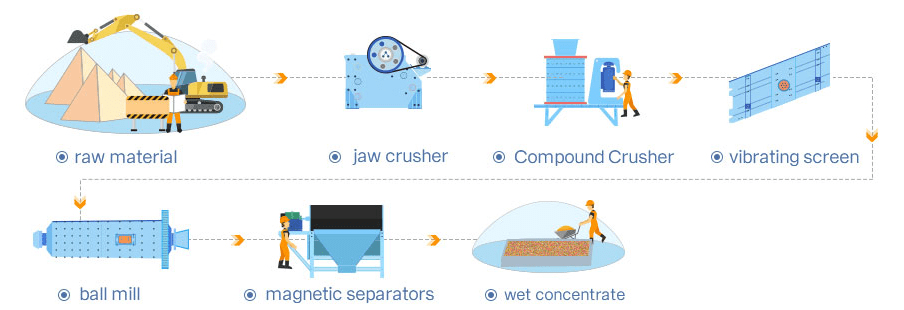
The high output, low cost, and efficient operation yield significant investment returns for me.
150 TPH Bauxite ore beneficiation plant in Australia
Capacity | 150t/h |
Raw material | bauxite ore |
Estimated investment | 150000$ |
bauxite ore grade | 45% |
Feeding size | 0-50mm |
Moisture content | 10-13% |
Ore beneficiation method | magnetic separation |
Concentrate content | 67.9wt% |
Recovery rate | 92% |
Bauxite beneficiation equipment:GZD-1000×3600 vibrating feeder,PE-500×750 jaw crusher,Φ1200 cone crusher, B500x15 m belt conveyor, 2YK1545 vibrating screen,Ф3200×4500 ball mills, CTB1224 Magnetic drum separators. |
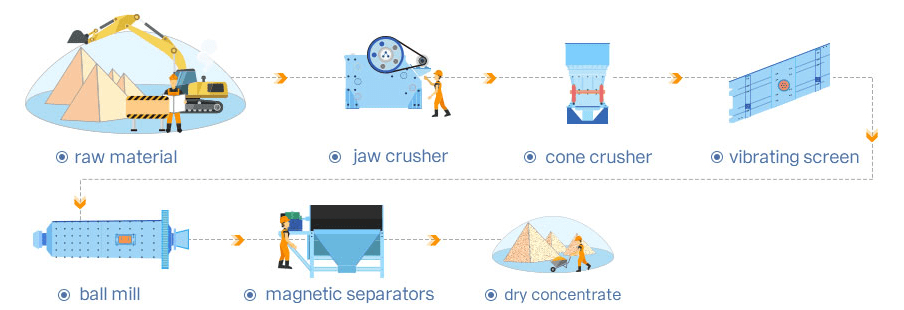
The magnetic separation method helped me remove alumina-silica, alumina-ferrite complexes, iron, and other impurities. Additionally, the entire production line was running smoothly.
50 TPH lateritic nickel ore beneficiation plant in Vietnam
Capacity | 50t/h |
Raw material | lateritic nickel ore |
Estimated investment | 150000$ |
lateritic nickel ore grade | 1.29 wt% |
Ore beneficiation method | Wet magnetic separation and forth flotation |
Concentrate content | 8.3% |
Recovery rate | 92% |
Manganese beneficiation machines: GZD-650×2300 vibrating feeder, PE-500×750 jaw crusher,2PG1060 roll crusher,B500x16 m belt conveyor, B500x15 m belt conveyor, 3YK1230 vibrating screen,Ф2100×7000 ball mill,mixing bucket, a CTB9018 Magnetic drum separator, a SF type flotation machine, a Φ3.2×25 rotary dryer. |
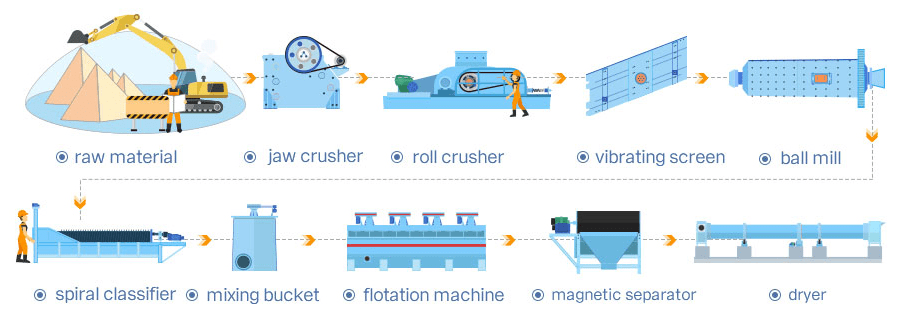
By employing wet grinding and efficient beneficiation methods, the recovery rate of laterite ore is significantly enhanced.
200 TPH zinc & lead ore beneficiation plant in Zimbabwe
Capacity | 200t/h |
Raw material | zinc & lead ore |
Estimated investment | 250000$ |
zinc & lead ore grade | Zinc 12% lead 9.05% |
Ore beneficiation method | Flotation separation |
Lead recovery rate | 72% |
Zinc recovery rate | 55% |
Total recover rate | 87.04% |
zinc & lead ore beneficiation machines: Φ1200 cone crusher, 2YK1848 vibrating screen, Ф3600×6000 ball mills, spiral classfier, a JJF type flotation machines, concentrater, a Φ3.6×28 slag dryer. |
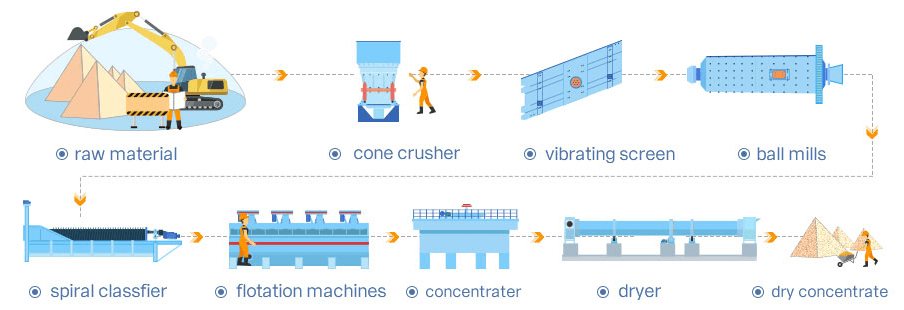
This line boasts powerful processing capabilities. Tailings processed by the coarse flotation machine no longer require further ball mill treatment, resulting in significant energy savings.
250 TPH chrome ore beneficiation plant in Russia
Capacity | 250t/h |
Raw material | chrome ore |
Estimated investment | 270000$ |
chrome ore grade | 44% |
Ore beneficiation method | Gravity and flotation separation |
recovery rate | 97.4% |
Chrome ore beneficiation machines: GZD-1100×3600 vibrating feeder, PE-750×1060 jaw crusher, FTMHP200 hydraulic cone crusher, B500x44 m belt conveyor, 2YK1848 vibrating screen, Ф3600×6000 ball mills, mixing bucket, FG-5 spiral classifier, JJF type flotation machine, Grit concentrator tables, a NZS-12 high efficiency concentrator. |
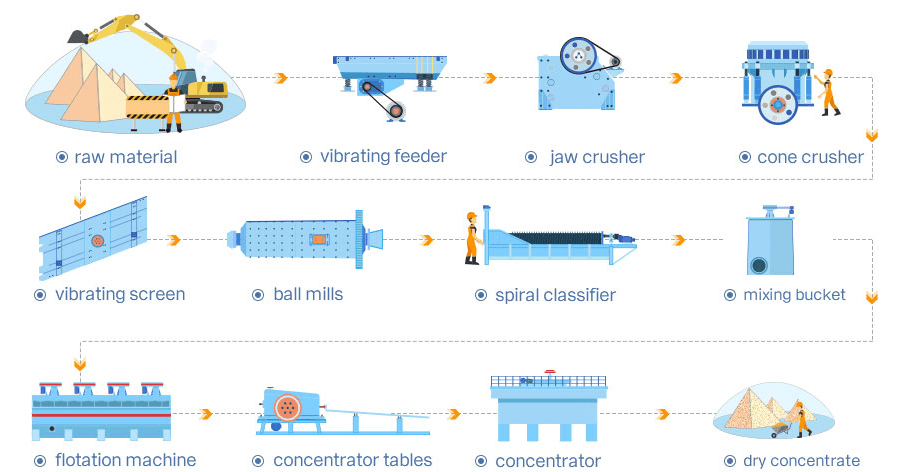
The process is highly effective as it rapidly extracts chromium concentrate, with minimal grinding time required.