CIL (Carbon in Leach) is a widely used method for extracting gold from ore. It involves crushing and grinding the gold ore into a fine powder, then mixing it with a cyanide solution to create a slurry. The cyanide solution reacts with the gold in the ore, forming soluble gold-cyanide complexes. This slurry is passed through activated carbon adsorption tanks, where the activated carbon adsorbs the gold-cyanide complexes, effectively concentrating the gold. Afterward, the carbon is subjected to elution using a hot concentrated cyanide solution to strip the gold from it. The resulting gold-cyanide solution undergoes electrowinning or smelting to recover the gold and produce either cathodes or bars/bullion. CIL has advantages such as high recovery rates for low-grade and complex ores, efficient adsorption of gold by activated carbon, versatility for different types of ores and processing conditions, cost-effectiveness compared to methods like CIP (Carbon in Pulp), and environmental considerations that minimize cyanide release into the environment. The CIL process includes crushing and grinding of ore into powder form, followed by cyanide leaching to dissolve the gold. Adsorption onto activated carbon occurs next before elution strips off the loaded carbon’s captured gold content. Electrowinning or smelting are then employed depending on which recovery method is chosen. Finally, refining produces high-purity gold from recovered material. While CIL is proven effective and widely used in mining due to its efficiency and adaptability, adhering to safety guidelines and considering environmental factors during implementation are crucially important.
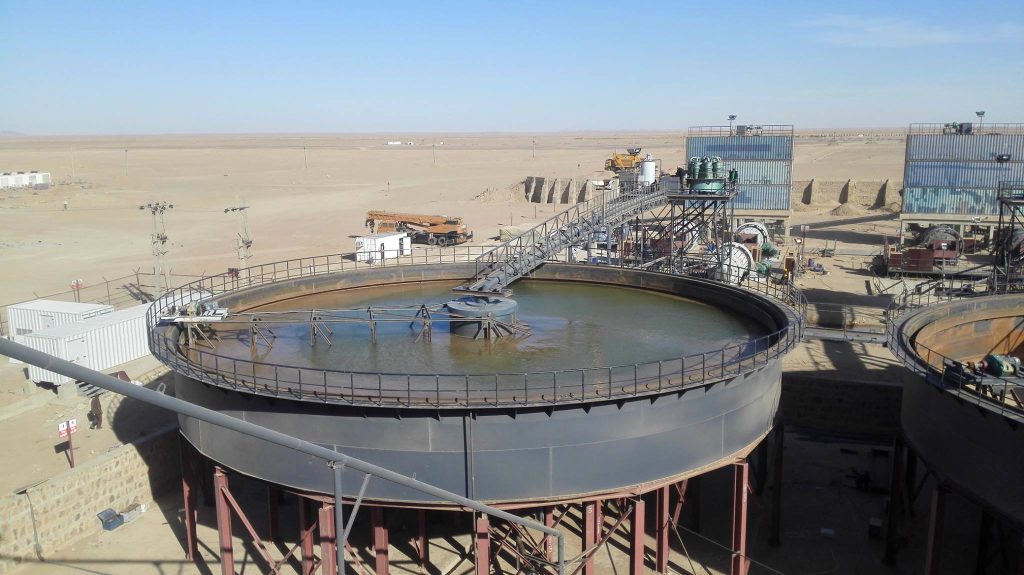
CIL Processing Line Chemicals List
CIL processing lines for gold mines typically require chemicals to extract and process the gold ore. Here is a list of commonly used chemicals on CIL treatment lines:
- Sodium Cyanide (NaCN): Primary agent for dissolving gold and silver.
- Oxidizing agent (e.g., oxygen or hydrogen peroxide): Used with sodium cyanide to promote oxidation and dissolution of gold.
- Lime (CaO): Adjusts solution pH to maintain proper alkaline conditions.
- Sodium Hydroxide (NaOH): Adjusts pH and maintains alkaline conditions.
- Sodium hypochlorite (NaClO): Oxidizes gold and silver, promoting their dissolution.
- Activated carbon: Adsorbs gold and silver ions for subsequent reduction and recovery.
- Polyacrylamide (PAM): Improves solid-liquid separation effect.
- Sulfuric acid (H2SO4): Adjusts acidic conditions in some cases.
- Ammonia (NH3): Adjusts alkaline conditions in some cases.
- Clarifier: Removes suspended solids and impurities.
- Redox Agent: Reduces gold and silver, causing them to precipitate into metals.
-Chelating agents: Increase solubility of gold and silver for easier extraction.
-Dissolution Aid: Speed up the dissolution of gold and silver.
-Anti-Foaming Agent: Controls foam generation to maintain process stability.
Chemicals & Dosage List for 300TPD CIL Plant
Activated Carbon Dosage:
Add carbon at a rate of 10–15 g/L. Prepare an additional 3 tons after adding; activated carbon can be recycled after pickling washing.
Sodium Cyanide Dosage:
Calculated based on 1 kg/ton of ore; specific dosage determined by silver nitrate titration results, maintaining free sodium cyanide concentration at 0.03%–0.05%.
Lime Dosage:
Calculated based on 1 kg/ton of ore; pH value should be controlled at approximately 10.5.
Flocculant Dosage:
Calculated at 30 g/ton of ore; CIL plant requires approximately 9 kg of flocculant per day.
Electrolyte Solution:
- Sodium Hydroxide: 40 kg
- Sodium Cyanide: 80 kg
Electrolyte solubility: sodium hydroxide (1%), sodium cyanide (2%). Test concentration after each electrolysis batch and add cyanide or sodium hydroxide if necessary.
Hydrochloric Acid Dosage:
Used for carbon washing after electrolysis, prepared as a 5% solution in batches of about 30 kilograms. Normally not used, only for cleaning carbon.
Total Water Consumption (clean water + circulating water):
Calculated based on 1.5 tons of water/ton of ore; leaching concentration guaranteed to be between 40% and 45%. Additionally, consider the backwash water from the centrifugal concentrator, which amounts to an extra 80 tons/hour. Therefore, the CIL plant requires a total of 450 tons/day + backwash water from the centrifugal concentrator (80 tons/hour).