Lithium ore is a versatile metal energy resource with various uses, including manufacturing glass, ceramics, and batteries. It is also crucial for high-energy lithium batteries and controlled thermonuclear reactions, making it an essential raw material for long-term energy supply.
Types of Global Lithium Mines
Global lithium mines can be categorized into three types: salt lake brine lithium mines, pegmatite lithium mines, and sedimentary lithium mines. Pegmatite and sedimentary lithium mines are solid deposits among these distribution types. Salt lake brine-type lithium minerals have a high development and utilization rate and play a vital role in the production of lithium compounds.
Types of Lithium Ore Ball Mills
Lithium resources are mainly extracted from pegmatite ores and salt lake brine. Extracting lithium from brine is simple, with a high recovery rate, low cost, and minimal environmental pollution. However, the availability of lithium resources in salt lake brines is gradually decreasing. Therefore, extracting lithium from pegmatite ores has become crucial for obtaining these resources. Various methods can be used to extract lithium minerals from this type of ore such as sulfuric acid roasting, sulfate roasting chloride roasting etc., but grinding before extraction remains an indispensable step
The grate ball mill is commonly used in lithium ore processing to effectively extract lithium resources. It is responsible for grinding coarser minerals and is mainly used in one-stage grinding operations. With its unique ore discharge plate design, the ball mill allows for a large ore discharge particle size and reduces grinding blockage.
This horizontal cylindrical rotating device has an outer edge gear transmission and two chambers. The material enters the first chamber evenly and spirally from the feeding device through the feeding hollow shaft. The chamber is lined with a ladder or corrugated lining, and steel balls of different specifications are installed inside. As the cylinder rotates, centrifugal force brings the steel balls to a certain height before they fall, resulting in heavy impact and grinding on the material.
Once coarse grinding is achieved in the first chamber, the materials enter the second chamber through a single-layer partition plate. This chamber contains a flat lining plate and steel balls for further grinding of materials. Finally, powdery material is discharged through the grate plate to complete the grinding operation.
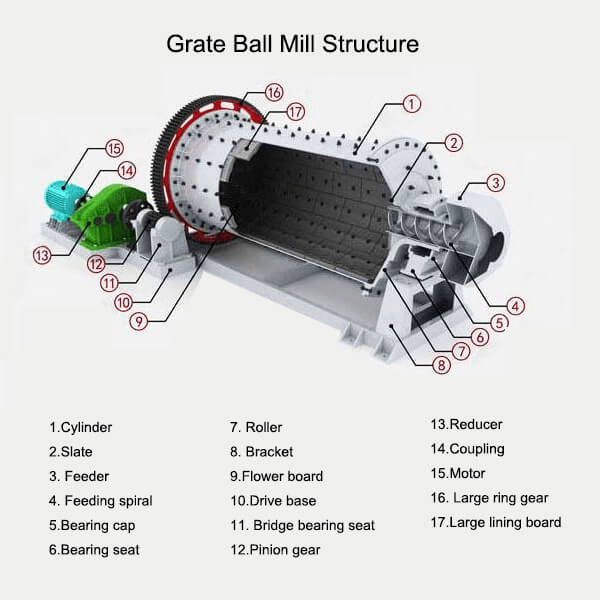
The grate ball mill consists of the feeding part, discharging part, rotating part, transmission part (reducer, small transmission gear, motor, electronic control), and other main components. The hollow shaft is made of cast steel with a removable inner lining. The rotating gear is hobbed from castings. The cylinder is lined with a wear-resistant plate that has good wear resistance. The grate ball mill operates smoothly and reliably. With the presence of the grid plate, it can accommodate more balls and facilitate loading of smaller balls. The productivity of the lattice ball mill is about 20% to 30% higher than that of the overflow ball mill.
- Overflow ball mill for lithium ore
This type of ball mill differs from the grate ball mill in that it does not have a grid plate design at the ore discharge area. When discharging ore, it relies mainly on continuous feeding of ore slurry to push out the ground ore slurry so that it gradually moves towards the ore discharge section. Once the slurry exceeds the overflow weir, it is discharged. Overflow ball mills are primarily suitable for grinding finer minerals in lithium ore dressing plants and are mainly used in second-stage or concentrate grinding operations.
The overflow ball mill is commonly used as a grinding machine in mineral processing plants. It consists mainly of a cylinder, end cover, main bearing, hollow journal, transmission gear,and ore feeder.The barrel oftheoverflowballmillisweldedwithasteelplatewithathicknessof15-36mm.Caststeelflangesareweldedto both ends ofthebarrel.Theendcoverandtheflangeareconnectedwithbolts.Thetwo mustbefinelymachinedandfittedasthehollowjournalcarryingthemassofthegrinderis weldedtotheendcap.Thereare1-2manholesonthecylinderforinspectionandliningreplacement.Lining platesarelaidinsidethebarrelandendcover.Themainbearingsupportsthehollowjournalonthe end cover. The main bearing is commonly used as a sliding bearing with a large diameter but short length. The bearing bush is cast with Babbitt alloy. It differs from ordinary sliding bearings in that only the lower half has a bearing bush. The entire bearing is cast iron except the bearing bush, which is cast with babbit gold.
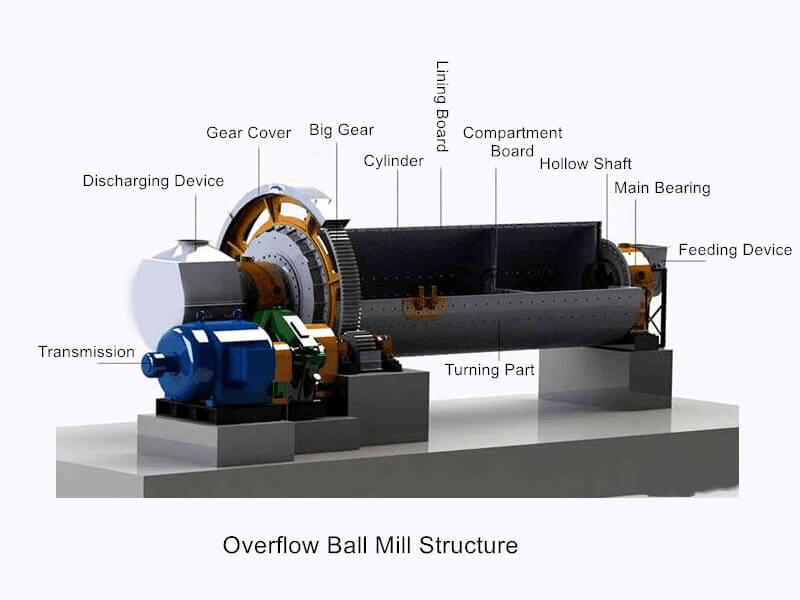
When the ball mill is operating, material is loaded into the cylinder through the hollow shaft at the feed end. As the cylinder rotates, the grinding body attached to the lining plate is removed by inertia, centrifugal force, and friction. When brought to a certain height, it falls due to gravity and crushes materials in the cylinder like a projectile. The material enters evenly and spirally into the first warehouse of the ball mill through a feeding device connected to a hollow shaft. This warehouse has ladder or corrugated linings with steel balls of different specifications inside. The rotation of the cylinder generates centrifugal force that propels steel balls to fall from a certain height, producing a strong impact and grinding effect on materials. After coarse grinding in the first warehouse, materials enter the second warehouse through a single-layer partition board. This warehouse has flat lining plates and steel balls for further grinding. Finally, powdery material is discharged through a grate plate to complete the grinding operation.
- Long-barrel ball mill for lithium ore
The long-cylinder ball mill features an elongated barrel much larger than its diameter. The interior can be divided into 2 or multiple chambers (usually up to four). Each chamber’s length depends on specific grinding conditions. This type of ball mill is used in lithium ore dressing operations and finds application in fine-grinding processes within factories.
4.Energy-saving ball mill for lithium ore
The energy-saving ball mill is an innovation based on traditional grid or overflow mills.It replaces their transmission device with one that operates at lower speeds,reducing overall energy consumption by approximately 30%. Additionally,it incorporates spray lubrication systems for both large and small gears,to effectively address lubrication issues.It also includes hydraulic jacking devices which allow manipulation of hydraulic jacks during maintenance procedures,enabling precise adjustment of horizontal position.Customized lining plates suitable for lithium ore are employed,to enhance wear resistance,and extend service life