Ilmenite is a mineral that consists of titanium iron oxide, with the chemical formula FeTiO3. It is considered one of the most crucial titanium ores, as titanium is a metal renowned for its exceptional strength, resistance to corrosion, and low density. Typically found in igneous rocks and sedimentary deposits, ilmenite appears as black or dark brown crystals or grains. The significance of ilmenite lies in its role as a primary source of titanium—a valuable metal extensively used in today’s industrial world. The demand for titanium continues to increase due to its unique combination of properties, making it an indispensable material in various high-tech and industrial applications.
Common Ilmenite Beneficiation Methods
I, lmenite Gravity Separation
The gravity separation method is used to remove gangue minerals from the crushed ilmenite ore. This process involves utilizing equipment such as jigs, spiral chutes, shaking tables, and others. It is primarily effective for coarse-grained ilmenite.
- Ilmenite Magnetic Separation
Due to its weak magnetism, ilmenite can be separated from non-magnetic minerals through magnetic separation. Inadequate magnetic field strength during this process may result in the discarding of some ilmenite minerals, leading to decreased resource utilization efficiency. Therefore, the magnetic field strength plays a crucial role in the magnetic separation process of ilmenite.
Ilmenite primarily exists as a complex solid solution within deposits and quickly generates ilmenite flakes with a higher magnetization coefficient. This increased difference in magnetization between the gangue facilitates easy magnetic separation. Some ilmenite sand ores contain significant impurities and sludge. After initial grinding, weak magnetic separation can be employed to separate the iron ore, followed by strong magnetic separation to separate the titanium ore and enhance ore recovery.
- Ilmenite Flotation
Flotation is a commonly used method for separating ilmenite, which can be categorized into conventional flotation, flocculation flotation, agglomeration flotation, and carrier flotation.
Conventional flotation
Traditional methods for ilmenite beneficiation typically employ collectors such as oleic acid, oxidized paraffin soap, and tar oil. The combination and ratio of these collectors can be determined based on the mineral composition. For instance, ores containing both ilmenite and titanium pyroxene can be separated using new collectors to enhance ore grade.
Flocculation flotation
The flocculation and flotation method for ilmenite can be categorized into selective flocculation and flotation methods, as well as hydrophobic flocculation and flotation methods. These are primarily used for finer particle sizes of ilmenite. Selective flocculation and flotation condense one mineral before gradually separating it into a slurry with two or more minerals. Hydrophobic flocculation and flotation utilize the mutual hydrophobic interaction of mineral particles to form separate clusters.
Agglomeration flotation
The agglomeration flotation method for ilmenite involves using a collector that adsorbs onto the surface of ilmenite particles, rendering them hydrophobic. Capillary attraction from bridging liquid is then utilized to agglomerate the ore particles, achieving successful ilmenite flotation. This method is suitable for finer particle size ilmenite. Attention must be given to collector usage and stirring intensity as they directly impact the recovery of ilmenite.
Combined Ilmenite Separation
Ilmenites often contain various minerals and impurities like rutile and titanite. To improve mineral grade, recovery rate, and achieve comprehensive utilization of minerals, combined beneficiation methods yield better results compared to single methods alone. Commonly used combined techniques include magnetic separation-flotation; gravity separation-flotation; magnetic separation-gravity separation; gravity separation-magnetic separation-flotation-electrical separation.
Magnetic separation – Flotation
This processing technique first magnetically separates the ilmenites to eliminate unwanted gangue minerals before floating the magnetically separated concentrate to enhance the grade and recovery rate of ilmenite concentrate.
Gravity separation – Flotation
The gravity separation-flotation method exhibits good selectivity for ilmenite with a raw ore grade below 6%. It can also separate sulfur in ilmenite, improving the utilization rate of ilmenite resources.
Magnetic separation – Gravity separation
Combining magnetic separation and gravity separation reduces production costs, improves concentrate grade and recovery rate of ilmenite, and enhances production efficiency.
Gravity separation – Magnetic separation – Flotation – Electrical Separation
Suppose the gangue minerals in the ilmenites include titanium pyroxene, plagioclase, sulfide minerals, etc. In that case, plagioclase can be removed through gravity separation first. The flotation method can be employed for desulfurization while electric separation removes titanium pyroxene. This approach offers a better solution for low-grade ilmenites by enhancing their grade and utilization.
The above methods represent various approaches to ilmenite beneficiation. Due to the complex composition of actual ores, relying solely on experience is insufficient when determining process flow. It is recommended to analyze mineral composition and properties through mineral processing tests and formulate scientifically sound plans based on test results.
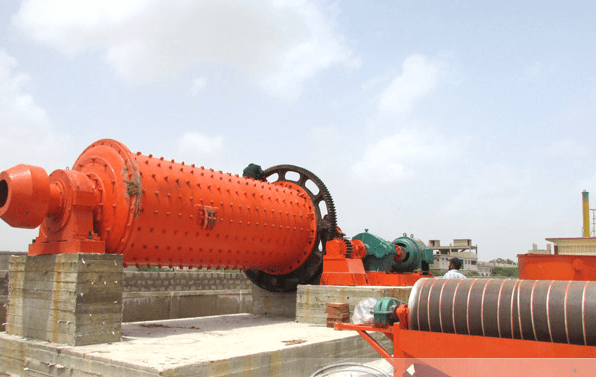