Extracting gold from rock can be a complicated process, but there are a few methods that are commonly used. One of the most popular methods is called cyanide leaching. This process involves crushing the rock and then mixing it with a solution of sodium cyanide. The gold particles are then separated from the solution using a variety of methods, such as adsorption onto activated carbon or direct electrowinning. Another method that is sometimes used is called amalgamation, which involves mixing the crushed rock with mercury. The gold particles will then bond with the mercury, creating an amalgam that can be easily separated from the rock. However, it is important to note that both of these methods can be harmful to the environment, and may also pose health risks to workers. It’s crucial to conduct the process under proper regulations and with the necessary precautions
Gold mining underground and the extraction of gold
Although gold is a precious metal that occurs very rarely, it can be found almost everywhere on Earth in the 16-kilometer thick crust. However, the amount of gold in the earth is extremely small, making mining not economically viable. There are two types of gold: primary gold (mined from mountains) and secondary gold (found in streams or as nuggets). Extracting primary gold requires significant effort. Various methods are used to separate the gold particles from the ore extracted underground. The most important method will be described here.
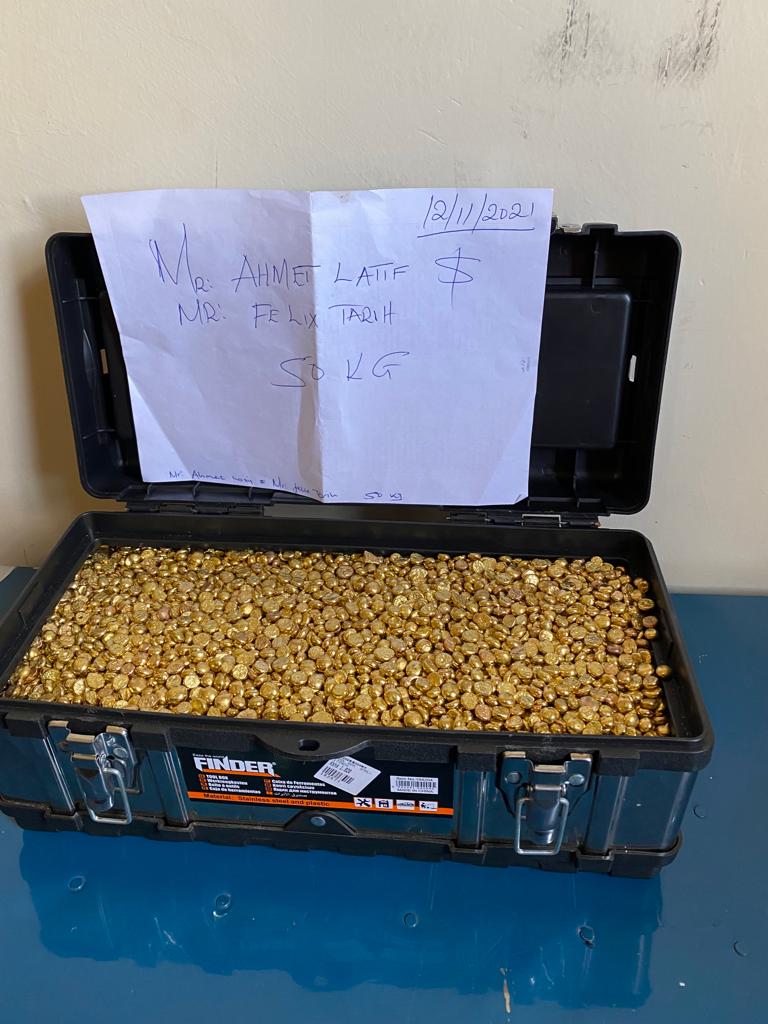
Extraction of Gold by Cyanide Leaching
Cyanide leaching is mainly used when there is a high concentration of gold in the earth, making industrial development worthwhile. In this process, the rock containing gold is crushed into sand and dust. Then, sodium cyanide solution (sodium salt of hydrogen cyanide acid HCN) is combined with the rock dust piled in heaps or stored in tanks. The acid separates the gold from the rock dust and carries it away chemically bound within an acidic fluid seepage. Afterwards, zinc dust is added to filter out and recover the dissolved gold from the leach solution. The recovered raw gold is then washed out and dried before being refined into fine qualitygold.The release of highly poisonous hydrogen cyanide acid during this extraction method raises concerns about its impact on human beings and environment due to its flammability.
Extraction of Gold by Amalgam Process
The amalgam process, which was used since ancient times,is oneofthe oldest technical methods for extractinggold.Withthisprocess,the rock containinggoldis also crushedinto finesand.Thenmercuryisaddedtotherockdust.Goldhasapropertythatallowsittoattachtothesurfaceofmercury.Themercury-enrichedmixtureformsasilveryshiningalloysolutioncalledamalgam.This amalgamprecipitatesatthebottomofthemixingcontainerandcanbeeasilyseparatedfromotherminerals.Subsequently,themercuryisevaporatedbyheatingtheamalgam,leavingbehindpure rawgold.This method also poses health and environmental risks due to the vaporization of highly poisonous mercury.
Extraction of Gold using Electrowinning Process
Electrowinning is a commonly used process for extracting gold without the use of toxic substances. This electrochemical approach takes advantage of the extraction of other precious metals such as copper or zinc, which also contain small quantities of gold in the extracted rock. During the electrolytic cleaning process, an anode activates the precious metal-bearing rock sludge while a cathode made of pure metal collects under it. The gold in the raw rock material does not dissolve during electrolysis and accumulates as a sludge under the anode. Other precious metals like silver, copper, lead, and tin concentrate in this sludge and can be easily separated from each other through suitable processes.
Extraction of Gold using Borax Process
The borax process is another environmentally-friendly method for extracting gold. In this method, the gold-bearing rock material is placed in a melting crucible along with sodium borate (borax). The addition of borax lowers themelting pointoftheoremixture,makingitmorefluid.The lowmeltingpointallowsforcost-effectiveextractionusinglow-powerheat sources.Themoltenmassis then separated by gravity;gold sinks tothe bottomofthecruciblewhileotherrockmaterialslike silicon quartz ore or oxides rise tothetop
The process can be divided into three parts:
- Pre-Separation Stage
- Crushing
- Screening
- Grinding
- Classifying
2. Separation Stage
- Gravity separation
- Flotation Separation
- CIL/CIP gold extraction process
- Heap leaching process
3. After-Separation Stage
- Thickening
- Fitering
- Drying
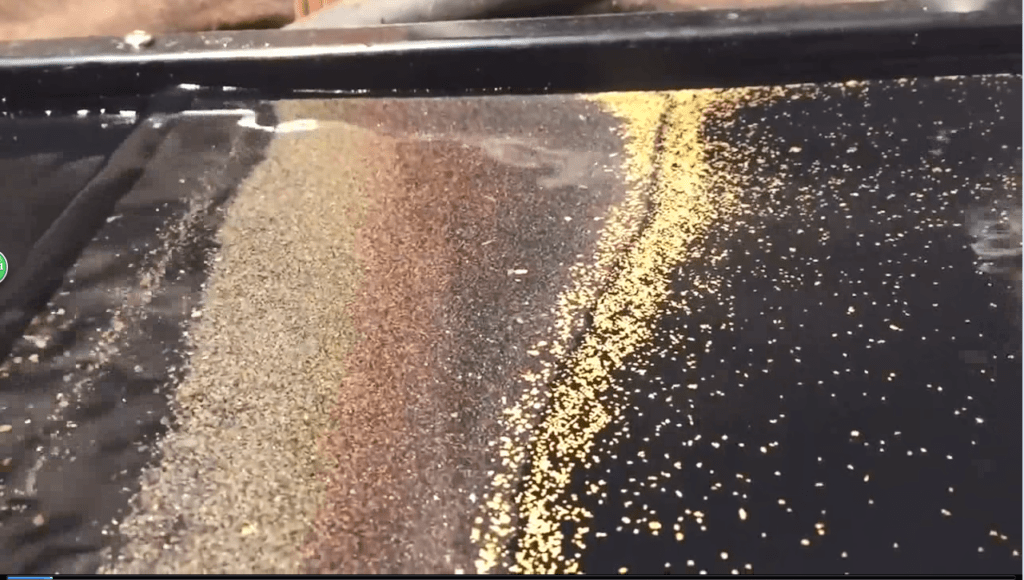
Method for extracting gold from gold ore:
First, single flotation method
Single flotation is suitable for treating coarse and medium-grain natural gold ore. The crushed ore enters the ball mill and is finely ground into a flotation. Sodium carbonate is used as a regulator to float the gold.
Second, gravity dressing
Gravity dressing utilizes the difference in specific gravity between gold and other minerals for flotation. The greater the difference in specific gravity, the easier it is to separate them. The gold-bearing ore is placed in a cylindrical sieve, and high-pressure water flows through it. Gravel sand larger than the sieve holes is transported into the tailing field via belts; while ore sand smaller than the sieve holes goes into sections 1-3 through a distributor. From there, it enters a jig that feeds into a shaker through three stages of concentrate jigs to produce fine sand ore. This method is mainly used for alluvial mines but can also be applied to finely divided ores.
Third, amalgam flotation method
Mercury flotation is suitable for treating natural coarse-grained gold embedded in pyrite and other sulfide ores. Unlike single flotation, after grinding, mercury plates are added for gold recovery with rates reaching 30-45%. The slurry after amalgamation undergoes classification overflow floating. To improve mercury production efficiency, certain concentrations of sodium carbonate and caustic soda are added during grinding to achieve a 70% mercury recovery rate.
Fourth, carbon slurry method
The carbon slurry method involves adsorption of activated carbon while oxidizing and leaching to increase the leaching rate of gold. The process includes two-stage closed-circuit crushing followed by two-stage grinding where 95% of the overflow product passes through a trimmer at 200 mesh size before entering thickener tanks where slurry concentration increases from 18-20% to about 42-45%. From there, it moves on to buffer tanks and then to leaching adsorption tanks for the leaching operation. Activated carbon made from coconut shells is used for adsorption, resulting in loaded gold charcoal as the final product. The tailings are thoroughly sieved with high frequency to recover gold from crushed activated carbon, and then the cyanide-containing tail liquid is treated with liquid chlorine. Gold recovery is achieved through analysis, electrolysis, pickling, and other methods.